Below is an interview with Arun Santhebennur. The interview text has been left intack, with only minor grammatical adjustments.
Tonae’ Hamilton: How/why was Petasense created and what is the overall goal of the company?
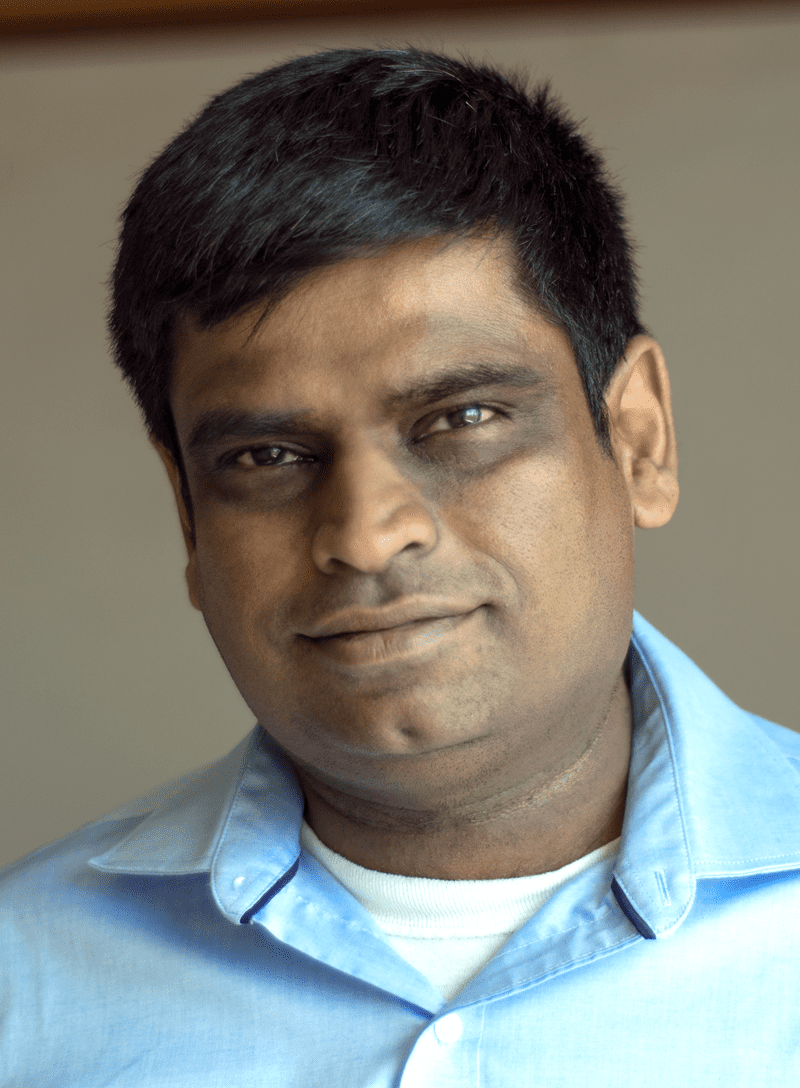
Arun Santhebennur: My cofounder, Abhinav Khushraj, and I saw that the next wave of connectivity was going to help “things” in the real world get connected after social media and the consumer internet got people connected. While we had both built our careers in building enterprise software products, we were really inspired by the simplicity and seamless user-experience that consumer IoT devices like the Nest thermostat and the Fitbit Smartwatch offered to end users. We were convinced that providing similar plug-n-play connectivity and analytics insight to industrial machinery was going to disrupt manufacturing. We launched Petasense in 2014 with the vision of becoming the “Fitbit” of industrial machines.
Taking the example of health, you can choose to only go to the doctor when you are really sick, or you can improve your health by continuously monitoring important parameters. In the industrial world, the same analogy can be applied – machinery can be operated until something fails, or you continuously monitor, predict, and prevent developing problems.
Our vision is to create a system for asset health that holds real-time information of equipment performance. The current practice of predictive maintenance is periodic, and information is siloed. We want to change that, making asset health transparent to everyone at the plant, across all assets. We also want to integrate process data with asset health and use that to better operate machinery on a day-to-day basis.
TH: Being an IoT startup that specializes in machine learning, in what ways do you hope to improve the energy industry?
AS: We want to see the energy industry achieve zero unplanned downtime and zero accidents. We also want these assets to operate in the most efficient manner possible. The energy industry has always been at the forefront of asset reliability, and we believe they will be leading other industrial companies with IIoT to have real-time visibility into the actual equipment condition.
Machine learning helps to sort through all the data. One of our customers in the energy industry collected 1.4 million data points in six months (compared with 5,000 using traditional walkaround techniques). It is not possible for a human to analyze all the data being generated from real-time wireless sensors. Our ML algorithms combine 40 different parameters to generate a single asset health score that can be trended over time.
