As the ‘blue economy’ grows apace, so too does the potential of uncrewed surface vessels (USVs) in the quest to reduce pressure on human capital and improve productivity on the oceans. Furthermore, with the onboarding of artificial intelligence alongside much developed satellite connectivity and navigation, USVs are going further and longer with ever greater reliability and precision.
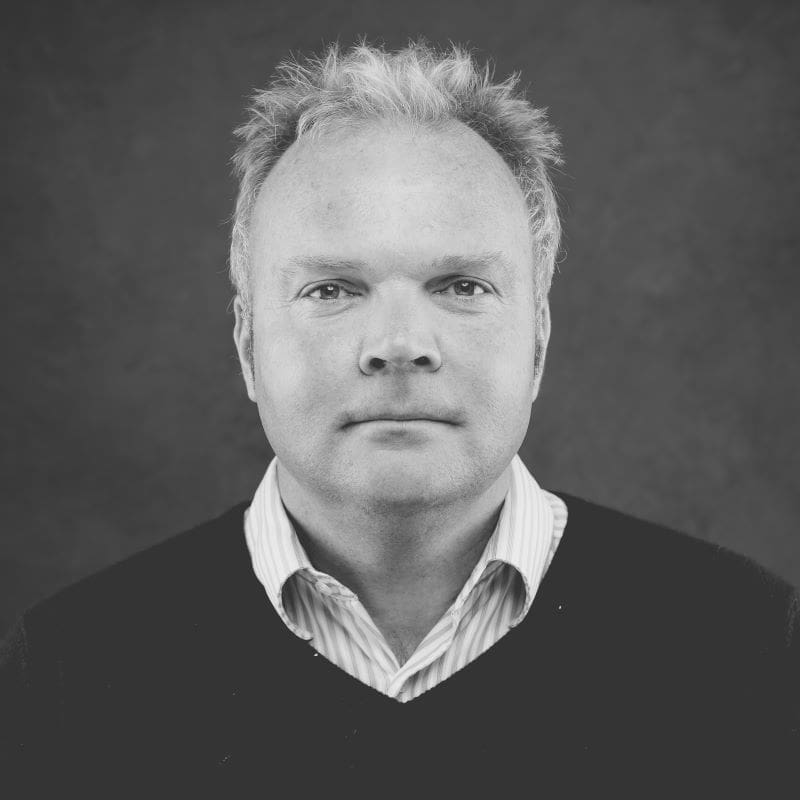
Here, Matthew Ratsey, managing director of the world’s first charter firm for high-endurance USVs, Zero USV, highlights the still untapped potential of USVs, arguing that autonomy on our seas is well on the way to becoming a primary means of completing marine survey and mapping operations.
With its projected value of £3.2 billion by 2050, it’s easy to see why the ‘blue economy’ encompassing so many industries, is spawning a race to deliver smarter, safer and more efficient ways to monitor and understand our oceans.
Fuelled by the drive for Net Zero, coupled with universal desire for energy security in an increasingly uncertain world, is the growth in offshore renewables (wind, tide, wave and thermal) to augment and potentially one day replace existing hydrocarbon energy production.
According to a report by Wood Mackenzie, over the next ten years, global offshore wind capacity alone is projected to increase almost tenfold, from 34GW to 330GW, driving the installation of more than 80,000 new fixed or floating moored turbines. Each of these will require accurate sea-floor data for the life of their installation, potentially for up to 30 years. The marine survey and mapping industry is set to remain in rude health for some years to come.
Indeed, there are many other industries requiring hydrographic and geophysical surveying, from seabed-extraction to utilities, biotechnology, power, telecoms, to subsea wrecks and exploration.
To Crew or not to Crew
Traditionally, marine surveying has relied heavily on crewed vessels. It’s long been the assumption, from navigation itself, to deployment and recovery of sensors, to data-collection, interpretation, and reporting.
The complexity of these tasks in parallel with dealing at the same time with often physically challenging environments might naturally lead one to rule out USVs, and yet the opposite is true as autonomy proves itself increasingly capable of boosting productivity, safety and economy of physical, financial and human resources.
As with all disruptive technologies which challenge tried and tested orthodoxy, the true extent and potential of autonomy in the survey industry is still being revealed, and this will continue as new systems, along with AI and machine learning (ML) enable more human-dependent processes to be completed by machines. And we are already quite a long way down that track, not least around the UK and the Continental Shelf, which provide immediate opportunities to despatch and operate USVs which are fully autonomous, independent of onshore controls.
Similarly, the barriers to operating successfully over-the-horizon USVs for offshore hydrographic and geophysical surveys are rapidly being overcome. As practical concerns are being mitigated, regulatory codes of practice are being adapted and well developed whilst forward-thinking manufacturers are coming up with technical solutions on a pathway to ever greater autonomy and efficiency for the marine survey industry.
My own company, Zero USV, has been at the forefront of this against the backdrop of what already exists on the market, which is vessels operated substantially or only by remote control from the shore. This is not the same as a vessel which is independently capable of maintaining all of its operational functionality in the absence of any form of connectivity, at the same time avoiding shipping, marine mammals, and all other dynamically positioned obstacles.
