Well drilling, the second step in the downhole process, begins when the superficial casing is put in place and ends when the well is set to begin the hydrocarbon production. It is commonly the process of greatest investment; for this reason, it is the main gauge when studying new projects.
Because of what drilling means for the investment of the project, all the operational problems that generate loss of time are taken into account. When this NPT (Non-Productive Time) is taken into account in the wells in the Gulf of Mexico, the study outlined in “New Drilling Optimization Technologies Make Drilling More Efficient” by D.C-K. Chen revealed that 25 percent of lost time is NPT, translating to $1.5 million per well.
According to Chen, operational problems such as loss of circulation, variations of the EDC, pipe clamps or problems related to borehole cleaning, among others, are problems that go hand in hand with borehole stability, and he explains that the best way to deal with these difficulties is with the continuous use of new tools and techniques for drilling.
Understanding the needs of the market, the drilling process has been perfected over time, so have the special tools for projects and the use of new techniques to meet the different operating needs of the formations, in order to create a solution for each problem, or a single solution for several problems.
Tools Used in Drilling
The tools used for drilling consist basically of the drilling rig; this element has different versions that have been born over time, in order to reach new levels.
The drilling rig is an element composed of elements such as crown block, derrick, traveling block, swivel, standpipe, Kelly, rotary drive, draw works, engines, blowout prevention equipment, mud pump and mud pit. On surfaces and in the subsoil, it consists of drill pipe, casing, cement and drill bit. This is the basic configuration of a drilling rig; this group of elements represents the four systems that govern drilling.
- Lifting system
- Rotation system
- Circulation system
- Power system
Its mission is to ensure a surface/reservoir connection and thus transport fluids trapped in the subsoil. Although it is easier said than done, an easy goal does not always exist, so there are different alternatives for different challenges:
- Percussion drilling: When there are wells to be built at depths not greater than 30 meters, this type of method is most often used, as it works for unconsolidated formations. The first of the drilling methods used, it was based on employing a hard and heavy bar that had a drill bit at the tip, which collided against the soil repeatedly, shrinking the gravel with the help of a bailer. The structure is a tripod that supports the weight and the drilling process was done by using cables. To maintain the stability of the borehole, a casing was used that prevented it from collapsing and, at the same time, isolated the procedure. This method is still applied in Australia.
-
Percusion drilling. Photo courtesy of Dando Drilling & Prospecting International Rotary drilling: With the passage of time, research offered new opportunities to exploit oil, but meant drilling to greater depths. Due to this, one of the most common forms of drilling in the world was born. Originally built for wells of more than 3,000 feet of depth, over time it varied to what it is today. The equipment consists of a tower of about 40 meters which supports the equipment configuration, and contains a motor that, along with the rotary table, is in charge of generating the drilling, the drill bit being responsible for destroying everything in its way. The fluid control equipment is responsible for raising the gravel to the surface and maintaining the pressure differential in equilibrium. In turn, it is connected to the system, thus preventing blow-outs, being able to send a line of fluid pressure to counteract the pressure of the formation, if necessary. Capable of working in any type of formation by modifying certain elements and, with a speed of 40 to 250 rpm, this drilling rig has been on the market for over 50 years.
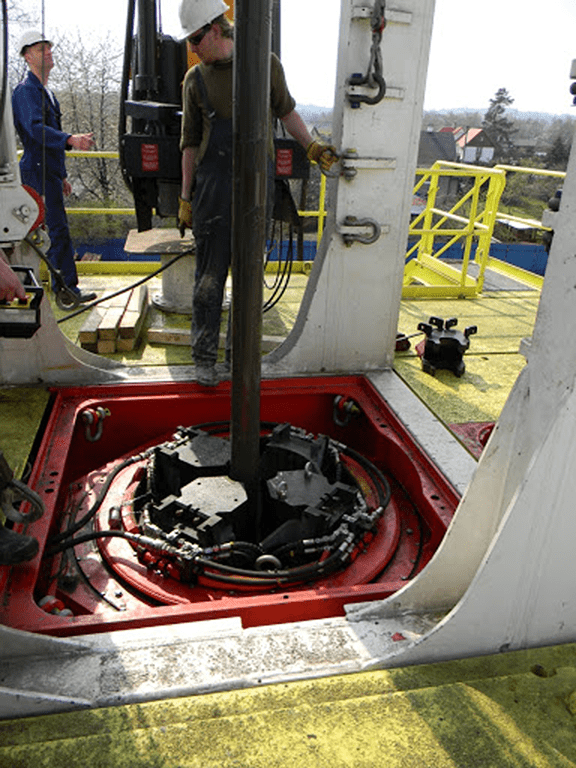
Drilling Rigs
Drilling rigs were born from the idea of making direct drilling on the seabed. The reason? Geological studies showed large reservoirs established in the sea and the best way to take advantage of them was with the use of boats equipped to move the drilling rigs and to be autonomous in order to perform the whole process.
