Capsol Technologies has developed a carbon capture and storage (CCS) technology based on hot potassium carbonate, which offers multiple advantages over conventional solutions and is well suited for treating emissions from waste-to-energy (WtE) plants. Vaisala’s new CO2 sensor MGP241 helps to optimize the process and maintain high CO2 capture rate.
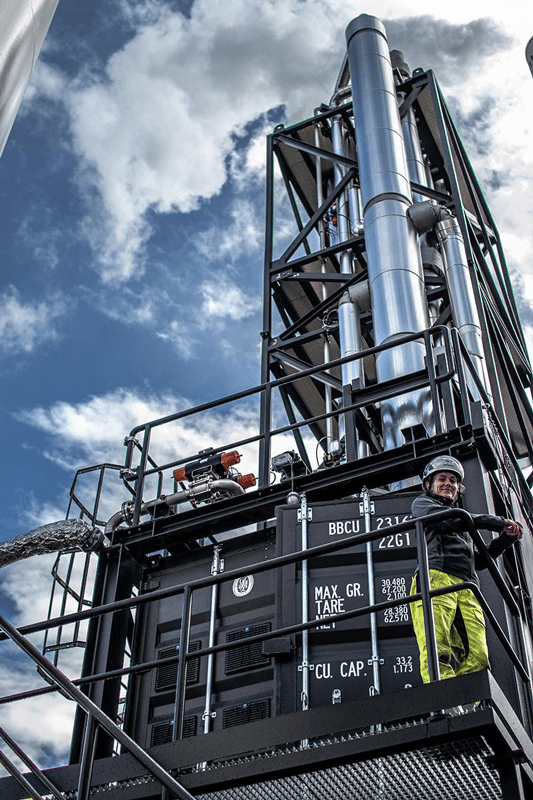
Application
Capsol’s modular CapsolGO carbon capture plant uses hot potassium carbon capture technology, where an aqueous solution of potassium carbonate undergoes a reversible reaction together with carbon dioxide and water.
The reaction is reversible based on the temperature and partial pressure of CO2, and the potassium carbonate solution loops through absorber and stripper columns with a patented heat recuperation stage which reduces energy losses and lowers operating costs of the carbon capture unit by approximately 40% compared to traditional solutions. Other advantages of potassium carbonate chemistry over amine and other solvents are that potassium carbonate is an inexpensive, non-toxic and non-volatile chemical.
The captured CO2 is liquefied and stored on-site for transport in a storage vessel. Possible uses for the captured CO2 include the beverage industry and greenhouses. Figure 2 shows a simplified flow diagram of a typical potassium carbonate process.

“The compact in situ measurement device is well suited for monitoring Capsol’s capture process and has performed well in both laboratory and field testing,” Anders Grinrød, Head of Innovation, Capsol Technologies.
In Capsol’s system, the absorber where CO2 is bound to potassium carbonate consists of two stages, and there are three CO2 measurement points in the system: One at the inlet, one between the two stages and one at the outlet of the scrubber where CO2 lean gas is returned to the WtE plant.
“The compact in situ measurement device is well suited for monitoring Capsol’s capture process and has performed well in both laboratory and field testing.” ~ Anders Grinrød, Head of Innovation, Capsol Technologies
Measurement of incoming CO2 level is used to estimate the load on the scrubber, i.e., how much CO2 needs to be removed. On the other hand, measurement of the outlet CO2 level tells the residual emissions to air, and together with the first measuring point it can be used to calculate carbon capture rate, which is a critical figure for overall efficiency of the plant.
The middle position between two scrubber stages provides a deeper process insight. If the CO2 level after the first scrubber stage is already low, it indicates that the scrubber is performing well. If, on the other hand, the concentration after the first stage is closer to the inlet level, it indicates that the process is not performing optimally.
Process parameters that can be adjusted based on the CO2 value after the first absorber stage include the temperature of the scrubbing material and its flow rate as an example. The three measurement points are shown in Figure 3, where three motor valves pass gas from the inlet, middle, and outlet locations to a common manifold.
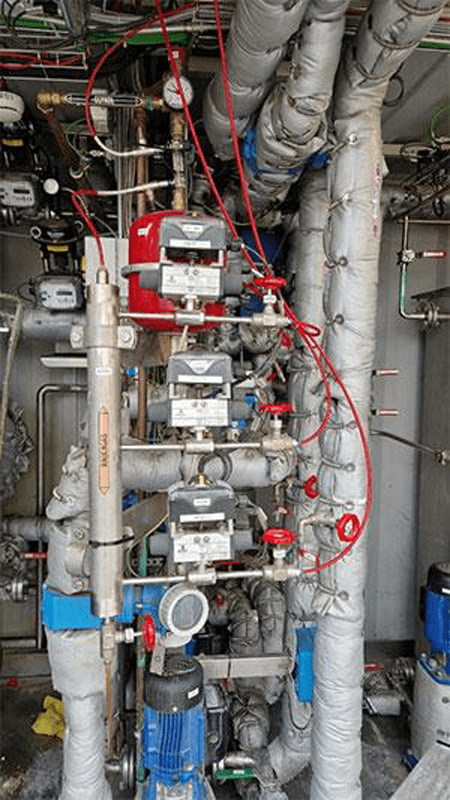
After extensive laboratory testing at Capsol’s Norwegian facility to prove its measurement performance, Vaisala’s carbon dioxide probe was installed in the CapsolGO system for a field test.
The field test included a comparison to an extractive process gas analyzer based on NDIR technology to demonstrate that a compact probe can give equivalent measurement results with a fraction of the cost and space requirements of conventional extractive gas analyzers.
