Gas monitor calibration remains an all too important and often insufficiently discussed topic in the oil and gas industry. All kinds of professionals use gas monitors to protect themselves from hazardous gases and other airborne substances that can lead to injury, illness or even death.
It’s important to remember that gas monitors and detectors are only as effective as the people using them. If you or a member of your team fails to properly calibrate and test your gas detection equipment, this could risk exposure to hazardous gases or an oxygen-deficient environment. Many gases can be difficult to detect, let alone judge exposure, without a properly calibrated gas monitor. Carbon monoxide, for example, is odorless, colorless, and tasteless. Using a digital gas monitor will provide you with a quick responding live readout.
I recently sat down with John Saechao, Gas Monitor & Warranty Expert at PK Safety, and asked him a few questions about this important topic.
What is calibration and why is it important to calibrate your gas detector?
Calibration tells you how accurate and reliable your gas monitor is by testing it with a known traceable concentration of gas. The procedure tests the sensors in your instrument to make sure they respond accurately and whether the alarms function properly.
The responsiveness of sensors varies depending on workplace environmental conditions, like temperature, humidity, and atmospheric pressure. Therefore, you should calibrate sensors in environmental conditions that are as close to (or similar to) the actual workplace conditions as possible.
During the calibration process, you will be using a type and concentration of calibration test gas, sample tubing, flow regulators, and calibration adapters. You will need to expose your gas monitor to the calibration gas, a small sample of the target gas. When you calibrate your monitor, it resets the instrument’s meters so that they match the test gas and ensures all readings are accurate.
Over time, all sensors will experience calibration drift. This occurs when an instrument’s reference point shifts, which also causes the reading to shift and no longer be reliable. Gas monitors experiencing calibration drift will still measure the quantity of gas present, but not convert it to an accurate numerical reading. This is why calibrating your monitors with a traceable gas concentration will verify or update the instrument’s reference point.
What’s the difference between bump tests and calibration?
There’s often some confusion when it comes to the ideas of bump testing and calibration.
Before the advent of modern day gas detection, coal miners made use of yellow canaries as a means to detect carbon monoxide. Unpleasant as it sounds, the miners would occasionally give the caged canary a quick jostle (bump, if you will) to confirm it was still alive and it was safe to continue. Thankfully we’ve come a long way since those days. A bump test today translates to a quick qualitative test that confirms that a monitor is functional and all alarms respond accordingly to target gas(es). Upon completion, the user is then confident its gas monitor will alarm audibly, flash visually, and vibrate accordingly at preset alarm levels. In other words, we’re giving the monitor a quick jostle (bump of gas) to confirm that it will perform as expected.
On the other hand, a calibration is a quantitative test that checks and adjusts sensor readings for accuracy against a known standard calibration gas. Sensor readings naturally drift due to environmental factors and normal everyday usage. If any deviations are found, the monitor will make any needed adjustments automatically during its calibration process.
When in doubt, always refer to the owner’s manual and manufacturer’s guidelines. Start with a bump test to make sure the device is working. If the bump test fails or your work environment is subject to change, proceed with a full calibration. Properly verifying the function and accuracy of your gas monitor before each use is critical to ensuring that workers are safe. Bump testing ensures proper function. Calibration ensures accuracy.
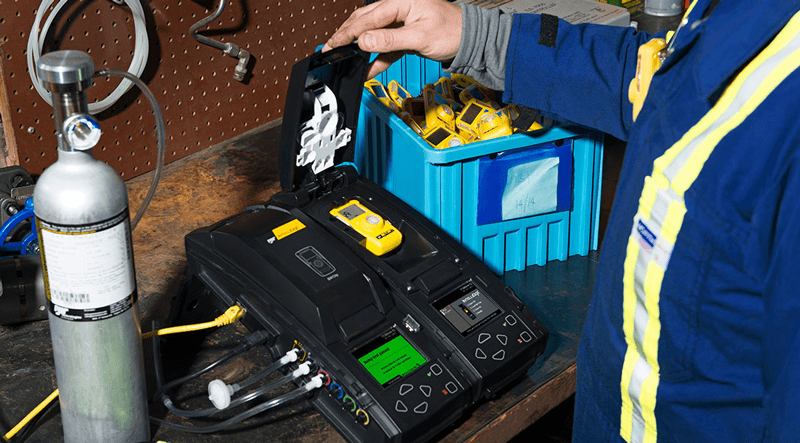
How do you bump test or calibrate a gas detector?
