Refineries are petrochemical industrial plants where substances derived from crude oil and gas are obtained. Within their walls, transformation and refining processes occur to obtain products such as gasoline, diesel, asphalt, kerosene, liquefied gas, oils and fuel. To talk about refineries is to discuss movement worldwide.
Today, refined hydrocarbons are the most vital source of movement in the world, despite their competitor: electric cars. In 2018, the number of electric cars per 1,000 people in China was 1.6 and in the United States that number was 3.4 people per 1,000 people. This means that the world will depend on refining processes for much longer.
If we count the things produced in a refinery, we notice that all derivatives have a significant degree of volatility. Add to this the acidic and toxic elements used to carry out these purification and refining processes and we conclude that it is work that involves constant high risk because the slightest mistake can lead to tragedy.
Beyond a solution including the use of protective equipment such as appropriate clothing, special nitrile gloves or insulator, artificial respiration masks or suits to prevent environmental toxicity in controlled sectors, the best safety practices for the refining industry are based on the implementation of these resources as a small part of the entire system. The best way to avoid accidents is if they do not occur. Regulations are based on this principle, especially the ones created for work in refineries.
Although most hydrocarbon refining industries worldwide adjust their safety and regulation mechanisms, there is a global standard rule provided by the American Petroleum Institute (API), composed of 180 operational refining safety standards, which are approved by the American National Standards Institute (ANSI). It should be noted that API standards are required in most countries for refineries to operate safely.
API Standards Base for Safety Regulations
The 180 regulations of the API created for the industrial refining complex are based on avoiding accidents, considering solutions in the form of regulations, with the use of the pyramid created in 1931 by H. W. Heinrich. This pyramid is represented with two key concepts in the field of safety as established by the API document titled “Process Safety Indicators for the Refining and Petrochemical Industries.”
- Safety accidents can be placed on a scale representing the level of consequence.
- Many precursor incidents occurred with lesser consequences for each accident that occurred with greater consequences.
- Pyramid tier 1 events refer to safety events that are represented as the most consequential incidents as the result of real containment losses. This type of accident is closely related to the loss of toxic or volatile fluids in the facilities.
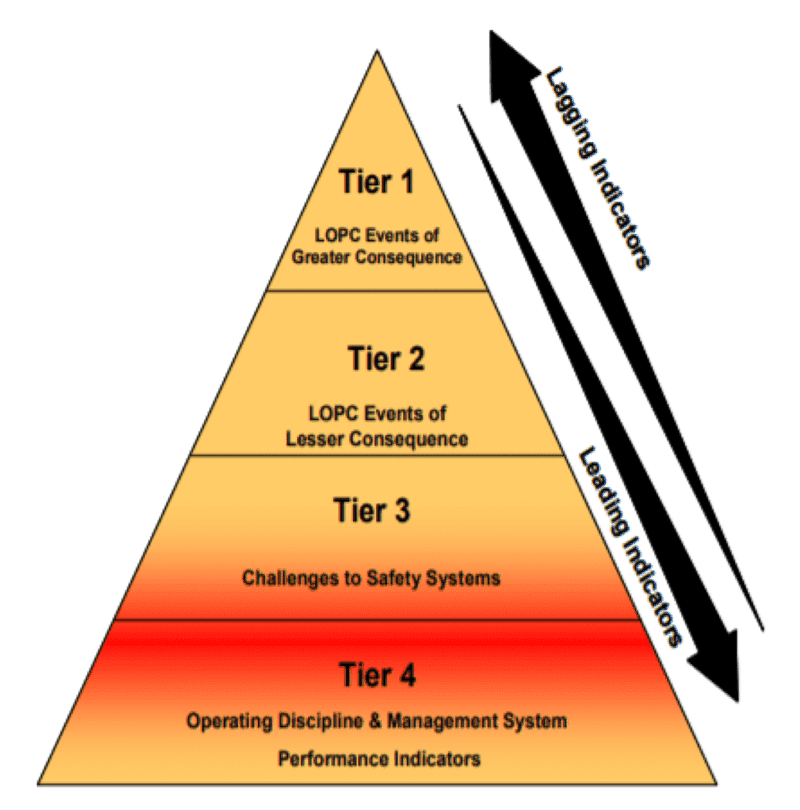
At this tier of the pyramid, the regulations established by the API that integrate the proper management of the processes within the facilities enter the scene to avoid possible spills of hazardous substances, either volatile or toxic.
In the Recommended Practices (RP) 2001, provided by the API in 2019, it is mentioned that the best ally to deal with process failure and to avoid Tier 1 of the Heinrich pyramid, is the correct digitalization of the industry. This limits the intrusion of human error and does not put lives in jeopardy, using PLC valves, and sensors for detection of leakage and odors, under the management of the supervisory control and data acquisition system (SCADA), added to the standard emergency spraying systems for refineries.
- Tier 2 of the pyramid sets out spill events with respect to inert fluids that may cause problems of minor consequences, but these in turn may cause major operational problems in the facilities.
What is established by the pyramid encourages the rules of best practices to have as the main alert for the second tier of the pyramid, where a failure not visualized on time generates an unexpected spill which, despite containing a non-toxic or dangerous substance for human personnel, marks an Amber Alert in the mechanisms of action, and encourages the inspection and reconditioning of all processes before and after this.
The API in its RP 2001 (8th edition) mentions this point in particular and establishes a series of action rules in view of these situations, including the use and implementation of the SCADA system for the management of diluent pumping toward the distillation and enrichment processes of hydrocarbons, as well as the presence of highly qualified and experienced personnel to avoid unnecessary alarms in case of spills.
- Tier 3 of the Heinrich pyramid addresses problems related to weaknesses in safety systems, ranging from the entry of unauthorized personnel into a certain area, to a failure in the inspection of the raw material entering the refinery, as well as the inspection of automated processes.
