In the shale oil industry, effective water management is crucial. The extraction process generates large volumes of produced water, both naturally occurring and injected during hydraulic fracturing. Produced water, known in the industry as “saltwater,” often contains a high concentration of dissolved salts, chemicals, hydrocarbons, heavy metals, and naturally occurring radioactive materials (NORMs). To mitigate spills and contamination, it is essential to manage this water correctly.
Goodnight Midstream, established in 2011, has carved out a niche in saltwater management for shale oil operators. Their water pipelines support midstream water management tasks, allowing customers to bid farewell to challenges in this area. What began with just three saltwater disposal wells and a two-mile pipeline in the Bakken has now evolved into the management of over 450 miles of gathering pipelines linked to 50 saltwater disposal wells across the Williston Basin, Permian Basin, and Eagle Ford Shale.
Managing Water Pipeline — Managing Data
As the company’s pipeline infrastructure continues to grow, Goodnight Midstream intensifies its focus on meticulous pipeline management. Goodnight Midstream also now prioritizes advanced data analysis. Every inch of their pipeline infrastructure presents potential management challenges, including issues like pipe wall thickness, leaks, water flow rates, pressure fluctuations, inflow and outflow volumes, and the coordinated control of related equipment such as valves, pumps, and measurement instruments. Therefore, Goodnight Midstream needs to leverage data-driven insights to enhance system safety and efficiency.
The Journey of New System Development
Data collection and system processing are crucial for effectively tackling pipeline issues. Goodnight Midstream initially consulted INS, a key value-added reseller (VAR) with extensive expertise in the U.S. oil and gas industry and industrial networking, to implement Ignition® SCADA Software, which efficiently manages process control and data management.
Meanwhile, the company also had to factor in the hardware needed to run Ignition. To make sure the software worked on the computing platform, Goodnight Midstream furthermore had to get the Azure account and software environment ready. Since they didn’t have a specific support role to help with development and deployment, they concluded that extra resources and time would be necessary, making it difficult and time-consuming to create customized systems.
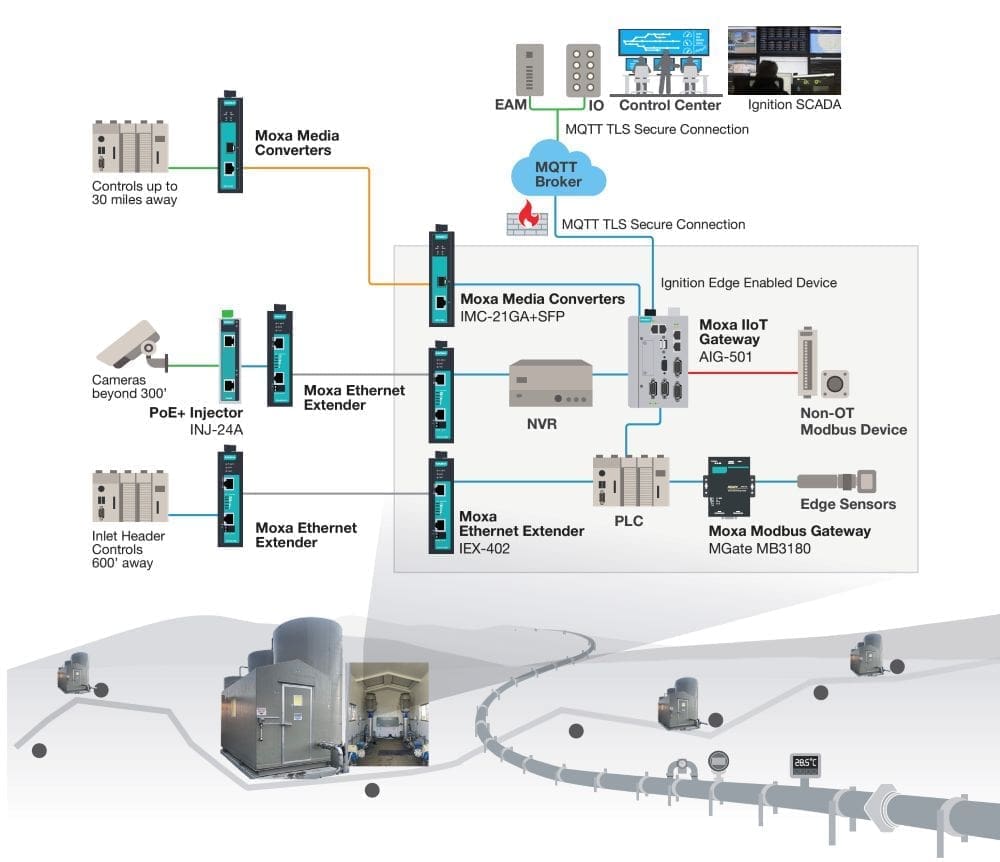
Communication System Hurdles
Another worry was operating in harsh and isolated oilfield settings. Goodnight Midstream sought networking solutions that could endure harsh conditions and guarantee secure process control and data management. Additionally, the complex on-site systems at Goodnight Midstream sometimes lacked communication experts in remote locations. Therefore, Goodnight Midstream required solutions that allowed for network visualization and remote monitoring, ensuring seamless data transmission from remote and distributed sites. Additionally, the communication devices needed to provide power to various network devices, including video cameras, over Ethernet cables.