Breaking tradition with AI
Significant advancements in graphic processor unit (GPU) technology over the past few years have enabled AI software – which controls our fleet – the Oceanus12 class – to be deployed ‘on the edge’, which means the AI models can be deployed on physically small GPUs, which in turn are mounted on the boat. These are relatively small, roughly the size of an A5 box with low electrical consumption, but at the same time extremely powerful machines. This is the significant step change in chip technology led by NVIDIA, which three years ago would still have required a server rack level installation. The edge compute devices with the AI models installed on board ensures enough intelligence is built into the vessel to be able to carry out missions without having to rely or constantly revert to an ‘always on’ satellite connection.
Without delving into specifics here, the electric hybrid powertrain we have developed solves the historic issues of reliability and power optimisation.
Whilst it may still be argued by a few that USVs and marine autonomy is restricted to areas away from structural or geophysical ‘hazards’, I’d argue strongly that this isn’t the case, with advances both in AI and in connectivity technology, particularly in providing robust communications ‘over the horizon’. With the ushering in of low earth orbit (LEO) satellites such as Starlink, and hybrid connectivity solutions hitting the market which bond multiple bearers (4G, LTE, satellite, etc) autonomous navigation and edge collation of survey data are becoming much less of an issue, and certainly this will continue to develop.
When the Mayflower Autonomous Ship project, sponsored by Promare, IBM and other partners, completed its fully autonomous Atlantic crossing in 2022, it was the first autonomous USV to do so. At the heart of the vessel’s onboard AI systems were UK-based software engineering company – Marine AI, who together with the parent company MSubs (responsible for the design and marine engineering), jointly developed the vessel’s capability to traverse the North Atlantic Ocean autonomously, devoid of any human intervention. Indeed, it is these same two companies who are providing the “under the hood” systems and technology which are crucial for the deployment of Oceanus12 class with the AI and advanced sensor systems, enabling the vessels to navigate and make decisions in real-time. Beyond its autonomous capabilities, Oceanus12 is equipped with an array of sensors and scientific instruments aimed at collecting data on oceanographic and environmental variables.
Extensive R&D and innovation, aligned with robust engineering and planning will help to overcome the physical challenges associated with many of the perceived challenges with autonomy in marine surveying, including towing. Hull-mounted multi-beam echosounder (MBES) are part of the solution, but it’s AI that is emerging as the real gamechanger.
With AI, survey companies can automate and optimise speed, in addition to immediate-course and whole voyage routing for fuel optimisation and vessel safety. This yields cost-saving benefits for vessel owners, fleet managers, insurers, and cargo customers. In February 2024, Hydro International Magazine commented that “When used properly within an optimized workflow, from streaming the seafloor to producing the final geophysical product, AI will be responsible for massively improved operational efficiency.”
Given this, commercial performance and resultant job security will follow through quickly. In sum, AI promises immediate improvements to marine data acquisition and comes at a time when scarcity and cost of human skills and experience are increasingly significant industry factors.
That AI will increase job security at a time when skilled resource is low – partly down to the rapid growth off offshore wind discussed above – is a whole new story for another day, and one I’ll not go into here, but it is clear the appetite for AI and uncrewed surveying is growing. AI will not replace skilled surveyors, but it will help to streamline operations and the collation of accurate data and ultimately reduce human error and risk.
Furthermore, with AI, survey companies are ingesting data the entire time and whether it is object data from the CV (computer vision) system or the data from the radars and AIS, all of it can be used to train the AI data sets and curate these for improvements in the field.
As for the USVs, they need to deploy the sensors that are fit for purpose, such as Navtech’s high-definition W-band radar which significantly aids near range situational awareness and obstacle detection & avoidance for LOMO’s (Low observable marine objects) such as fishing pot markers.
By dint of their much lighter payload (no crew with all their attendant food, water and accommodation) USVs help reduce carbon emissions, so they are greener, as is their energy source, the sun, meaning that they can travel further, and longer, without shifts and other human dynamics.
Without a full understanding of the power and reliability of AI, it’s easy to see why some still fear the deployment of USVs in congested shipping lanes, and yet as The Mayflower proved, the reality is very different, and it’s only going to get better. USVs can also work in pairs or even fleets, looking out for out each other, or in tandem with crewed vessels if needs be. Whatever the future, get ready for more computers to take the helm of survey vessels exploring ever further corners of the ocean.
Potential ‘Box Out’ on technical spec
The Oceanus12 class is powered by an electric-hybrid power train with 100% redundancy – a very important consideration when working deep ocean, uncrewed.
The vessels have twin, commercially rated, 40Kw electric drives linked to twin 21Kw Lithium battery and powered by twin 22Kw marine diesel generators powering a 400V system. The generators have the ability to run off HVO (Hydrogenated Vegetable Oil) as well as regular marine diesel. At a cruising speed of seven knots the vessels have an operational range in excess of 2,000 nautical miles, actually more like 2,200. Whilst at lower survey speeds of three to four knots this range increase dramatically to in excess of 3,500Nm and all of this before an optional bladder tank for range extending is taken onboard.
Matching the electric drives, batteries, charging systems and generators to optimise the installation and ensure a “good match” has taken extensive collaboration with our powertrain partners and in many ways we are breaking ground again on the engineering side, as these system are not simply available off the shelf, but have to be custom specified and optimised. The result is a fuel efficient, reliable, and in full electric mode, extremely quiet power delivery.
Oil and gas operations are commonly found in remote locations far from company headquarters. Now, it's possible to monitor pump operations, collate and analyze seismic data, and track employees around the world from almost anywhere. Whether employees are in the office or in the field, the internet and related applications enable a greater multidirectional flow of information – and control – than ever before.