Confined spaces in the oil and gas industry present a distinct set of safety challenges. These areas, which include storage tanks, pipelines and process vessels, are essential for production and maintenance activities. However, they also pose inherent risks to workers. Below, we discuss the primary confined space safety concerns oil and gas workers face and offer practical tips for mitigating them.
Hazardous Atmospheres
The Occupational Safety and Health Administration (OSHA) defines confined spaces as areas with limited entry and exit points, poor ventilation, and the potential for hazardous atmospheres. These safety concerns are significantly heightened in the oil and gas industry, where gas leaks and chemical processes that degrade air quality are common occurrences. Confined spaces may contain toxic gases, lack sufficient oxygen or accumulate flammable vapors, considerably compromising worker safety.
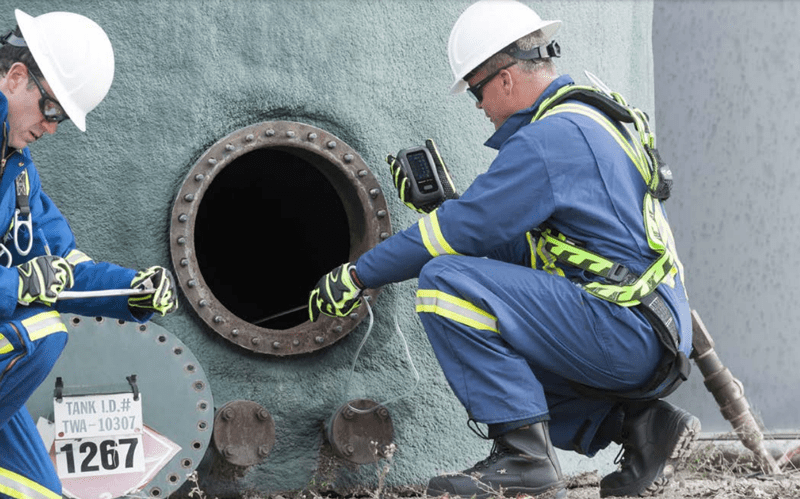
Here’s a closer look at these hazards:
- Toxic Gases: Hydrogen sulfide (H2S) is common in oil and gas operations, particularly in areas where crude oil or natural gas is processed. Even low concentrations of H2S can cause health problems, such as respiratory distress, dizziness or loss of consciousness.
- Oxygen Deficiency: In confined spaces, oxygen levels can quickly drop due to several factors, including consumption by chemical reactions, displacement by other gases, and poor ventilation. A drop in oxygen levels, even by a small percentage, can cause dizziness, fatigue and unconsciousness.
- Flammable Atmospheres: Confined spaces in the oil and gas industry often contain volatile organic compounds (VOCs) and hydrocarbon emissions, which can form explosive gas mixtures. Even a tiny spark from equipment, tools or static electricity can ignite these gases, leading to devastating explosions.
- Mitigating Risk: Continuous air monitoring is crucial in confined spaces. Before entry, workers should use multi-gas detectors to test for oxygen levels, flammable gases, and toxic substances. Additionally, ensuring adequate ventilation and providing respirators with appropriate filters is pivotal to ensuring worker safety in confined spaces.
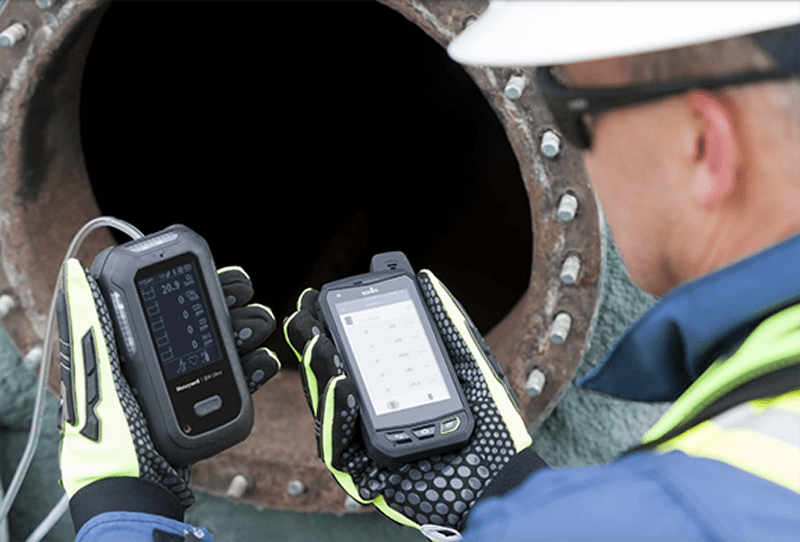
Limited Entry and Exit Points
Confined spaces often have few, if any, easily accessible entry and exit points. In addition to restricting movement during normal operations, this can create significant challenges during emergencies. Should something go wrong inside a confined space, such as a sudden gas leak or equipment malfunction, workers’ ability to evacuate the area can spell the difference between life and death.
