With the evolution in recent years, the energy demand for fossil fuels has been increasing (with some periods of recession and/or stagnation), which has led to a search for resources in places of high operational complexity, such as seas and oceans. This activity is called offshore extraction, the word offshore means “in the sea, away from the coast,” to indicate the location of a resource or a production process.
The activity, per se, is extensive and includes the exploration, development, and exploitation of oil and gas accumulations. It is critical to conduct geophysical studies, such as seismic studies, in large areas to identify possible exploration blocks. Once the areas with the best conditions have been identified from an exploration standpoint, the oil wells are drilled from ships or temporary platforms to verify the existence of possible hydrocarbon-containing traps. Once the traps have been spotted, the drilling of development oil wells from fixed-production platforms takes place as well as the construction of the transportation and processing infrastructure. The production units can be of various types: platforms with multiple production and reinjection wells, storage tanks, separators, and support equipment.
Transportation is usually carried out through flow lines and, occasionally, by barge or tanker to onshore refineries and/or gas processing facilities.
Hazards and Accidents
Among the most common risks and accidents that originate in offshore operations are the following:
- Platforms for offshore operations are generally confined spaces; therefore limiting workers’ activities. The fact of carrying out simultaneous activities requires greater safety controls. There is a high risk of accidents due to falls, slips, and trips, considering the large number of irregular steps and floors.
- Greater risk due to storage of chemical, radioactive, and explosive products.
- Platform safety equipment (BOP, riser, and surface equipment) uses high pressures.
- Greater difficulty in mitigating environmental spills.
- Risk of accidents during transport by helicopters.
- Greater difficulty in certifying fixed equipment on the platform.
- Need to incorporate equipment for areas with risk classification of 0, 1 or 2 on the platform.
Most workers are aware of the hazards faced in this type of work. They know that they can be from gas leaks, explosions, fires, or poor environmental conditions, but what is weighed more strongly and critically is the possibility of a hydrogen sulfide gas leak and, consequently, an explosion and fire. There are multiple perception errors that are mainly associated with communication or the way information is handled. These can be multiple and can indicate diverse and varied causes.
Safety in Offshore Operations
Safety, as it is known nowadays, is an integral part of every operation, project or program. It cannot be ignored as it is intertwined with the economic aspect of a company. It is a crucial factor in reducing costs and, if it is not controlled, costs can increase out of proportion. Not following these rules could harm the company, as in cases where the injured party sued the company and the ruling was favorable.

The effectiveness of prevention depends significantly on the adequate and precise identification of the risks present in the development of work activities. In the same way, it is vital to carry out an adequate analysis of causes and their evaluation; since according to these results, solutions are proposed either for the mitigation or elimination of risks. For this, two techniques for the identification of risks will be explained.
Job Safety Analysis (JSA): A technique that is based on identifying, in the same workplace and with the workers themselves, the hazards to which they are exposed when carrying out their daily work. Its objective is to reduce or eliminate the risk of accidents. To fulfill its objective, it is necessary to carry out an analysis of the tasks through an appropriate methodology (JSA) that will make the tasks safer, not only for the benefit of the staff, but also for the company in general. A step-by-step methodology is explained in the following figure.
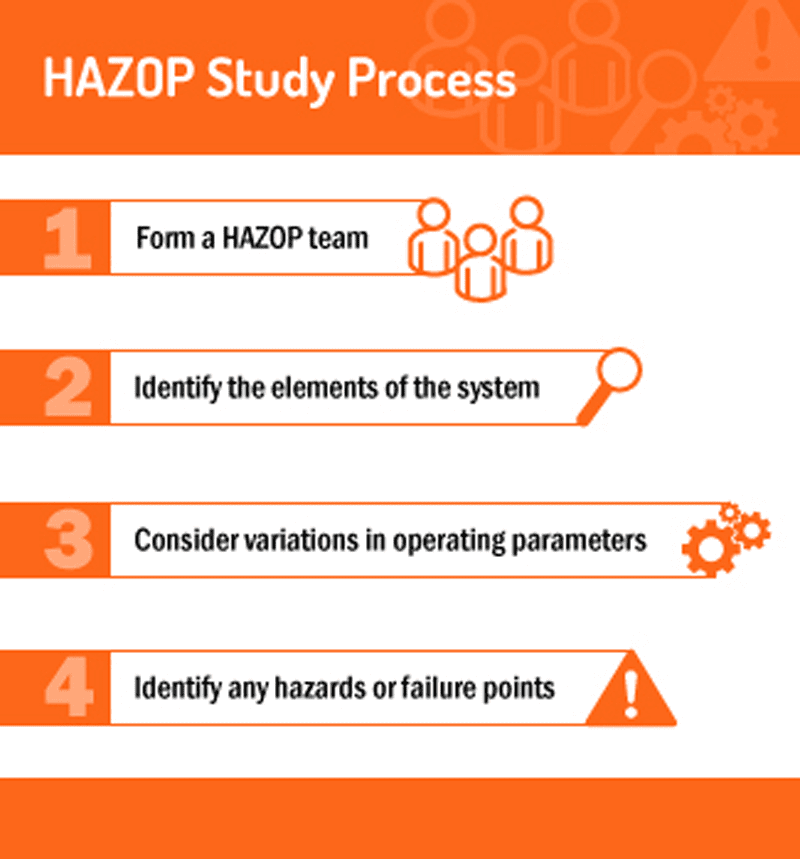
HAZOP: A Process Risk Analysis (PRA) technique based on the premise that risks, accidents or operability problems occur as a consequence of a deviation of the process variables with respect to normal operating parameters.
