Innovative technologies applied all along the oil and gas supply chain have dramatically changed the industry over the past decade, and companies have learned to turn to new techniques that make every well, every inch of pipeline, and even every employee as efficient as possible. Risks associated with lower oil prices, however, are forcing companies to work smarter to cut costs. Rapidly advancing information technologies have become a key source for efficiencies on the ground as the industry implements enterprise solution applications and new devices that are changing the very definition of smart.
A recent report by Intergraph Process, called “8 Technology Innovations Revolutionizing the Oil & Gas Industry,” provides a little insight into some of the technologies that are influencing productivity for companies.
Intergraph Process consulted with oil and gas industry representatives, including global Fortune 500 owners, operators and engineering companies, to gain feedback on the technologies that are making the biggest difference to productivity – from design and engineering to operations and maintenance.
According to Franz Kufner, executive vice president with Intergraph Process, oil and gas companies are seeking innovative ways to create efficiency as the industry moves from an exploration phase to a production phase.
“This report reveals that innovation in oil and gas comes down to two key factors: information management and communication,” Kufner added.
According to the report, there are enormous advantages to implementing advanced management systems as early on as possible – ideally before project planning.
“Given that today’s projects involve more contractors, fabricators and other suppliers than ever before, the efficient management of materials, such as pipes, valves, pumps, and tanks, is an issue that affects all stages of the project,” the report said.
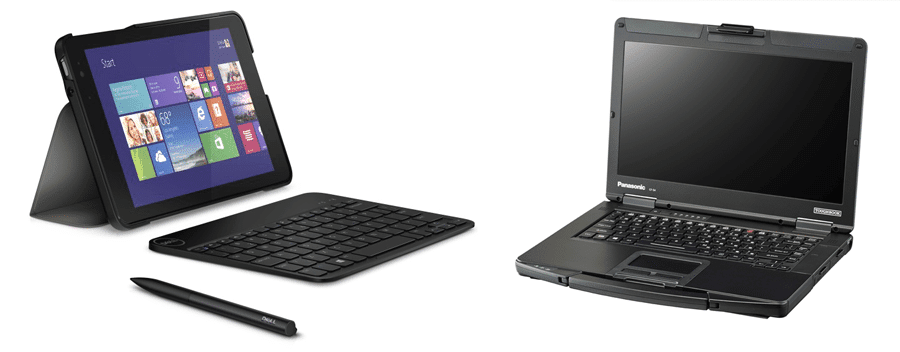
The report also noted that designers must select an engineering design system that can be used across different projects.
“Just like a race team, companies that want to optimize their people and processes to get the highest performance possible must focus their expertise on a single engineering design system,” the report said. “Not only is there the issue of higher costs for managing multiple systems, but also the fact that your best people are split across these systems.”
In addition, the report found that one of the industry’s most important trends is model data reuse in a collaborative environment. Model data reuse delivers significant benefits in complex contracting arrangements that involve multiple contractors and sub-contractors.
“Designers are able to share designs and models for reuse by other parties involved in the design process, creating efficiencies that shave work hours and ultimately, costs,” the report said.
Modular design is another important trend for the oil and gas industry, according to the report.
“With project budgets getting tighter and tighter, it makes sense that companies are sourcing parts and materials from all over the world – not just in the local area of the project,” the report said. “This means that systems need to be designed to be ‘taken apart’ – with due consideration for the fact that individual components will be sourced and shipped separately.”
Progress also is being made in interface management, according to the report.
“A typical CAPEX project will have 20 to 100 separate interfaces that need to be managed, each with hundreds of issues that need to be resolved,” the report said. “Traditionally, these interfaces have been managed by way of Microsoft Excel sheets or ad hoc databases, making consolidated reporting and gaining a comprehensive management overview nearly impossible.”
Project execution solutions that are tailored for oil and gas owner operators now can provide template processes that allow for the hierarchical structuring of interface needs and management reporting.
The report recommended that oil and gas companies work closely with technology providers to customize a data handover solution that makes sense to a given project.
“The handover of data and documentation occurs many times during the project life cycle, with project participants having to deal with a continuous flow of information from suppliers and contractors,” the report said. “This means often tens of thousands of documents, and hundreds of thousands of records, which must be validated and organized before handover.”
The report said that, ultimately, cloud technology is the absolute cutting edge means for oil and gas companies to work in a consistent environment and save on operating costs.
“A central repository of data is established across multiple locations, companies and business units within those companies,” the report said. “The financial benefits of working in the Cloud are significant – Cloud technologies eliminate the need to implement new hardware, networks and staff, which means capital expenditure can be reserved for investment in resource-producing assets.”
Information management in near real time
Information management and better communication between field personnel and managers has been the focus of the founders of Fort Collins-based CartoPac for more than a decade.
CartoPac provides enterprise solutions that enable highly accurate collection of asset inventory and inspection data. The company has been working with major oil and gas companies to support geospatial field asset management needs and leverage GIS expertise to help companies meet their regulatory compliance and realize time saving and cost saving efficiencies.
