Production Downturn Summary
The global oil industry has been in crisis since March. While recovery has begun, we must ask: is the worst behind us or can the industry recover? Visibly fewer commuters are on the road needing to fill up at the gas pump, but what about the myriad of manufacturers dependent on the oil and gas industry for materials used in the manufacture of products for critical services or everyday consumers? Is that demand on the sector gone or is it stronger than ever?
Paradoxically, the same downturn that has led to record low prices at the gas pump and sent shockwaves through investors and contractors has elevated the already high demand on the oil and gas industry to provide materials needed in the manufacturing sector.
Effect on Downstream – Petrochemical, Chemical, and Plastics
Manufacturers rely on the oil and gas industry for its primary material: petroleum. Petroleum, or crude oil, is a liquid mixture of hydrocarbons found in underground geologic formations. Petroleum is pulled to the surface, refined, and separated to be used for a variety of purposes.
Petroleum provides a vast assortment of polymers needed by the plastics industry. Polymers –like polyethylene, polystyrene, and polypropylene – are essential components of plastics. These versatile materials can be molded, extruded, cast, and blown into containers, films, foams, and fibers.
Plastics are lightweight and abundant and provide the perfect building blocks for products and packaging made for the pharmaceutical and medical industries.
Importance of Plastic Medical Supplies and Devices
Modern healthcare is not possible without the use of plastic materials. Plastics have made supplies and devices lighter weight, cheaper to produce, and easier to sanitize or to dispose. Health care providers have an endless inventory checklist of equipment, supplies, and devices needed in hospitals, doctors’ offices, clinics, and emergency rooms across the country.
Even implants and prosthetics use plastic parts for the creation of smooth joints with better flexibility. Traditionally, metals, glass or ceramics were used for implants, devices, and supports, but plastics have opened a wave of innovative products that are lighter, cheaper, and offer better biocompatibility.
The most common polymers used in medical applications are polyvinyl chloride (PVC), polypropylene (PP), polyethylene (PE), polystyrene (PS) as well as nylon, polyethylene terephthalate (PET), polyimide (PA), and polycarbonate (PC), among many others. These materials are essential to the manufacture of the myriad supplies that are now in high demand across the world for medical and pharmaceutical emergencies.
COVID-19 Crisis Exposes Supply Chain Gaps
Pharmaceutical companies and medical device buyers have become reliant on global sourcing to lower costs. Recent events, coupled with the lack of supplier diversity, have exposed gaps in the supply chain. Single source commodity supply chains may drive down costs, but the lack of redundancies can have disastrous consequences when supply cutoffs resulting from catastrophic events occur. For instance, hospitals have been forced to use non-optimal solutions to correct shortages of essential supplies and devices (such as Personal Protective Equipment (PPE) made of garbage bags). It is easy to see how increased shortages may lead to closed doors to sick patients. China, one of the top global producers of chemicals, has been hit hard recently. When factories across China closed due to the corona virus, its chemical industry. which had already been hit hard by the tariff war, nearly ground to a halt. Regional manufacturers, like India, that rely on chemical exports from China, were folded into the supply chain issue. As the dominoes fell, regional manufacturers could not produce enough of the petroleum-based products used by American hospitals to stock medical supply closets. Without supplier diversity, procurement managers cannot react quickly enough to mitigate the shortfalls of the supply chain system that had once protected the bottom line.
Latest Outlook for Oil and Gas Sector
Oil and gas strategists want to know that future returns will be strong before investing and many jobs in the sector are on the line waiting to see if oil prices will rebound. Questions about Russia and OPEC play a part in forecasting rebounds, but is the bigger picture decided by more than just the big players?
More states are lifting stay at home orders and bringing people back to work and shop. Prices at the gas pump are currently down leaving more dollars in the pockets of everyday U.S. consumers to spend their money elsewhere. Add that to the demand found in the medical and pharmaceutical industries and it leaves an opening for the oil and gas industry to meet the fierce demand with supply. It is likely that the oil and gas industry will see a strong recovery parallel to the economies in which it works. Or more simply put, as the economy in a given region or country recovers, so, too, will the oil and gas industry at roughly the same rate.
Opportunities for the U.S. Oil and Gas, Chemical, and Manufacturing Sectors
Trade wars and a pandemic have wreaked havoc on the chemical sector, but plants are still in operation and the need for petroleum-based products is still high – if not higher than before – due to depleted stockpiles. Demand for pharmaceutical and medical supplies has skyrocketed, but buyers are scrambling to find cost-effective and reliable sources. The future of supply chain management will be a balancing act between cost and risk with an increase in the need for domestic manufacturers. Could this break China’s hold on the chemical industry and be a boon for the resurgence of the U.S. manufacturing sector?
