Driven by the worldwide COVID pandemic, the oil and gas industry is challenged to plan and operate with new procedures and approaches to keep its employees healthy. Social distancing, sick employees, and quarantine requirements can lead to smaller crew sizes, staggered shifts, and limited expert availability. Companies are often under pressure to operate safely with fewer and less experienced employees.
This pressure is compounded by the retirement of large percentages of experienced workers in many industries. Industrial organizations have indicated that up to 25-30 percent of their workforces are retiring over the next three to five years. In an industry like oil and gas, where the workforce is regularly being replaced as workers age out, there are real questions as to how to make existing employees more productive and efficient, how to on-board new employees quickly, and how to enable less experienced employees to leverage expert knowledge in order to be proficient and operate safely – and how to do all this when travel and in-person collaboration may be hampered.
This is where augmented reality (AR) can help. An industrial AR solution can capture skills and expertise, apply them to training and work instruction content, and ultimately drive knowledge transfer across an enterprise to increase collaboration and productivity while decreasing errors. It can be a fundamental tool to help drive business continuity, flexibility and resilience.
An AR solution can help upstream frontline workers repair an oil well, or midstream workers monitor and manage segments of a remote pipeline, or a downstream refinery technician react to real-time sensor data from a supervisory control and data acquisition (SCADA) system to implement corrective actions faster. Step-by-step, guided work instructions can be created with AR to make it easy for frontline workers to complete the task at hand by simply donning a headset with step-by-step instructions and real-time data appearing within their field of vision. Instructions are enhanced with photos, videos, 3D diagrams, sensor data as well as sequential instructions requiring evidence of successful completion before prompting workers to move to the next step. It combines to create an interactive, multimedia experience that is far superior to past approaches with paper or rudimentary digitization.
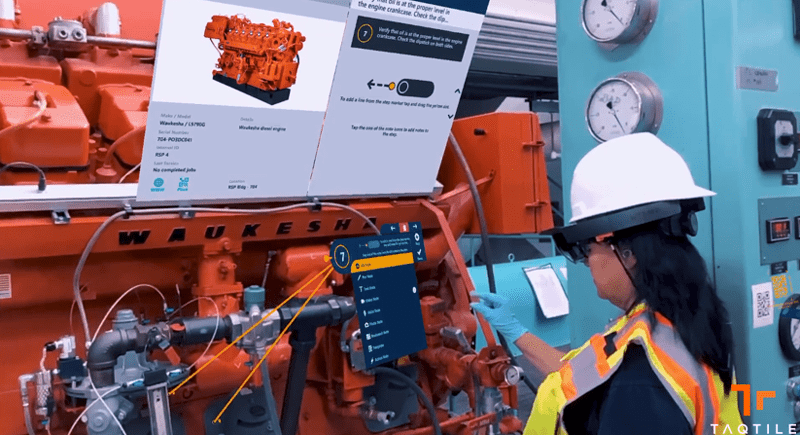
Onboarding and Training
New employees rely on more experienced employees to show them how a job gets done. Before AR, both parties needed to be onsite for training, especially when the task at hand involves machinery or tools new to the trainee. Now, with AR solutions, the trainee and trainer don’t need to be on site together for instruction to take place; in some case, trainers may not be required at all. Evidence of successful task completion can be captured via photos or videos so that auditing and evaluating can be automated or performed remotely.
Experts can create digital tutorials based on their knowledge and overlay the tutorial on real-world equipment. No matter how much equipment or how many procedures a technician on an oil rig needs to learn or how many tutorials an engineer needs to map out, it can be done easily and quickly with an industrial AR solution. Such solutions deliver digital transformation and productivity to frontline workers in a simple, consistent and scalable way.
Workflow Instructional Content
Without additional consulting or programming, experts create step-by-step digital instructions overlaying the rig’s equipment, which other workers see via an AR device such as a heads-up display (HoloLens and Magic Leap are two popular examples) or an AR-enabled tablet like an iPad. Instructions appear as a checklist where steps are spatially anchored to the equipment and workers mark off each step when completed.