The HAZOP risk analysis is suitable for both a design stage and an operation stage, evaluating in both cases the consequences of possible deviations in all process units, whether they are continuous or discontinuous. The technique consists of systematically analyzing the causes and consequences of deviations of the process variables, presented through “guide words.” This methodology is better explained in the following step-by-step figure.
Environmental Problems and Solutions in Offshore Operations
Offshore oil and gas industry operations involve environmental risks, especially oil spills from oil tankers or pipelines that transport oil from the platform to shore facilities, as well as the hazards of leaks and accidents on the platform. These problems can be divided by area:
Water: Hydrocarbon producing activities cause contamination of the waters around the platforms. In coastal areas, raised sediments may contain heavy metals and other contaminants. Drilling muds and discharged additives are contaminated with formation waters and introduce hydrocarbons, heavy metals, and other contaminants to the water column. Non-routine events such as spills during transfer or at loading areas, pipeline failures, tanker spills or well blowouts can cause severe contamination of the local or spread water column.
Air: Emissions in the drilling and production area include combustion gases from generators and pumps, evaporation of oil at transfer and load areas, burning of waste gas in the burner, and small oil spills.
Land: Seafloor disturbances can be caused by extraction of samples from the bottom, dragging of anchors, location of the drilling vessel or platform, installation of production equipment, and excavation of the pipeline during development. Contamination of the bottom occurs as a result of discharges from drilling mud and solid waste. Upheavals on land will be the result of trash and spilled oil that floats ashore. It is of utmost importance to carry out environmental impact studies where the corresponding evaluations for the handling of these products are carried out, as well as the monitoring and follow-up of transport, use, and possible risks that they may present to the environment in the event of any type of accident, to prevent environmental impacts, clean up and restore environmental liabilities, to reduce deviations in occupational health and industrial safety.
This series of problems presented above has its possible solution depending on the problem that arises. Among them there are:
- For the problems that arise when releasing mud and wastewater from the platforms to water bodies, the solution is simple. These liquids should simply be contained in the best possible way and taken to places where they can be treated without any problem.
- For possible spills, either from platforms or from hydrocarbon transport means, the solutions are more complex and, therefore, not always effective. There are several methods to contain and clean hydrocarbon waste, for example. Some solutions are given below:
- Use of contention barriers for further processing.
- Use of dispersing agents.
- Burning of spilled product (in situ).
- Skimmers: mechanical devices that physically remove free or contained oil
on the water surface. - Use of absorbents when there are small amounts of oil.
- Oil transfer through the use of pumps.
It is imperative to continue studying new technologies that can prevent any accidents that may occur during these operations. Also, better emergency plans need to be designed to have a quicker and more effective response to any possible accident, as small as it may be. The present and future goal of any company should be zero work accidents and no environmental damage.
The most tragic case of offshore operations accidents and environmental problems to have occurred is the Deepwater Horizon, which was a platform located in the Gulf of Mexico, and had a terrible accident on April, 20, 2010. To understand the subject better, let’s take Lisa Friedman’s article featured in The New York Times titled “Ten Years After Deepwater Horizon, U.S. Is Still Vulnerable to Catastrophic Spills,” where she explains that this was the largest accident in the history of the United States, resulting in loss of human lives and a severe, negative environmental impact in the area surrounding the accident’s location, where more than three million barrels of oil were released into the waters off the coast of Louisiana. Due to this, safety improvements have been made to prevent this type of catastrophic accident from reoccurring.

Headline photo courtesy of Bloomberg – Offshore operation facilities.
Juan Zambrano has around 3 years of experience in the oil industry, working in the following areas; reservoir engineering, support engineer for a petrophysical environmental corrections in a petrophysics program and geomechanic engineering. Working in several projects, such as, developing a 1D geomechanical model, a Phase 1 reservoir model and serving as a consultant in a petrophysical app development. Holding a Bachelor’s Degree in Petroleum Engineering and currently coursing a Masters in Petroleum Engineering.
Oil and gas operations are commonly found in remote locations far from company headquarters. Now, it's possible to monitor pump operations, collate and analyze seismic data, and track employees around the world from almost anywhere. Whether employees are in the office or in the field, the internet and related applications enable a greater multidirectional flow of information – and control – than ever before.