The U.S. still has an abundance of oil needed to supply the U.S. chemical industry. U.S. chemical plants will need to make materials required by the manufacturing sector to create high demand petroleum-based products. Add to that the large unemployed population eager to get back into the factory and reignite U.S. manufacturing. Can we keep costs down enough to encourage the medical and pharmaceutical industries to diversify?
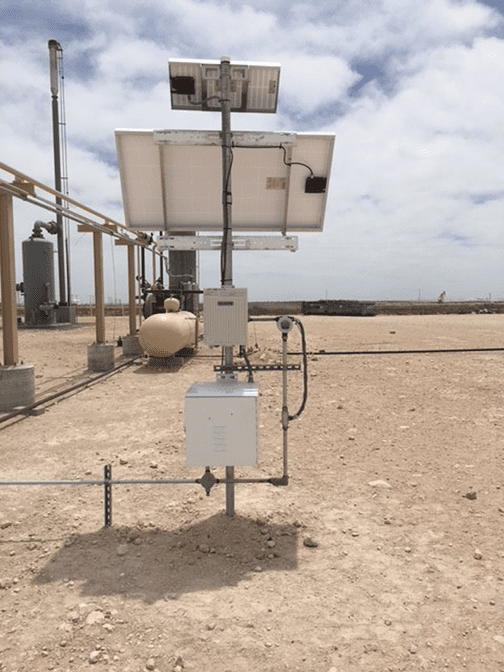
5 Keys to Reinvigorating the U.S. Manufacturing Sector
There have been vast improvements in process efficiency and equipment performance, but the manufacturing sector of yesterday must evolve to fit the demands found in the modern marketplace.
1. Managing Big Data for Greater Profitability
There is more accessible data than ever and the manufacturing sector inevitably must tie into the collection and effective management of this data to improve the ability to foresee shifts in customer needs. Ideally, this process will also drive the move from a product-focused mindset to a customer-focused mindset that continuously works to address customer needs and improve the customer experience.
2. Knowledgeable Staff
Technology improvements are happening at ever-increasing rates, regulations are in a state of flux, and the market makes swift and regular changes. Having a talented in-house team to track the results and innovate at key times is paramount to the success of manufacturers. Attracting and retaining a team that can keep performance high, improve efficiencies, and track regulatory compliance will ensure that the manufacturer can shift along with the needs of the industry.
3. Reliable, Flexible, and Efficient Process Equipment for Automation
Industry 4.0 has encouraged the manufacturing sector to move beyond outdated processes and manifest a culture of innovation to deliver value. Error detection, AI, and robotics have fueled a manufacturing transformation that is forward-thinking and ready to rapidly adapt to changes in the market.
4. Accurate and Reliable Instrumentation
The successful automation of processes is dependent on an array of sensors and instrumentation to feed data into the control system. Response time and accuracy are vital to system performance and overall operation success. The reliability of instrumentation to perform consistently is also critical. Out of the box, the instrument is expected to perform according to specifications, but over time performance may drift. Each instrument manufacturer must supply certification of accuracy, performance, operation, and/or calibration to applicable standards. Beyond the purchase, manufacturers must offer a way to check or reassure the reliability of performance after the passage of time. All process equipment and instrumentation must be updated on an enforceable maintenance schedule.
5. Quality Control and the Customer Experience
Today’s customers have greater access to choices, a shorter attention span, and high expectations. Brand loyalty is harder to attain and retain than in the past. If the customers’ expectations are not met the first time, it is unlikely they will return for a repeat buy. This permeates the B2B market now more than ever. Engineers, procurement managers, and consultants expect to find what they are looking for easily and quickly online.
In general, manufacturers must try harder at every point of the sales funnel, operation, and customer service to perform above the competition. This requires a great customer-facing experience online, fast and responsive service during negotiations, easy access to order information, quick product and service production and delivery, and exceeding expectations for service inquiries.
Summary
The oil and gas industry has always been cyclical and will repeatedly be confronted by challenges over time. The chemical and manufacturing sectors in the U.S. have been on the path to maximize profits by seeking lower prices offshore during the rise of globalization. The impulse to narrowly focus supply chains has proven too risky. Like it or not, the oil and gas industry is closely linked with the U.S. chemical and manufacturing sectors and each directly impacts the success or failure of the other. It is imperative that players in these industries take notes, regroup, and turn failure into strategy.
Headline photo courtesy of Shutterstock
Ria Edens got her start in construction, served as water and sanitation extension agent in sub-Saharan Africa, then moved into the private sector after completing a graduate program. Today, Ria Edens is Marketing Communications Manager for Fox Thermal and Air Monitor Corporation with over 10 years’ experience in the instrumentation manufacturing sector selling to the global industrial, oil & gas, and wastewater markets.
Oil and gas operations are commonly found in remote locations far from company headquarters. Now, it's possible to monitor pump operations, collate and analyze seismic data, and track employees around the world from almost anywhere. Whether employees are in the office or in the field, the internet and related applications enable a greater multidirectional flow of information – and control – than ever before.