The common operation of this type of drilling is using a rotary table, and over time different drilling rigs were developed, such as:
- Drillship
- Semi-submersible platform
- Self-elevating platform
- Fixed platform
In the beginning, they consisted of necessary equipment to fulfill tasks; today, they have comfortable facilities to accommodate professionals.
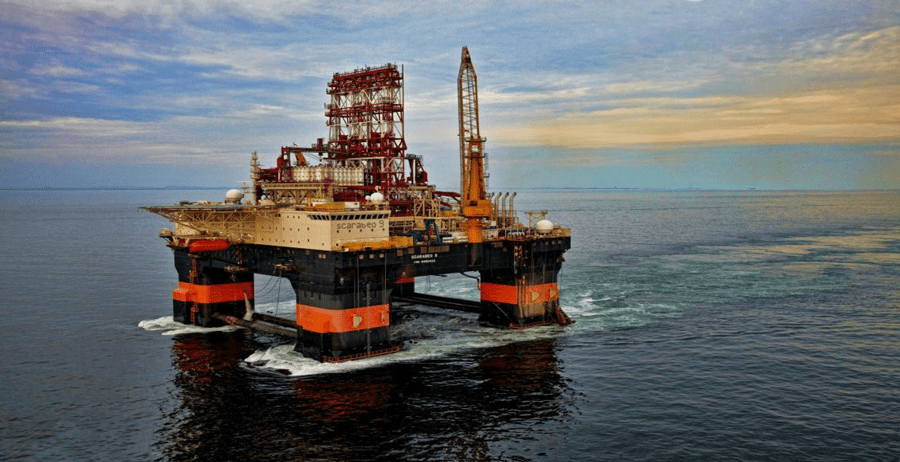
Directional Drilling
Directional drilling rigs are a necessary variation born from the common rotary table rigs, there are different configurations, but they are based on the use of a bottom motor that is responsible for controlling the direction of the drill bit, from the surface the position of the drill and its degrees of inclination is controlled, either with a manual or digital system.
This drilling rig was born in view of the need to create oriented wells; in turn, it has the ability to create several wellbores from the same location on the surface, providing low costs and solutions to geological problems. It is used globally and companies such as Halliburton or Schlumberger, among others, use this technique in marine stations, managing to exploit the reservoirs optimally.

Electro Drilling
This type of drilling is similar to rotary drilling but, unlike being driven by combustion engines, electro drilling is driven by electric motors. This important difference includes the change in the type of control to the drilling, the rotor that drives the movement of the drill bit is close to it, being only a few tubes above it.
Currently used in Nordic and Asian countries, it provides the benefits of a hydraulic drilling rig and is applicable in high pressure, high temperature (HPHT) conditions. The biggest drawback of this drilling rig is its maintenance but, despite this, it is an optimal option for new fields.
Drilling Techniques
Drilling techniques vary according to the type of challenge faced. The correct choice of drilling rig, drill bit, location and other factors is only the first part of the job. With the knowledge of the conditions of the formation comes a critical decision: drilling under balance or over balance.
Drilling Over Balance
This drilling technique is the most used in the world. With the use of drilling fluids of optimal features, it tries to increase the hydrostatic pressure that causes the liquid column on the sidewalls to overcome by a margin of 15 percent or more, ensuring that the fluids found in the different formations that are drilled stay in their place and do not enter the well.
Commonly used to prevent bursts in areas of over formation pressure, and when the conditions of the formation are not fully known, this type of technique creates larger whitewash on the sidewalls, making the area cleaning do-overs more concurrent, and also making it more difficult to lift the gravel to the surface resulting in longer operating times. It is used in all types of formations from extra hard to soft, and it is very common for drilling mud to enter the washed area of the target reservoir.