“Several vendors have informed us that they offer excellent hardware platforms, but they require us to develop the necessary software ourselves. Given our time constraints, we needed a solution that is ready to deploy our SCADA software right out of the box,” said Rick Hornung, Goodnight Midstream Senior IT Manager.
Finding the Right Partner
Goodnight Midstream needed to install IIoT gateways at each of their 50 sites, spanning 450 miles, to transmit data from PLCs, cameras, and inlet headers to their control center for integration into the Ignition SCADA system. Making sure data transmission and integration are reliable posed a complex challenge.
In light of its established presence in the oil and gas industry, Moxa, a leading provider of industrial automation and connectivity solutions, joined forces with INS. For this project, Moxa and INS provided a suite of industrial-grade networking products from Ignition® SCADA Software to Moxa’s AIG-501 Series programmable IIoT gateways, Modbus gateways, PoE injectors, vDSL Ethernet Extender, and fiber optic SFPs.
Ready in 20 Minutes: Preload for Instant, Out-of-the-Box Setup
Few products on the market offer the operating system, preloaded libraries, cloud platform runtime, and container instructions all packaged and ready to go. To expedite the setup, Goodnight Midstream needed to find additional workers, which might take up to two days. The issue was exacerbated by the fact that they had to handle 50 sites but didn’t have enough personnel. It could take three to six months to find an adequate workforce.
Moxa’s AIG-501 programmable IIoT gateway, with ThingsPro software library and Linux OS, offered out-of-the-box compatibility with Azure runtime prebuilt and instruction for running Ignition SCADA software. With Moxa’s solution, the setup time was reduced to just 20 minutes and included dedicated support from IIoT engineers, both locally and at headquarters. “Initially, we faced challenges with Ignition deployment. Moxa was crucial in guiding us to a successful solution,” said Rick Hornung, Senior IT Manager at Goodnight Midstream.
Industrial-grade Communication Devices
At remote and unmanaged sites, heat and dust often cause problems for communication devices. Designed to withstand dust and extreme temperatures, Moxa’s AIG IIoT Gateways ensured network connectivity for reliable data transmission. Its removable storage design simplified issue reporting, even for non-technical personnel at any time. “We use removable storage in all field hardware to facilitate easy transport between devices,” stated Rick.
Additionally, Moxa’s INJ-24 PoE Injector powered video cameras and other devices by combining power and data over a single Ethernet cable. This setup was crucial for transmitting video feeds to the on-site control room, ensuring constant surveillance and monitoring.
“Leveraging Moxa equipment has been a key component in increasing information systems uptime, increasing data resolution, and creating cost effective solutions for common connectivity challenges. Reliable, high-resolution data is helping pave the way for our journey from automation to autonomy,” said Rick Hornung, Goodnight Midstream Senior IT Manager. “Moxa has helped us expedite the process, allowing us to set up a new unit in under 20 minutes—this has been a game-changer for us. It’s incredibly helpful when we need to deploy or replace a unit in the field.”
With a dedicated local team for the field site, INS provided expertise, customization, and support tailored to Goodnight Midstream’s specific needs. The team offered pre-sales consulting, integration, and post-sales assistance, assisting with tasks like setting up the SCADA system and installing IIoT gateways and PoE injectors.
The close collaboration between Moxa, INS, and Goodnight Midstream resulted in the development and implementation of a high-quality network to enhance process visibility and ensure dependable communication in water and pipeline management.
