In a world where steel pipelines run deep into the seabed and flammable gases move under crushing pressure, precision isn’t a luxury — it’s survival. Waterjet cutting, a technology once limited to soft materials, has carved out a niche in the most unforgiving environments of the oil and gas industry.
Waterjet cutting is a machining process that uses a high-pressure stream of water — sometimes combined with an abrasive — to cut through materials without heat or flames. In oil and gas, where the risk of ignition is constant and materials are tough and thick, this cold-cutting method is not just useful — it’s often the safest option.
Solutions like TECHNI Waterjet systems are engineered specifically for these high-risk environments, delivering precision and reliability where it matters most.
Whether you’re cutting down old subsea platforms or preparing flanges for high-integrity pipelines, waterjet cutting offers a rare balance of accuracy, safety, and versatility under pressure.
What makes waterjet cutting ideal for oil and gas operations?
The oil and gas industry operates under relentless pressure—literally and figuratively. Equipment must endure corrosion, extreme temperatures, and remote locations where mistakes aren’t just costly, but dangerous. Add to that the flammability of hydrocarbons, and it’s clear: traditional cutting methods can pose significant hazards.
Thermal methods like plasma or oxy-fuel cutting generate heat, sparks, and sometimes flames — a nightmare in explosive zones. Waterjet cutting, by contrast, is a cold cutting technique. It doesn’t produce any heat-affected zones (HAZ), making it safe for operations in volatile environments.
Safety aside, waterjet systems excel in cutting a wide variety of materials — even layered composites or rubber-lined pipes — without deformation. They’re also environmentally cleaner, producing no fumes, no slag, and minimal waste.
How does waterjet cutting work?
Waterjet cutting might seem deceptively simple — it’s just water, right? But under the hood, it’s a precise orchestration of fluid dynamics, abrasive physics, and machine control.
Here’s how the process typically unfolds:
- Pressurization of water
Ultra-high-pressure pumps force water to pressures as high as 90,000 PSI. - Addition of abrasive (if applicable)
For cutting metals and tough materials, garnet abrasive is introduced into the water stream. - Nozzle focusing and cutting
The stream is concentrated through a jewel orifice and directed through a cutting head. - Material erosion and separation
The high-speed stream erodes the material along the tool path, separating it cleanly. - Real-time monitoring systems
Sensors and controls maintain cut quality and adapt for material inconsistencies.
This process creates precise, burr-free cuts while maintaining the integrity of the surrounding material — a critical factor when dealing with high-stakes infrastructure.
What are the different types of waterjet cutting technologies?
Not all waterjets are created equal. The method you choose depends on the material and the application — and in oil and gas, that range is wide.
Pure waterjet cutting
This technique uses only pressurized water — no abrasive — to cut soft, non-metallic materials.
- Pros: Clean cuts, no abrasive cost, minimal maintenance
- Cons: Limited to soft materials like rubber, foam, or food-grade items
Abrasive waterjet cutting
By introducing abrasive particles like garnet into the stream, this method can cut nearly any hard material.
- Pros: Effective on metals, stone, composites, and clad materials
- Cons: More expensive, requires abrasive management, higher maintenance
What materials in oil and gas can be cut with waterjets?
From downhole tools to gasket seals, waterjet cutting supports a vast array of materials used in oil and gas operations. Its versatility lies in handling both hard metals and soft, heat-sensitive components without compromise.
Carbon Steel
- Properties: High strength, corrosion-prone
- Why waterjet?: Precise without inducing thermal stress
Stainless Steel
- Properties: Corrosion-resistant, dense
- Why waterjet?: Maintains edge integrity, no discoloration
Inconel and Nickel Alloys
- Properties: Extremely tough, heat-resistant
- Why waterjet?: Avoids microcracking and warping
Titanium
- Properties: Lightweight, corrosion-resistant
- Why waterjet?: Prevents work hardening and preserves mechanical properties
Composites and layered materials
- Properties: Multi-layered, variable density
- Why waterjet?: Cuts through layers without delamination
Coated or clad metals
- Properties: Mixed surfaces, differential hardness
- Why waterjet?: Uniform cutting across layers, no separation
Rubber-lined pipes and gaskets
- Properties: Flexible, elastic
- Why waterjet?: Clean cuts without tearing or distortion
Polyurethane and elastomers
- Properties: Soft, vibration-damping
- Why waterjet?: Prevents smearing, ideal for custom-fit components
What are the most common applications of waterjet cutting in oil and gas?
In oil and gas, where downtime is expensive and safety is paramount, the waterjet cutter is used in both planned fabrication and emergency response.
