Determining which automatic tank gauge works for a specific application is more complex than simply comparing product prices or performance specifications. There are numerous factors associated with installing a gauge that can inflate costs and cause an operator to exceed budget. These factors can lead to expenses that overshadow the cost of the level transmitter itself.
The most significant of these factors includes the need for tank modifications, cabling and conduit, and auxiliary equipment. Operators specifying a specific level transmitter should work with manufacturers to determine the estimated installed costs of the main automatic tank gauge technologies. Only then can they choose the technology that meets their needs within their budget.
What Options are Available?
First, operators need to understand their options. There are three prominent level measurement technologies used in aboveground storage tanks in the upstream oil and gas market. They are Magnetostrictive, guided wave radar (GWR), and ultrasonic based technologies. Each technology offers specific benefits that meet the needs of different customer applications.
Each utilizes different technologies to measure liquid levels. A GWR level transmitter determines the liquid level in the tank by taking a time of flight measurement by sending a microwave signal and waiting for the return reflection from the liquid. The GWR has a rod or flexible cable that goes inside the tank and provides a guide on which the microwave signals can travel. An ultrasonic level transmitter is similar to GWR as it is a time of flight measurement, but it does not have a guide to direct the waves and it uses sound waves instead of microwaves to determine the level measurement. Both technologies need to be calibrated to the tank based on its size and product.
Magnetostrictive level transmitters use the time-based Magnetostrictive position sensing principle. Within the sensing element, a sonic strain pulse is induced in a specially designed waveguide by the momentary interaction of two magnetic fields. One field is generated by a permanent magnet sealed inside of a float while the other field is generated from an “interrogation” current pulse applied along the waveguide. The resulting strain pulse travels at ultrasonic speed along the waveguide and is detected at the head of the sensing element. The position of the magnet is determined by accurately measuring the elapsed time between the application of the interrogation pulse and the arrival of the resulting strain pulse. Magnetostrictive level transmitters are built to order and do not need to be calibrated in order to function in the tank.
Are Tank Modifications Necessary?
One of the first considerations engineers and site managers need to make when estimating installation costs is how much existing tanks will have to be modified. Most were not fabricated to accommodate the various gauges and other equipment required. While some tanks require no modification, others can require considerable alterations. The two factors that need to be considered are costs for new tank openings and the cost for stilling wells. These can vary significantly depending on the technology used and the preexisting nature of the tank.
Every additional opening cut into the tank increases the modification costs. Multiple openings are needed when a single gauge does not provide all of the necessary process variable measurements. Most tanks are looking for a measurement of product level, interface level and temperature to control the process. GWR and Ultrasonic level transmitters are only able to provide a level measurement and require separate devices to provide temperature. Magnetostrictive level transmitters provide a definite advantage in these applications because they incorporate a 5-IN-1 design, which allows for the measurement of product level, interface level and temperature to be measured from a single tank opening, but also gives volume measurement and an HI Level Switch as featured in the LevelLimit by MTS Sensors. The ability to provide automatic tank gauging and overfill protection from a single opening helps increase safety while minimizing expenses.
The second factor is the need for stilling wells. Depending on the details of the application, some level technologies can be installed without the need for a stilling well, allowing for lower installed costs. If available, all three level technologies should be installed in a slotted stilling well for the most accurate level measurement. In addition, stilling wells are typically required to allow the additional interface and temperature measurement instrumentation to perform correctly. This need is best determined by the manufacturer, who can easily tell you if a stilling well is required. For most applications, the Magnetostrictive level transmitter does not require a stilling well and helps minimize cost.
How Do Cabling and Conduit Affect Price?
Cabling and conduit needs differ significantly based on the level technology used and are not included in the standard cost of automatic tank gauges. To determine the costs of the cable, simply access the installation manual for the manufacturer’s cable specification. Some level transmitters require separate power and communication cables or specialty cables. A slight change in cable requirements can cause a significant change in price.
Wiring topology also affects the overall cost. Analog outputs require direct connection between the level transmitter and the host system, while bus networks wiring allows sharing cabling and reduces the amount of cable needed. Some level technologies require individual power cables but will share the communication cable. All of these options should be evaluated based on their cost as it relates to the level technology chosen.
The MTS LP-Series offers Modbus RTU output over a RS485 network. The cable can be shared with power and communication lines and have a bus topology to minimize the overall length of the cable run. The cable requirements are standard communication cable. All of this helps the LP-Series maintain an attractive installed cost.
