Offshore makes a comeback. Bloomberg reports that investors expect offshore investment in 2019 to increase for the first time in five years.
The greater offshore investment has also led to higher demand for digital technology, in large part to gain greater transparency of workflow processes and data. The digital twin creates a virtual replica of the offshore field, allowing for smarter, more collaborative and efficient field planning and operations.
For many new projects, companies look to implement digital field twins from day one to enable smarter business decisions from planning through development. Oil and gas operators and service providers already use digital software to plan and build new fields digitally in the cloud, see tremendous potential to introduce new, more transparent digital workflow processes into their operations.
Global Collaborative Environment
Digital twin enables true workflow collaboration and information transparency in offshore development. The digitized field data moves teams away from a traditionally siloed work environment with a variety of owned, non-integrated tools, applications and data to a global collaborative environment. Operators can now collaborate cross-departmentally within the enterprise, as well as with outside contractors as everyone works from the same real-time data. Greater visibility and collaboration leads to better business decisions and greater safety procedures with reduced staffing requirements. Digital twin technology uses Open Web technology to access and view the data at any point no matter where you sit in the world.
Digital twin generates a virtual field in the cloud to offer greater transparency.
Additionally, big data significantly transforms the bidding process for oil and gas engineering firms. Historically, the basic bidding process captured brainstormed ideas from engineers on flip charts and in PowerPoint and then converted them into visuals via Visio, Corel Draw and MS Paint. An outsourced engineering house would then transform them into Computer Aided Design, or CAD, files. This legacy engineering design process limited the EPC firms’ ability to meet tight design schedules and implement late changes quickly.
Emerging technologies are proving they can generate many more field concepts in a much shorter time while helping to eliminate inaccurate options. By uploading data to the cloud, digital twin technologies are able to visualize subsea fields and run computations from a single source of data. For instance, McDermott uses FutureOn®’s FieldAP™ – a FieldTwin™ platform application to respond far more rapidly and efficiently to new project opportunities as well as develop multiple concept proposals – in just 20 percent of the time it took to develop a response in the past. The tool accelerates project timelines by up to 80 percent during the early concept and FEED (Front-End Engineering Design) phases.
Data Transparency
The data transparency via visualization enables teams to see more about their assets from every vantage point and every point in time via real-time 3D digital simulations. This allows engineers to explore more ideas, more rapidly, in collaboration with colleagues all around the world. Through the power of data visualization, engineers examine multiple possibilities in minutes rather than days, weeks or months required in years past. This speed results in 30 percent reduction in pre-feed field design and significantly more successful bids for EPC firms.
Data Integration and Cost-effectiveness
Internal resistance to technology happens because engineers fear the emerging tools will not integrate into legacy systems. These new technologies, however, are being designed with integration in mind. Through an API, these digital technologies are bringing expert engineering systems data directly into a single platform so engineers don’t have to close out of one system to open a flow simulation in another software.
Companies may budget cost-effective digital platforms as an operational expense rather than CAPEX (capital expenditure) with a return seen immediately, i.e., $45,000 in cost savings associated with outsourced drafters. Traditional digitalization approaches can involve significant upfront CAPEX. IoT devices, SMART sensors and robotic tools require costly new equipment investments, employee training and retrofitting of existing systems. The return on investment is difficult to assess.
As offshore investment increases, companies must adapt to gain competitive advantage initially – and to remain competitive as digital adoption rapidly progresses. Digital twin technology can play a big part in moving the industry forward for greater collaboration, smarter field development and enhanced operations, all while reducing costs to retrieve the oil more quickly.