Please understand that bump test and calibration procedures (and apparatus) do vary from monitor to monitor and it’s a good idea to take a few minutes to review your user manual to familiarize yourself with its basic functions and features. Manufacturers use varying calibration gas and regulator flow rates that are not always compatible with one another. There are two methods available: manual (done by hand) or automatic (using a docking station).
To perform a manual bump test, begin by gathering the appropriate calibration gas bottle, regulator (valve for cal gas bottles), and provided testing cap. With the monitor on and in normal running status, apply test gas for about 10 – 20 seconds and observe that all alarms function and trigger at the appropriate level. It’s important to also take note of actual readings. The readings should be within a determined acceptable range of the test-gas concentration (typically ± 10-20 percent of the test-gas concentration). If it isn’t, proceed to a full calibration to readjust.
To manually calibrate your monitors, start by zeroing the meter, also known as a fresh air calibration. Some gas monitors may perform this automatically on startup. Your monitor would likely have a selectable mode for calibration. Using your calibration gas, regulator, and cal cap, apply gas when required. This process usually takes about two to three minutes and you’ll either be alerted when calibration has been completed, or you’ll manually end the calibration session. Any monitors failing calibration should be pulled aside and tagged. Contact the manufacturer for troubleshooting and assistance.
If your organization has a fleet of gas monitors, then utilizing an automatic calibration system will save time and reduce the chances of user errors. These docking stations can automatically bump test, calibrate, and provide all corresponding digital records.
How often does a gas detector need to be bump tested or calibrated?
It’s difficult to make one specific recommendation on bump test and calibration frequency. Most regulatory agencies defer to manufacturers for guidance on the matter. Even among manufacturers, there are ranges from 30 – 180-day calibration cycles. Bump testing is quick and easy and should be performed daily or just prior to usage. As for developing a tailored calibration cycle, consider starting at a more frequent rate than you normally would: once a week, if not more. Monitor for any changes (during your daily bump tests) to sensor response and confirm if any adjustments are needed. If you’re finding that little adjustment is needed, the sensor’s response is normal (within tolerance), and there are infrequent exposures or alarms, then gradually extend the frequency longer and longer. Ultimately it is up to the end users to determine an appropriate calibration frequency. The question should always be asked, “Are you confident with the instrument you’re using?” If there’s any uncertainty, test and calibrate accordingly.
How is calibration gas used and does it have a shelf life?
To calibrate your monitors, you’ll need to use calibration gas. These cylinders of various target gases contain information about the test gas, including its contents, so you can compare them to the meter readings to make sure they’re accurate.
Calibration gases do have a shelf life, so always check the expiration date of the gas before using it. Store your calibration gases away from sunlight in a dry, room temperature environment to keep them intact. You may need to recalibrate your monitors on the job, so make sure you have access to additional test gases throughout your shift.
Calibration gases can be either reactive or non-reactive. Reactive gases will change under certain conditions and may react to other materials, such as moisture, oxygen, or other chemicals. These usually last between eight and 12 months. Nonreactive gases will remain stable under changing conditions. These usually have a shelf life of up to three years.
Headline photo: John Saechao is a gas monitor & warranty expert who calibrates and services gas monitors in-house at PK Safety.
Rick Pedley, PK Safety’s President and CEO, joined the family business in 1979. PK Safety, a supplier of occupational safety and personal protective equipment, has been operating since 1947 and takes OSHA, ANSI, PPE, and CSA work safety equipment seriously. PK Safety's customer service can be reached at 800-829-9580 or online at https://www.pksafety.com/contact-us.
Oil and gas operations are commonly found in remote locations far from company headquarters. Now, it's possible to monitor pump operations, collate and analyze seismic data, and track employees around the world from almost anywhere. Whether employees are in the office or in the field, the internet and related applications enable a greater multidirectional flow of information – and control – than ever before.