The restricted access also makes it difficult for rescue teams to reach distressed workers. In most cases, rescue personnel rely on specialized equipment, such as rescue tripods and harnesses, to extract workers from confined spaces. This process can be time-sensitive, with delays amplifying the potential for serious injuries or fatalities.
Mitigating Risk: Establishing thorough safety protocols and emergency response plans is essential to mitigating the risks of limited entry and exit points. This can involve task-specific training and requiring safety equipment like fall protection harnesses, self-retracting lifelines (SRLs), and personal gas monitors.
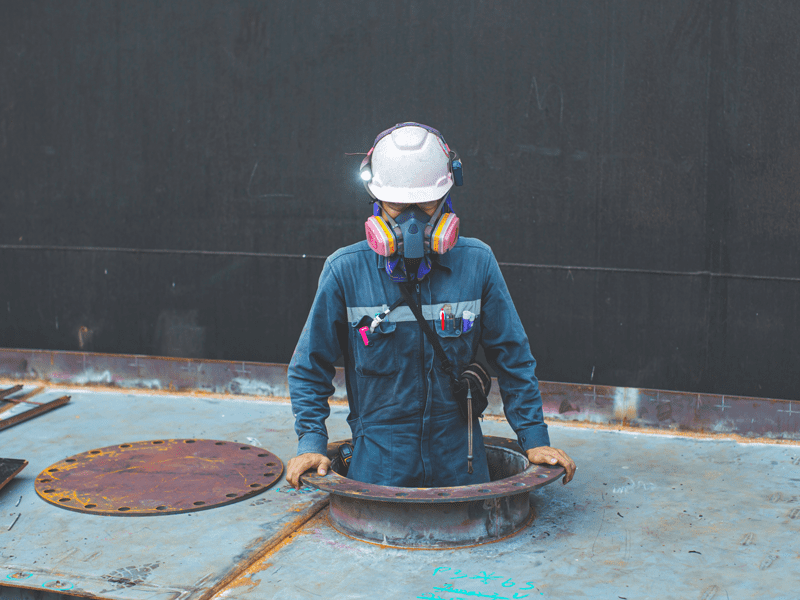
Engulfment Hazards
Engulfment occurs when loose materials such as sand, mud, oil or liquids rapidly fill confined areas and trap workers. This can lead to suffocation or drowning if workers cannot free themselves quickly. Storage tanks, silos and other similar spaces used in oil and gas production are particularly vulnerable to engulfment hazards. Workers performing cleaning, maintenance or inspection tasks are at higher risk, as they may be unaware of material buildup or the sudden release of substances in these spaces.
Mitigating Risk: Workers should avoid entering confined spaces containing unstable material loads. If entry is unavoidable, isolate the confined space from potential engulfment hazards (e.g., pipelines, machinery) to prevent accidental releases.
Physical and Mechanical Hazards
Confined spaces used in oil and gas operations often house rotating parts, agitators and other machinery that, if not properly de-energized, can cause severe injuries, such as amputations or crushed limbs. Additionally, pressurized systems like pipelines carrying hydrocarbons can further heighten the risks.
Meanwhile, inadequate lighting and cramped conditions within confined spaces can contribute to musculoskeletal strains, injuries and fatigue. Workers may also find it difficult to operate machinery safely with constricted space, especially with poor visibility.
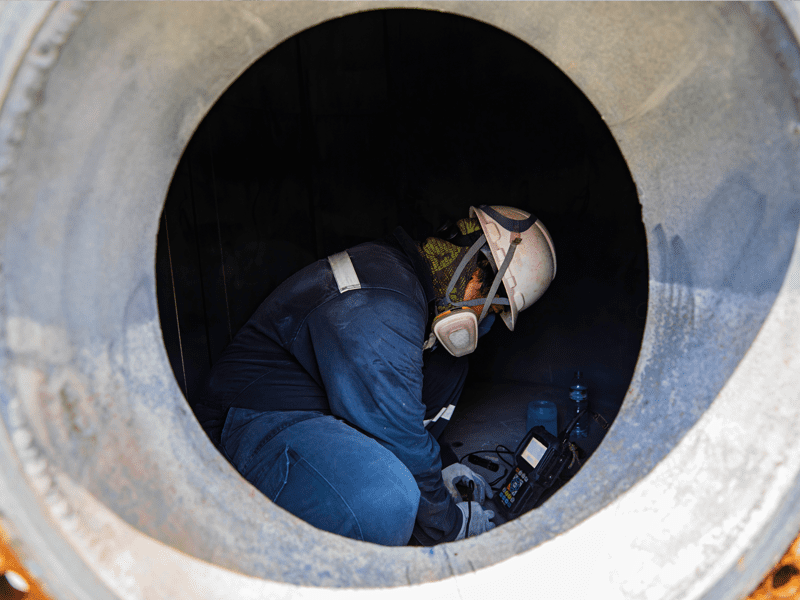
Mitigating Risk: Establish strict lockout/tagout (LOTO) procedures to ensure machinery is properly de-energized before workers enter confined spaces. The “lockout” involves physically locking the equipment’s energy isolation devices, such as switches or valves, in an off or neutral position, while the “tagout” uses warning tags to indicate that the equipment should not be operated.