Any supporting materials a worker may need in addition to the basic step-by-step instructions and checklist, such as supplemental photographs, videos, PDFs or documents, further aid the worker in knowing exactly how to operate, maintain or repair equipment. An operator can walk up to the same equipment type at any location, put on a headset, and follow the step-by-step instructions to get the job done. Independent studies comparing AR content with traditional approaches have demonstrated 36 to100 percent decrease in errors when using AR. The technology helps less experienced workers make fewer mistakes and become proficient much faster, and experienced workers will be more consistent when completing complex or less frequently executed tasks.
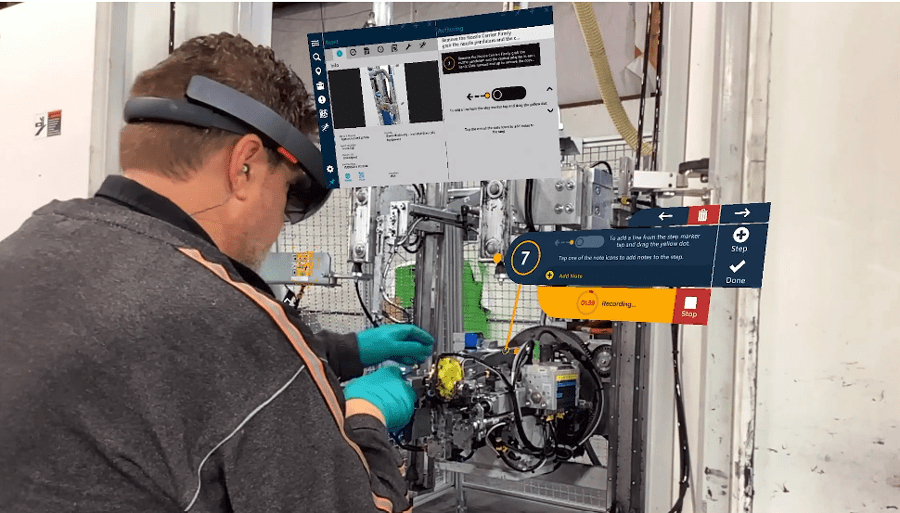
Safely Operating
Specific safety training is a vital component when it comes to keeping equipment properly maintained, using machinery appropriately, and keeping frontline workers and their colleagues safe. Upon completing a high incident safety issue analysis, a steel plant found 85 percent of incidents occurred with workers who had been on the job for 30 days or less. This emphasizes the value of efficient training solutions like those built around AR to guide new employees through tasks and safety protocols from the get-go to reduce the margin of error and number of incidents.
AR content is a great medium to document the practices and procedures for a lockout/tagout process. A step-by-step checklist can be accessed hands-free from a headset while a worker is performing the procedure. Evidence for each step completion can be required and captured before a worker is prompted to move to the next step. This can even benefit experienced technicians who may get distracted by other activities within their environment.
An AR solution can also help frontline workers operate complex machinery more safely by incorporating real-time data from SCADA systems into their heads-up displays. Real-time warnings or updated readings can be viewed with a headset when a worker is at the machine. There is no need to radio the control room and a worker’s hands are free to manipulate the equipment or take corrective action. This can result in a faster or more accurate and safer response or action. It can also help workers operate more safely when completing tasks in harsh or remote environments such an oil rig in the North Sea or a pipeline in Alberta.
Expert Assistance
Leveraging experts in real-time is another area where AR solutions really shine, especially when work is being performed in remote locations as described above. Frontline workers with questions about any task (whether it be a new or unfamiliar process) can initiate a real-time chat with an expert from their heads-up display. Communication can be initiated directly from the step they need help with, providing valuable context to the remote expert. Real-time video can also be shared so that experts can see what their colleagues are seeing to enable speedy and accurate assessments. This is faster and safer than a phone call or video chat on a mobile device because the worker retains the use of his or her hands while attention and focus are maintained on the task and not the mobile device.