Companies in the oil and gas industry use CartoPac solutions for pipeline asset management, one-call reporting, regulatory compliance, inspections, tracking cathodic protection systems, permitting, safety issues, asset inventory, and data visualization and reporting. The company’s solutions include high-accuracy mobile solutions, high-quality data visualization and reporting, and a preconfigured, ready-to-deploy platform, called Jumpstart.
According to Scott Crouch, vice president of CartoPac, the customizable solutions CartoPac uses today took shape when the company first started working with Chevron Pipe Line Company in the mid-2000s.
CartoPac now works extensively with oil pipeline owners and distribution providers, and it has branched out to gas distribution and electric utilities.
“Our client base is about 60% oil and gas and 40% other applications, such as UN weapons inspections teams and even dolphin mapping,” Crouch said.
Earlier this year, the company rolled out its third generation solution at Chevron Pipe Line for Chevron’s asset management system.
“Our first generation solution was not as centralized as the later solutions,” Crouch said. “Our second generation solution was centralized through a server, and the latest version is centralized through [Esri’s] ArcGIS server.”
Crouch said that the latest generation solution is a much more robust server system, and it’s tied directly into Chevron’s enterprise system.
The latest solution features a decision process tree on the back end that allows data to be allocated to the appropriate personnel.
“It’s a near real-time solution,” Crouch said. “When the field personnel check in their data, it will be known in the central system, and from there, managers are able to run reports and the analytics on that data to have a good picture of what is going on in their infrastructure.”
CartoPac’s solution has a mobile component and a server component. Each of those components have a desktop technology that allows the company to customize the workflows on the back end and define who the users are and which users have permissions to see certain data.
On the mobile side, CartoPac has a customization tool, called Studio, which allows the company to customize workflows in a very detailed sense and match them up with a client’s enterprise database.
A client will provide CartoPac with paper forms that they use for a repair pipeline inspection, and CartoPac customizes a solution to capture all that data in the paper form. In addition, CartoPac will add on more logic so field personnel can collect even more data than they did on the paper form,
Crouch said.
Device management
Field personnel access and populate digital forms via handheld devices in the field.
“We support a broad array of devices to the right accuracy,” Crouch said. “If our client wants four-inch accuracy, or under two-meter accuracy, for example, we’ll set that up for them; then we match the right device for the right jobs.”
For very high accuracy, field personnel may use a Trimble handheld device, which is a Windows CE device, or a Leica handheld device.
“Those two devices could be accurate down to a centimeter, but in the oil and gas industry the standard is four-inch accuracy,” Crouch said.
If a customer wants more screen real estate than the traditionally smaller screens on the Trimble and Leica, CartoPac can couple a Trimble-like antenna with touchscreen tablets that have a larger eight-inch or 11-inch screen.
Crouch said that a lot of CartoPac’s customers really like the larger screen for inspections that do not require high level accuracy for locating assets.
He added that one of CartoPac’s clients is using a Panasonic Toughbook, which is a really ruggedized laptop, for field inspections.
“The trend right now is to move to a little bit bigger devices,” Crouch said. “In the oil and gas industry, it’s saving them a lot of money because they have one device for their field personnel, who can use the device in the field, bring them back to the office and dock the device to use as a laptop.”
Crouch said that a couple of CartoPac’s customers have recently adopted Dell Venues, which field personnel can pair with a keyboard in order to use them as laptops.
“In the past, companies had to buy a laptop and a high accuracy device, and now you can even mix and match components,” Crouch said.
Users also can integrate many different peripherals with the CartoPac solution, such as still cameras, video cameras, laser range finders, radio-frequency identification readers, and barcode readers.
Time savings
Crouch said that CartoPac’s solutions reduce the amount of time field personnel spend filling out forms and the time traditionally spent entering data that personnel brought back from the field.
“When the field personnel fill out the electronic forms, the system can enforce the data present in the form,” Crouch said. “For example, they only have items in a drop down menu that make sense, and they don’t have to type fresh content.”
The form also can control the amount of data that field personnel input under different scenarios.
“At a crossing, for example, there could be about 17 questions to answer that the Department of Transportation has to audit,” Crouch said. “The system ensures that the necessary data is entered and returned to managers.”
Crouch said that one of CartoPac’s clients reported that it saved $850,000 in one year with 50 system users. Another company reported that it had 50% to 75% less time entering data.
The time to integration for a CartoPac solution can be anywhere from three months to a year, according to Crouch. The turnaround depends heavily on a client’s internal needs and processes.
“We can do an enterprise system in a couple of months if everything is working together and we have support from the highest levels,” Crouch said.
Oil and gas operations are commonly found in remote locations far from company headquarters. Now, it's possible to monitor pump operations, collate and analyze seismic data, and track employees around the world from almost anywhere. Whether employees are in the office or in the field, the internet and related applications enable a greater multidirectional flow of information – and control – than ever before.