Extreme Temperatures
Confined spaces in oil and gas facilities, particularly in harsh environments like offshore platforms or desert operations, expose workers to extreme temperature fluctuations. In these conditions, workers face an increased risk of heat stress due to poor ventilation, high ambient temperatures, and physically demanding tasks. This can lead to dehydration, exhaustion or even heat stroke.
Oil and gas workers are particularly vulnerable when performing tasks that require full-body PPE, which can limit the body’s ability to dissipate heat effectively.
Mitigating Risks: To protect against heat stress, employers should schedule work during cooler periods whenever possible and mandate hydration breaks. The PPE provided should also be evaluated to ensure it balances protection with comfort in high-temperature environments.
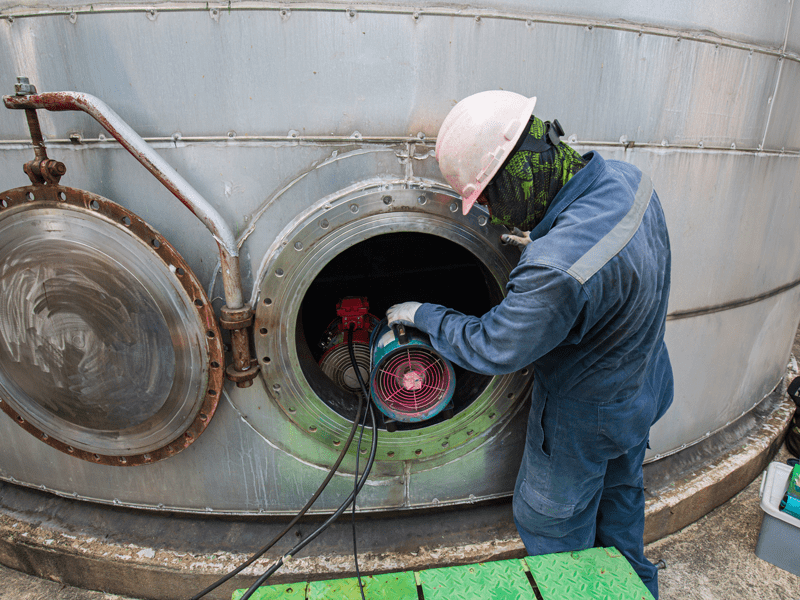
Lack of Communication and Coordination
Confined space work often involves coordination between multiple teams, including operators, safety personnel, and emergency responders. Confined spaces may limit access to radio signals or other communication tools, making it harder for workers to stay connected with relevant teams.
Without clear communication, workers may become unaware of potential hazards brought by environmental and situational changes. Aside from increasing risks, this lack of coordination can hinder rescue efforts if an emergency occurs.
Mitigating Risks: Comprehensive communication protocols are vital to confined space work. Pre-job briefings, continuous updates, and regular check-ins can ensure that relevant teams are on the same page and ready to respond to potential issues.
While confined space work in the oil and gas industry presents numerous safety challenges, the appropriate precautions can mitigate these risks. Identifying hazards such as dangerous atmospheres, mechanical threats, and communication barriers is just the beginning. The real key lies in fostering a safety-first culture – one that prioritizes rigorous training, strict adherence to safety protocols, and proper protective equipment. This enables oil and gas companies to protect workers and ensure more resilient and responsible operations.
Headline Photo: Conspace Tripod. Photo courtesy of FrenchCreek.
Rick Pedley, PK Safety’s President and CEO, joined the family business in 1979. PK Safety, a supplier of occupational safety and personal protective equipment, has been operating since 1947 and takes OSHA, ANSI, PPE, and CSA work safety equipment seriously. PK Safety's customer service can be reached at 800-829-9580 or online at https://www.pksafety.com/contact-us.
Oil and gas operations are commonly found in remote locations far from company headquarters. Now, it's possible to monitor pump operations, collate and analyze seismic data, and track employees around the world from almost anywhere. Whether employees are in the office or in the field, the internet and related applications enable a greater multidirectional flow of information – and control – than ever before.