Here are common applications:
- Flange cutting
Creates precise bolt-hole patterns and gasket surfaces. - Pipe cutting and beveling
Cleanly cuts thick-walled pipes without heat or spark hazards. - Subsea decommissioning
Safely dismantles structures underwater using remotely operated tools. - Casing and tubing cutting
Enables accurate internal and external cuts without deformation. - Cutting explosive or sensitive materials
Avoids ignition risk when working near flammable or pressurized systems. - Maintenance and repair tasks in refineries
Supports on-site modification with minimal environmental disturbance.
What are the benefits of waterjet cutting in hazardous environments?
Cutting in hazardous zones—onshore or offshore—demands reliability without compromise. Waterjet systems meet this demand through a mix of safety features and operational precision.
- No heat-affected zones (HAZ)
Preserves material properties, critical in load-bearing structures. - Intrinsically safe (no sparks)
Ideal for ATEX-rated zones and explosive atmospheres. - Subsea and remote deployability
Can be integrated with ROVs for underwater work. - Minimal risk of ignition
Cold cutting eliminates the primary cause of industrial fires. - Accurate and repeatable cuts
Supports high-precision fabrication under extreme conditions. - Low environmental impact
No fumes, slag, or contaminated runoff.
What are the main components of a waterjet cutting system?
A fully integrated waterjet system consists of the following essential elements:
- High-pressure pump
Generates water pressure up to 90,000 PSI. - Abrasive feed system
Delivers garnet or other cutting media consistently. - Cutting head and nozzle
Focuses the stream for precision cutting. - CNC motion system
Moves the cutting head accurately along programmed paths. - Water catch tank
Captures runoff and dampens splashback. - Control interface
Allows operators to manage pressure, path, and diagnostics. - Filtration/recycling system
Filters spent water and abrasive for reuse or safe disposal.
What tolerances and thicknesses can waterjets handle in oil and gas applications?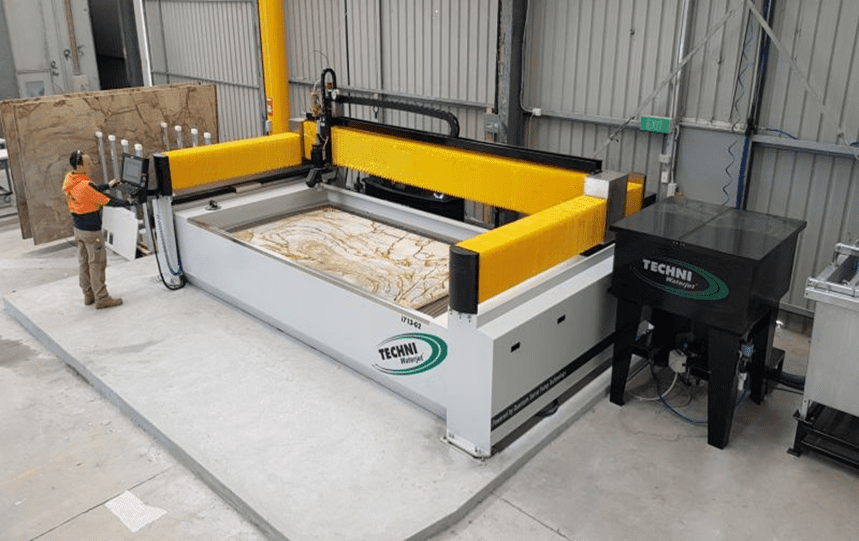
What are the typical tolerances for industrial waterjet cutting?
Waterjets are capable of:
- Dimensional tolerance: ±0.1 mm to ±0.5 mm
- Kerf width: ~0.76 mm to 1.2 mm
- Repeatability: ±0.05 mm, depending on system rigidity and software
How thick can waterjet cutters cut?
- Metals: Up to 300 mm (12 in)
- Softer materials: Up to 600 mm (24 in)
Abrasive jets handle harder, thicker materials. Pure waterjets are better suited to thin or soft materials.
How does waterjet cutting compare to other cutting methods in oil and gas?
Let’s break it down by cutting method:
- Plasma cutting
- High speed on thin metals
- Poor in precision, creates HAZ
- Oxy-fuel cutting
- Good for thick carbon steel
- Not safe in explosive environments
- Mechanical sawing
- Low cost
- Limited to simple geometries and access
- Laser cutting
- Precise, but can cause thermal distortion
- Ineffective on reflective or thick materials
- Wire EDM
- Extremely precise
- Requires electrically conductive materials
Waterjets stand out by balancing precision, safety, environmental performance, and material compatibility across the widest range of tasks.
What safety protocols are essential for waterjet cutting in oil and gas?