Drilling Under Balance
Mainly used in consolidated formations, the drilling under balance technique consists of employing a hydrostatic pressure similar to or less than the one offered by the formation. The least amount of pressure is used where there is a functional balance in which the sidewalls maintain the balance and where the formation fluids do not enter the wellbore.
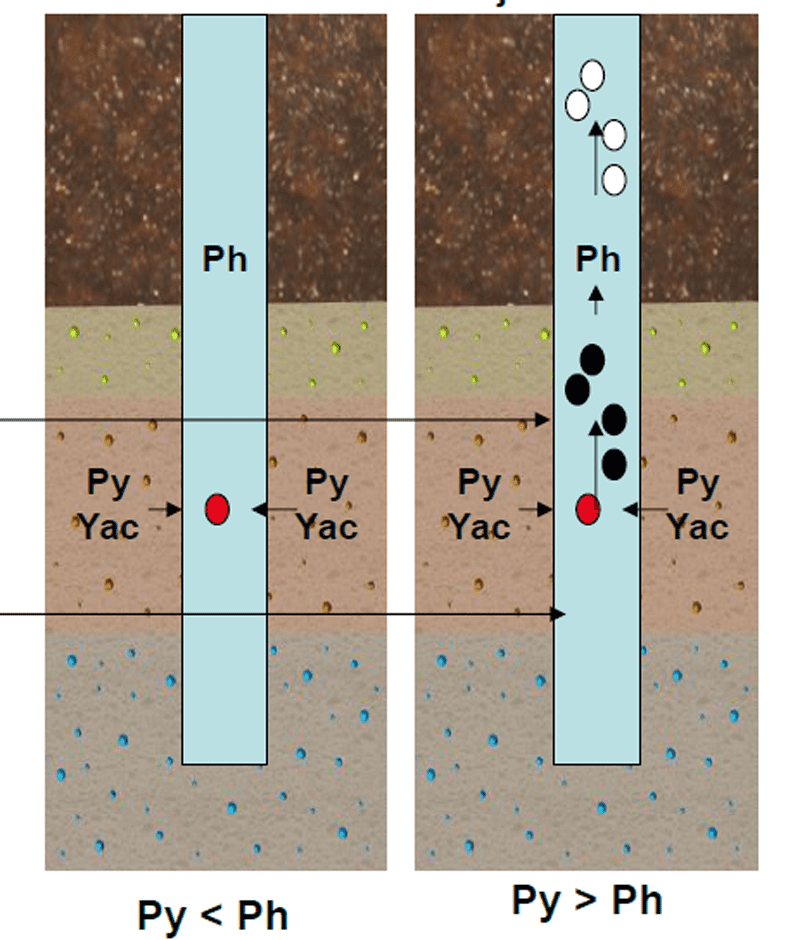
For the use of this method, it is necessary to have a complete knowledge of the formation, especially of the behavior of the shale, since these are the ones that normally represent the zones of over pressure. When a balance is achieved, the expenses of densifying material decrease, the creation of very thick seals on the sidewalls is avoided, which prevents operational problems such as pipe pegs, area cleaning do-overs and creation of caves, among others. This translates into saving time, which in turn is the direct definition of saving money.
It is not common to use this technique for the construction of oil wells, due to the margin of risk faced by the work team, but it is very common to use it to drill the target area. With the use of RFT or MDT equipment to calculate pore pressure, the response pressure of the reservoir is known. This facilitates the task of cannonade and helps exponentially to handle a low skin factor.
Drilling is a task that, despite maintaining its original essence of using a drilling rig to break the balance of the subsoil, has found itself obliged to evolve over the years to provide an answer to the different challenges faced by the industry, as it seems, the industry will not cease to have new obstacles and the engineer surely will not cease to have new answers.
Headline photo courtesy of Liebherr: Drilling equipment and technique.
Raul Palencia is an engineer and researcher with more than 10 years of experience as a geologist. He graduated from the prestigious University of Andes (ULA), later he received a master’s degree in reservoir engineering at the Venezuela Hydrocarbons University. During his career development, he worked for oil companies in positions such as: field geologist, reservoir engineer and reservoir simulation. He has worked in Argentina, Ecuador, Mexico and Venezuela. He currently resides in Texas.
Oil and gas operations are commonly found in remote locations far from company headquarters. Now, it's possible to monitor pump operations, collate and analyze seismic data, and track employees around the world from almost anywhere. Whether employees are in the office or in the field, the internet and related applications enable a greater multidirectional flow of information – and control – than ever before.