Safety and reliability have always been two sides of the same coin. Having real-time information about asset condition helps to eliminate safety incidents. All personnel, whether technicians or managers can see what is going on with all equipment and get notification via text or app.
Another improvement area that we see for the energy industry is in energy efficiency. Valves and steam traps are important components in the energy industry, and as many as ⅓ of all steam traps have failed.
TH: What products are you most excited for customers to use?
AS: We are really excited about our Transmitter and Asset Reliability & Optimization (ARO) Cloud software.
The Transmitter provides a way for our customers to wirelessly bring in information from hundreds of different sensor types. With it, you can do multi-parametric monitoring, meaning that instead of looking only at vibration and temperature, you can incorporate parameters that show the actual operating condition, such as pressure, flow, current, and more. This helps to see the impact of operating conditions on equipment performance, and it means you will have better diagnostics because you are trending under similar process conditions.
ARO Cloud is our cloud-based software that collects, trends and analyzes multivariate sensor data alongside the asset that we monitor. We created the software with simplicity in mind. A plant manager or technician can easily understand overall plant. We have a visual dashboard where you can quickly see how equipment is performing, and an asset-centric “event feed” to share knowledge about assets. It also has all the sophisticated tools that a vibration analyst needs to diagnose the actual faults and make repair recommendation.
The product that most customers are really excited about is our Vibration Mote, which wirelessly collects vibration and temperature data. It is often one of the first applications that customers put in place when they are setting up their IIoT projects. They use it to monitor critical rotating machinery like motors, pumps, fans, compressors, etc.
TH: Can you describe how your software optimizes how machines operate? How does it affect oil and gas operations?
AS: In downstream, refineries are looking to improve overall operational reliability by deploying wireless sensors to monitor their balance of plant. Current scheduled routes cannot provide the consistent data collection necessary to detect trends as many machines may not be operational during the collection runs. Some defects occur too quickly to catch between routes and some are in locations that are difficult to access and are at risk for a safety incident.
In midstream, the compressor sites and gas facilities can be up to 50 miles from each other requiring long periods of travel. These sites are many times in remote locations where dangerous weather conditions exist like heavy snowfall. By remotely monitoring these sites, Petasense’s ARO Cloud machine learning can show the maintenance and reliability teams the health of these remote assets and identify the equipment that needs maintenance. This improves not only the overall reliability, but also the safety program.
TH: Are you currently developing any new products or software?
AS: We are continuously releasing new software features. This is the benefit of cloud-based systems; instead of waiting for one release per year, we can immediately address customer requests and deliver improvements. On average, we have a new release every month. We recently launched a smart measurement feature on the ARO Cloud software. With this feature, clients can set up a custom fine-grained schedule for each Vibration Mote to take measurements. This can help in scenarios where machinery is not running all the time. We are also soon launching a machine-learning driven bearing health score. This can give technicians (who are not vibration analysts) a quick guide as to when they can replace bearings proactively.
TH: What improvements would you like to see happen in the energy and chemical industries over the next five years?
AS: I think a big improvement will be moving from proof of concept to full implementation of their digitalization strategy. Many companies have been testing different technologies and starting small pilots, and within five years, I’d like digital technology to be ubiquitous.
I think there is also a cultural change happening. Younger workers are coming in, and acceptance of mobile, cloud, machine learning, and wireless sensing is increasing. Companies will see dramatic shifts in what is possible. But you can’t get there without the cultural change from the CEO all the way to the maintenance technician.
TH: Additionally, how prominent do you think ML (Machine Learning) will be in the oil and gas, power, and chemical industries over the next few years?
AS: Machine learning will be very prominent. Every conference you go to today has tracks on Maintenance 4.0, IIoT, AI, and similar topics. There is a huge interest, and many companies have started testing it out – 2018-19 are the years of proving the technology. Within 3-5 years, it will be proven and applied in new ways. ML for Predictive Maintenance is widely seen as one of the earliest applications, but there are so many other applications that we are seeing emerging.
I think in five years, people won’t even be calling it ML; it will just be a feature that enables the workflows within industry. Just as we don’t refer to Siri as AI, but as a digital assistant that helps get things done. In the industrial world, people will rely on ML as an enabling technology rather than separate.
Tonae’ Hamilton has been a contributor and associate editor to the magazine for two years. She has been writing professionally for almost four years. In her free time, Tonae’ likes to spend time with her three pets, cook, and binge-watch Netflix shows. Tonae' has a Bachelor of Arts in Communication from McDaniel College.
Oil and gas operations are commonly found in remote locations far from company headquarters. Now, it's possible to monitor pump operations, collate and analyze seismic data, and track employees around the world from almost anywhere. Whether employees are in the office or in the field, the internet and related applications enable a greater multidirectional flow of information – and control – than ever before.