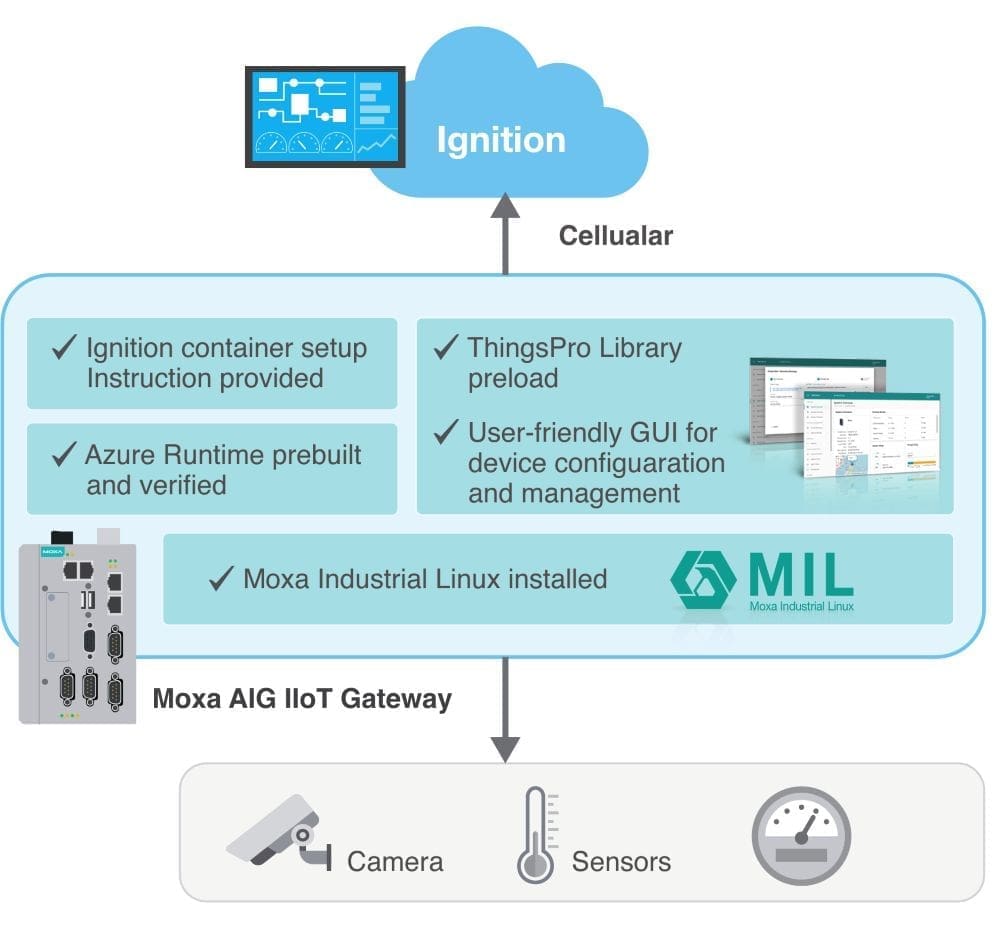
Triple Edge: Visibility, Reliability, and Power Efficiency
Goodnight Midstream now has a resilient network that can handle tough environmental conditions, thanks to this integrated solution. The combination of seamless connectivity and power management has greatly improved operational efficiency and data accuracy. The deployment of industrial networking solutions resulted in:
- Improved Process Visibility: Real-time data and process control enabled better decision making and operational oversight
- Enhanced Reliability: Rugged networking components ensured uninterrupted operation in harsh environments
- Efficient Power Management: PoE injectors simplified power distribution, reducing the need for additional cabling and infrastructure
A Sustainable Water Footprint
Many industries are embracing advanced water management practices, such as wastewater treatment, to decrease their fresh water consumption because of the importance of water as a crucial resource. There is also a growing emphasis on transparency. Over the last five years, there has been an 85% increase in corporate water disclosure, with more companies reporting usage and setting reduction targets, according to NGO CDP Worldwide.
Goodnight Midstream exemplifies this commitment to sustainability and operational excellence. By teaming up with INS and incorporating Moxa’s rugged networking hardware, the company successfully developed a resilient and efficient network for monitoring water pipelines. The customized solution tackles the obstacles in high-pressure settings, resulting in better performance and reliability. As a result, Goodnight Midstream effectively transported over 129 million barrels of used water annually, ensuring optimal use and treatment of water resources.
Headline image: Goodnight Midstream needs to collect various data to analyze and monitor the system for the remote oilfield sites and pipelines.
Oil and gas operations are commonly found in remote locations far from company headquarters. Now, it's possible to monitor pump operations, collate and analyze seismic data, and track employees around the world from almost anywhere. Whether employees are in the office or in the field, the internet and related applications enable a greater multidirectional flow of information – and control – than ever before.