Safety isn’t optional in this industry. These protocols are standard for waterjet systems:
- PPE requirements
Operators must wear face shields, gloves, and high-visibility clothing. - Pressure release protocols
Ensure the system is depressurized before maintenance. - Zone clearance
Keep non-essential personnel away from the cutting area. - Monitoring and interlocks
Built-in failsafes halt cutting if anomalies are detected. - Remote operation for offshore/deep-sea cuts
Reduces human exposure to risk in hard-to-reach or volatile areas.
How is waterjet cutting used in offshore and subsea oilfield operations?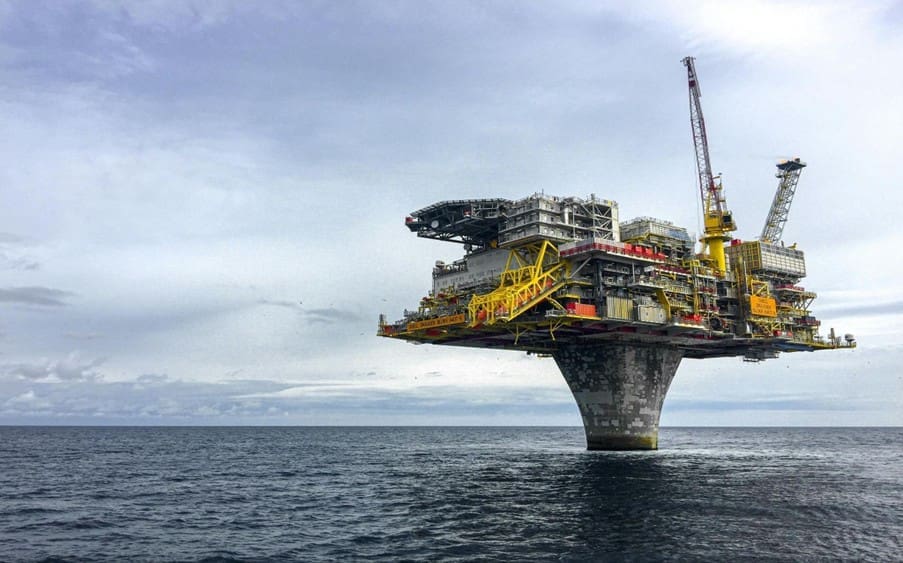
Waterjets can be deployed using Remotely Operated Vehicles (ROVs) in subsea environments. These missions often involve:
- Pipeline and platform decommissioning
Cutting risers, anchors, and conductors without diver intervention. - Emergency interventions
Fast response to compromised infrastructure. - Case studies
Operators like Shell and BP have used abrasive jets for subsea well abandonment, reducing risk and cost.
What are the design considerations for waterjet cutting in oil and gas?
When designing parts or assemblies meant for waterjet processing, keep in mind:
- Minimize unsupported sections to prevent movement
- Use standard tolerances to streamline CNC programming
- Hole diameter = material thickness for best cut quality
- Include tabs for holding small parts in place
- Choose erosion-resistant materials when repeated exposure is expected
What are common mistakes to avoid when using waterjets in oil and gas?
Avoiding these pitfalls will improve safety, precision, and efficiency:
- Incorrect abrasive ratio
- Cutting too fast on thick materials, leading to tapering
- Skipping filter maintenance causes nozzle clogs
- Not accounting for taper in high-thickness sections
- Improper clamping or hold-downs leads to misalignment
What should you look for in an industrial waterjet cutter for oil and gas?
Key selection factors include:
- Max pressure rating: 60,000–90,000 PSI
- Material compatibility: Support for steel, composites, rubber, etc.
- Automation level: CNC integration, remote control
- Abrasive handling system: Efficient feeding and recycling
- Durability: Corrosion-resistant housings for offshore use
- Remote operation capabilities: Especially for ROV integration
What’s next for waterjet technology in the oil and gas industry?
As demand for safer and smarter tools grows, expect waterjet systems to evolve through:
- AI-based cutting optimization
Real-time adjustment for material changes - Smart diagnostics
Predictive maintenance using IoT - Eco-friendly abrasive alternatives
Reducing waste and sourcing impact - Digital twin integration
Simulating complex cuts before executing on-site
Conclusion
In the unforgiving world of oil and gas, waterjet cutting stands out as a rare fusion of precision, adaptability, and safety. It thrives where other tools fail — underwater, underground, and under pressure.
But it’s not just about what it can cut. It’s about how it cuts — quietly, cleanly, and without compromise. As the industry pushes toward smarter, safer, and more sustainable operations, waterjet technology isn’t just keeping up — it’s leading the charge.
Oil and gas operations are commonly found in remote locations far from company headquarters. Now, it's possible to monitor pump operations, collate and analyze seismic data, and track employees around the world from almost anywhere. Whether employees are in the office or in the field, the internet and related applications enable a greater multidirectional flow of information – and control – than ever before.