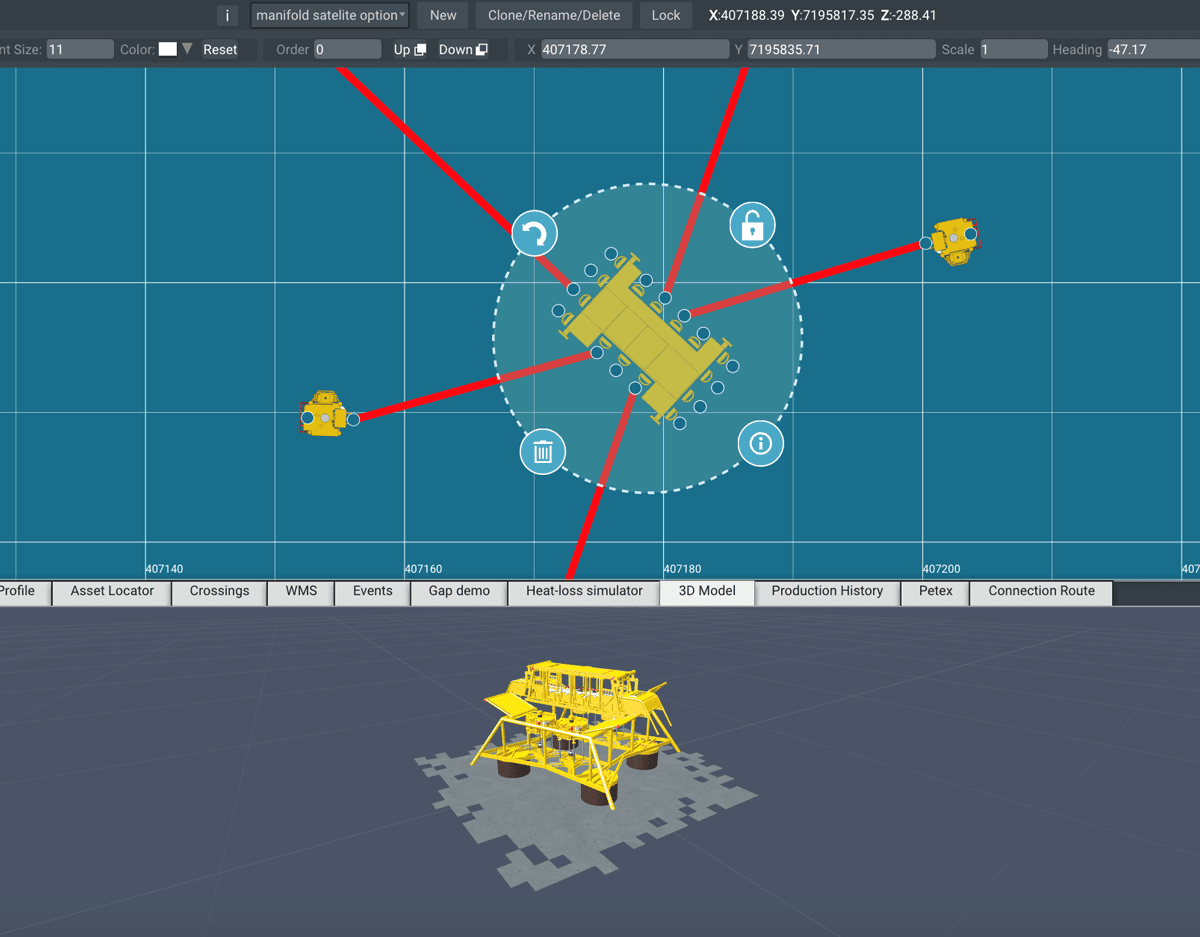
the cloud. FutureOn is the only digital solution provider to receive
the 2019 OTC Spotlight on New Technology® Award.
Thornton Brewer is the digital experience and marketing lead at FutureOn, a 2019 OTC Spotlight on New Technology® Award recipient. For more on how we help maximize the value of new fields, visit FutureOn.
Oil and gas operations are commonly found in remote locations far from company headquarters. Now, it's possible to monitor pump operations, collate and analyze seismic data, and track employees around the world from almost anywhere. Whether employees are in the office or in the field, the internet and related applications enable a greater multidirectional flow of information – and control – than ever before.