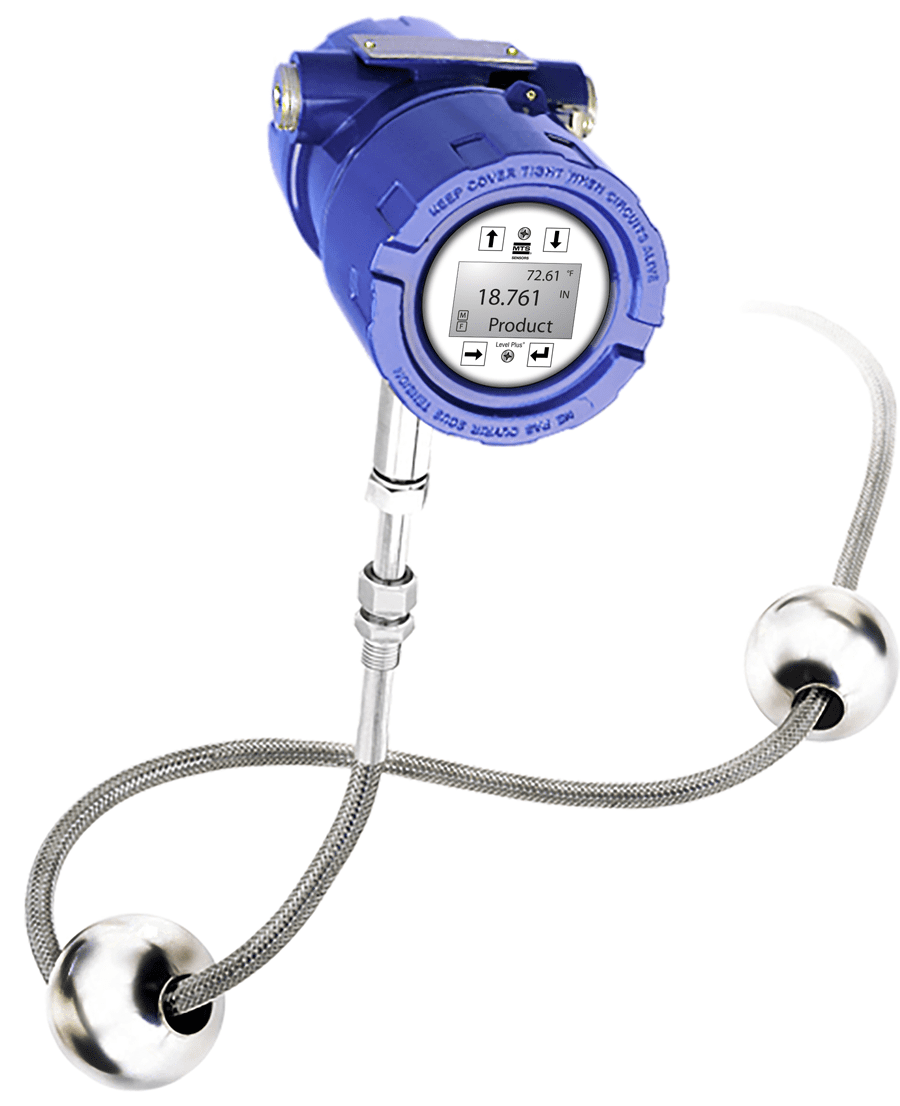
What Auxiliary Equipment is Needed?
The costs of auxiliary equipment can be determined through a site survey and an official quote from the manufacturer. Far too many site managers and engineers overlook this step only to find themselves with hefty costs related to auxiliary equipment later. A site survey will reduce the likelihood of surprises. Examples of auxiliary equipment are heaters for cold weather applications, protocol converters for proprietary protocols, specialty tools for service or installation, and licensed software.
The Magnetostrictive LP-Series from MTS does not need any auxiliary equipment to perform. The installed base covers the spectrum from warm tropical climates in Colombia to cold climates on the North Slope of Alaska. The LP-Series also features industry standard protocols of HART® and Modbus RTU that can connect directly to most controls systems. MTS provides free software for troubleshooting and commissioning is included in each shipment. There are no hidden costs for the LP-Series.
Making an Informed Decision
Installing an automatic tank gauge system can be more complex than it first seems. All factors, including tank modifications, cabling and auxiliary equipment must be considered in order to remain in budget. In most situations that require installing on existing tanks, Magnetostrictive level transmitters have the lowest installed cost over GWR and ultrasonic. The main difference is the 5-IN-1 measurement capability of the LevelLimit by MTS to measure the product level, interface level, temperature, volume, and a HI Level switch from a single tank opening. Operators who work closely with the manufacturer to understand what they need and how technologies differ will be better informed and able to make a decision that lowers costs without sacrificing the performance they need.
Headline photo courtesy of iStock
Lee Aiken is the Global Market Segment Leader, Liquid Level for MTS Sensors and an active member of API committees for Ch. 3.1b and Ch. 18.2. With over 12 years of experience with automatic tank gauging, he has been published in several magazines, hosted webinars, and taught at ISHM. Aiken has a Master’s of Business Administration (MBA) and a bachelor’s in electrical engineering from North Carolina State University.
Oil and gas operations are commonly found in remote locations far from company headquarters. Now, it's possible to monitor pump operations, collate and analyze seismic data, and track employees around the world from almost anywhere. Whether employees are in the office or in the field, the internet and related applications enable a greater multidirectional flow of information – and control – than ever before.