The Vaisala MGP241 prototype was installed in a flow through adapter at the outlet of a QAL1 certified1 CO2 emission monitoring gas analyzer to ensure that the two instruments receive the same gas and the results are comparable.
In a standalone installation, the Vaisala MGP241 probe would be installed directly in the process, for instance in the sampling manifold shown in Figure 3. Alternatively, separate probes for each stream could be used to gain real-time insight on all measurement points without the loss of data associated with the multi-point sampling approach.
Results
Typical CO2 concentrations in the three positions are shown in Figure 4, where the three sample streams are separated to different trend plots, even though a single CO2 instrument was used to measure in succession from the three sample streams. The flat portions of the graph correspond to periods when the instrument was measuring one of the other two streams.
To evaluate the performance of Vaisala’s new MGP241, a comparison measurement where the output of Vaisala’s instrument is plotted as a function of the reference instrument was carried out.
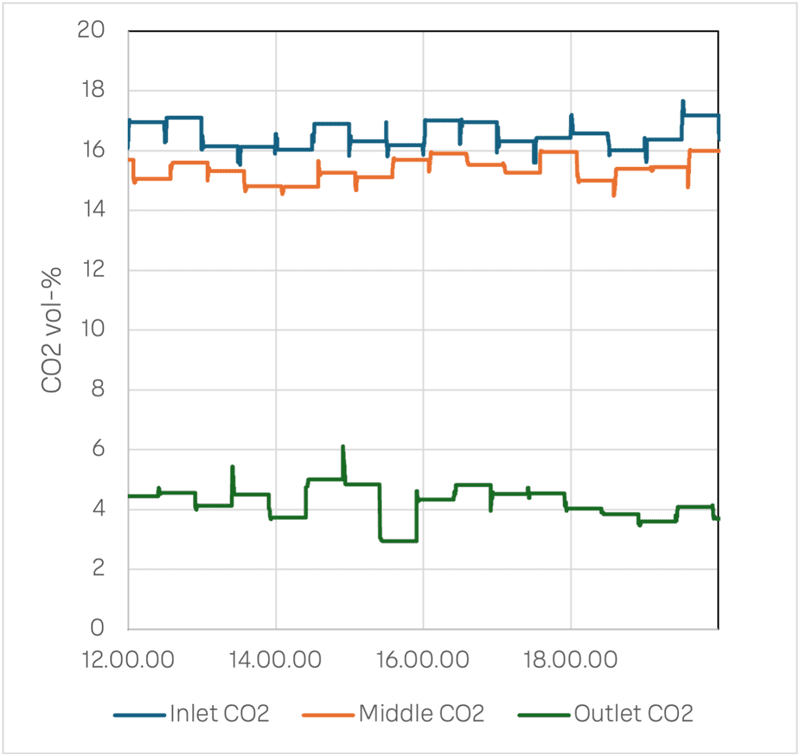
Three consecutive measurement runs of the inlet position and the outlet position, and one measurement of the middle position were carried out. In each run, a minimum of 30 measurement pairs were collected from both instruments. As the extractive reference instrument was measured on a dry basis, a dry gas compensation based on actual humidity value measured by MGP241 prototype was carried out.
Table 1 summarizes the averages of each run, and the parameters of the calibration curve and its correlation coefficient plotted to this data.
Figure 5 shows the same data in a graphic representation. The test results demonstrate good agreement between the two methods, and the variation between runs in the Vaisala results are smaller than in the reference method, indicating good repeatability and reproducibility of the method.
Table 1. Comparison of Vaisala MGP241 prototype (AM) and Standard reference method (SRM) carbon dioxide readings. | ||
SRM, vol-% CO2 | AM, vol-% CO2 | |
Outlet #1 | 0.78 | 1.12 |
Inlet #1 | 16.50 | 17.05 |
Midpoint #1 | 15.51 | 15.32 |
Outlet #2 | 0.73 | 1.10 |
Inlet #2 | 17.88 | 16.96 |
Outlet #3 | 1.48 | 1.30 |
Inlet #3 | 16.87 | 16.96 |
y = ax + b | ||
Slope a | 0.97854 | |
Intercept b | 0.2227 | |
Correlation coefficient R2 | 0.9984 |

Performance
CapsolGO modular CCS platform is a flexible and scalable solution for point source carbon capture in a variety of industries with flue gas CO2 concentrations ranging from 3 to 30 vol-%.
The Vaisala MGP241 carbon dioxide probe is a perfect solution for a compact, container-based solution such as this, as it requires minimal space inside the container, has no moving parts or need for calibration gases and provides data directly to the DCS system.
According to Anders Grinrød, Head of Innovation at Capsol Technologies, the compact in situ measurement device is well suited for monitoring Capsol’s capture process and has performed well in both laboratory and field testing. The MGP241 is also remarkably easy to install and commission, the task was carried out by the joint Capsol-Vaisala team in less than an hour.
[1] QAL1 or EN 15267-3 certification covers performance specifications for gas analyzers and is comparable to performance specifications found in 40 CFR 60 appendix B in the United States.
Antti’s focus is on multigas infrared instruments and developing products for wholly new market areas.
With over 15 years of experience in process and emission monitoring instruments and infrared gas analysis, Antti holds a M.Sc. in Physical Chemistry.
He is an active member of multiple international standardization workgroups (both ISO and CEN) on air quality and greenhouse gas measurements.
Oil and gas operations are commonly found in remote locations far from company headquarters. Now, it's possible to monitor pump operations, collate and analyze seismic data, and track employees around the world from almost anywhere. Whether employees are in the office or in the field, the internet and related applications enable a greater multidirectional flow of information – and control – than ever before.