For the correct prevention under this tier, the use of experienced personnel is established as well as automated processes to perform multiple random and periodic inspections in the established safety systems. In this way, the automated system is constantly inspected and the personnel is kept alert to be prepared for any unexpected event.
- The lowest tier of the pyramid deals with operational discipline and performance in process management systems. This is addressed to those responsible for compliance with the methodologies expressed in the operating manuals, i.e., human personnel, their degree of discipline, experience and commitment to comply with what is programmed.
The lack of personnel training is one of the main reasons for operational problems in refineries. In the RP 2001 document (9th edition), it makes special mention of the training of those involved in the development of processes, as well as the correct employment in the activities corresponding to qualified personnel.
The 187 parameters intended by API and the American National Standards Institute
(ANSI) for a safe environment in refineries, in addition to being a requirement for operation, are an alternative that, if followed to the T, give the system an almost foolproof functionality, as explained in the document “Comments of the American Petroleum Institute,” prepared by the API for the State of Washington in 2018, in which an assessment of refineries on U.S. territory was conducted.
It should be noted that the U.S. government requires the operation of refineries under API regulations. The results show that the 187 standards established under the RP 2001 document, in all its editions, fulfill the goal of establishing a safe environment by far.
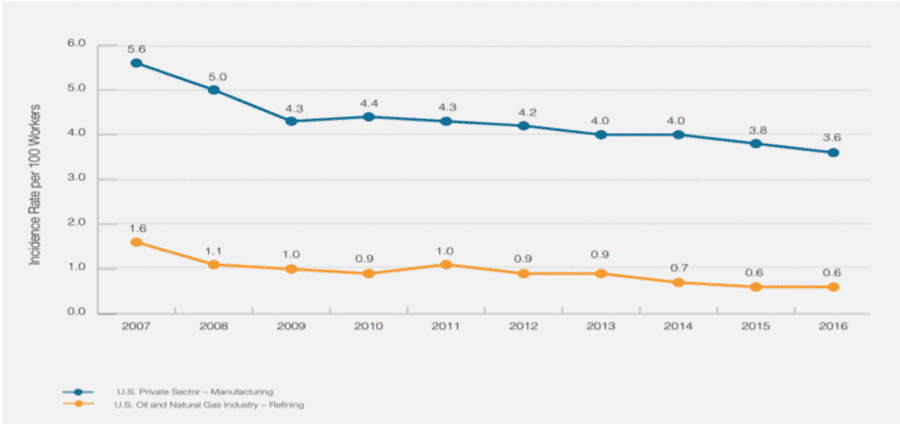
In this exercise, 520 companies from both the public and private sector were compared with refineries operating under the standards established by the API. The result is that the number of accidents per year is 0.6, regarding important cases.
On the other hand, the API conducted a survey in recent years, collecting safety data during the processes. Process safety involves the application of good practices of operation, maintenance, inspection, engineering and processes, i.e., compliance with the Heinrich pyramid. These are the results:
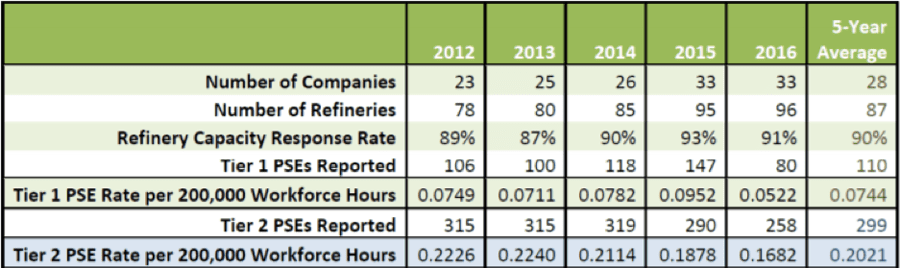
The study was conducted from 2012 to 2016 and included approximately 85 refineries per year. The analysis was based on the problems related to tier 1 and 2 of the Heinrich pyramid divided into 200k hours of work per man. The results showed that the practices established by the API for the management of operations in refineries kept the cases of danger or accident to a non-existent amount.
In light of these results, there is no doubt that the best practice for an environment free of accidents is prevention based on the prediction of possible accidents, from minimal circumstances that can lead to major problems. The 180 regulations prepared by the API as regulations for the proper functionality of the refineries are guaranteed as the best way to avoid accidents (this type of document obeys a copyright and may not be used unless the proper training is obtained). Thanks to this document, it is now a federal requirement that a refinery must have a permit to operate. It also requires training of personnel by the Occupational Safety and Health Administration (OSHA).
The use of helmets, safety suits and gas masks are the first line of defense for workers in refineries but, if the degree of danger with which workers do their job every day is analyzed, it can be concluded that without a proper and hermetic safety system the zero accidents goal cannot be achieved. Automation and process management followed to the T are here to stay, and every day they save more lives and jobs.
Andres Ocando is a 30-year old petroleum engineer, who has been working for PDVSA for five years, facing positions such as reservoir engineer and geomechanical engineer. He currently works as a project analysis engineer. There, he has optimized the data collection process for the development of geomechanical models. Ocando has experience in copywriting and is currently a technical writer on topics related to the oil and technology industries. He collaborates for important technical publications such as OILMAN Magazine and SPE. Quality and responsibility are two words that describe him perfectly. Ocando is currently pursuing higher studies at the University of Zulia to obtain his master’s degree in petroleum engineering.
Oil and gas operations are commonly found in remote locations far from company headquarters. Now, it's possible to monitor pump operations, collate and analyze seismic data, and track employees around the world from almost anywhere. Whether employees are in the office or in the field, the internet and related applications enable a greater multidirectional flow of information – and control – than ever before.