There are also ways to facilitate finding and contacting the correct expert. This is especially important in large, decentralized organizations. Internal contact lists enable the user to connect with the foremost expert available through relevancy sorting, starting with the original author of the job and other recent operators. This means the worker and the expert do not need to be working in the same room, the same shift, on the same day, or even know each other, allowing for broader assistance and collaboration regardless of location. It is not surprising that remote expert assistance is a driving force in AR adoption during this pandemic where travel is limited and scaled down crews are being utilized.
Working Together, Remotely
In addition to the ad-hoc expert assisted experiences described above, using an AR solution can help teams plan and collaborate on coordinated workflows and tasks regardless where team members are located.
Tutorials or instructions assembled via knowledge capture and job templates allow employees to execute planned team procedures while bringing in as many people as necessary. Collaboration through tools like a digital team review means a seamless transition between steps of the job and between individuals on the team regardless of shift overlap. An employee simply puts on the AR headset, divides the work among team members through either assignments or self-assigning steps, and completes the tasks assigned to them, keeping the job on schedule. The whole team can watch the job progress through each step, leave notes for other operators, and invite others, even from other locations, to take over, if necessary.
Combined with the live expert assistance mentioned above, using AR collaboration is a valuable solution to facilitate inspections with remote support. One operator could work with one or more remote inspectors in the field to help them evaluate, check and authorize equipment readiness. This can decrease multiple site visits by different people, reduce travel, and make common equipment checks, rounds and routine inspections much more efficient.
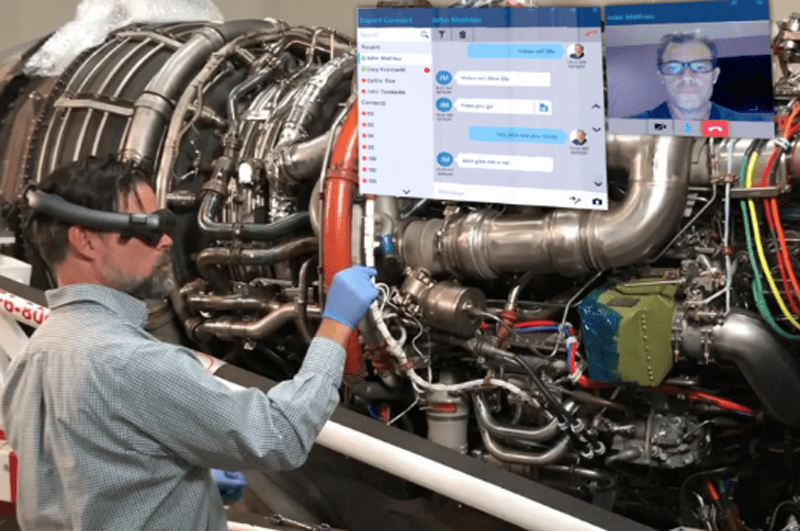
No matter what the reason is for a team to work remotely, whether they wind up working different days or fewer employees work per shift to comply with social distancing guidelines, AR solutions enable frontline workers to connect and work together virtually. Thanks to knowledge capture, digital tutorials and digital team reviews, everyone is given a chance to collaborate and everyone is empowered to be an expert.
At Taqtile, we believe in the power of expertise to drive business continuity, flexibility and resilience. We want to make every frontline worker an expert – especially now – and particularly for the oil and gas industry. We are a pioneer in implementing AR technologies to help capture skilled work instruction, and facilitate knowledge sharing and transfer. We can help your frontline workers become experts.
Kelly Malone is chief revenue officer at Taqtile, responsible for global sales, partnerships and marketing. He joined Taqtile in 2015 following his role as director of business development at Microsoft supporting the Windows platform team and specifically the HoloLens.
A software technology veteran, Malone spent over 10 years in a variety of sales, business development and product management roles at Microsoft. He also held sales vice president roles at Accenture and Spring Wireless driving and leading enterprise software sales to Global 2000 companies.
Malone has a master’s degree in business administration from the University of Wales. He enjoys cyclingand boating throughout the Pacific Northwest.