Eric Eissler: My grandfather used to tell me that there is nothing more constant in life than change. He is right and, for many, change is a hard thing to deal with. With all the automation going on, how are you helping companies adapt to change?
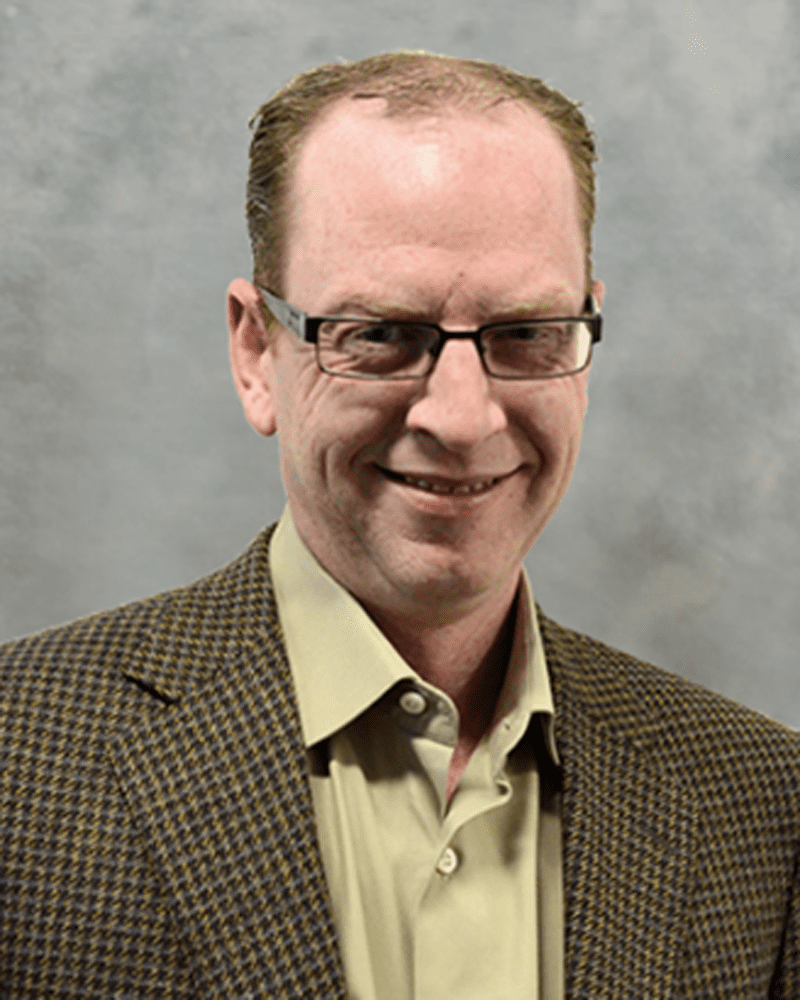
Ryan Lailey: At WolfePak, we speak daily with independent oil and gas companies about digital transformation and automation. Discussions may include how to get started with an electronic process, what should be taken into account when digitizing workflows, and ways to ensure frictionless data transfer and integration with operations.
WolfePak conducted a survey in April to learn about what challenges our customers were facing with practically an overnight transition to remote work. Their biggest hurdle was working with paper-based processes. Many organizations are looking for ways to manage their operations, customers, employees and partners while working from home. Couple these challenges with the market volatility, and you have companies that need to automate functions to do more with less, lower general and administrative costs, and reduce their reliance on paper-based processes.
The oil and gas industry is primed for this innovation and the events of 2020 gave the transition a “jump-start,” if you will. In an industry where even the smallest and least significant transactions may require complex interactions with owners, stakeholders, oilfield teams and more, along with the need to make smarter and faster decisions, now is the time for companies to automate.
To survive market conditions and our industry’s evolution, we must adopt new practices and excel in a modern workplace. Independent companies can gain several benefits by leveraging new automation technologies. It lets them become more agile and gain a competitive edge – all securely and cost-effectively.
EE: Automation usually spells layoffs for many. Have you been seeing layoffs or are employees being re-trained to do other, more technical jobs?
RL: Cost-cutting initiatives are just not enough. Automation eliminates manual tasks, enabling teams to do more with less, and focus on higher priority work.
When implementing a digital transformation strategy, you not only need to deploy new technologies, your team needs to learn new skills and expertise. That makes re-skilling and training the current workforce all the more critical. To complete a successful digital transformation, companies must embrace the right technologies and invest in personnel to learn modern approaches.
A recent report by Ernst & Young showed that nearly 60 percent of today’s oil and gas workforce needs re-skilling for their companies to remain competitive. Still, only 43 percent of them will receive the training they need, which averages about ten months to complete. Re-skilling employees can be challenging, but it’s not impossible. Companies are augmenting the skills gaps by leveraging automation technology, with more than 51 percent of respondents already in implementation mode and another 40 percent planning to do so.
It’s not just individual companies that need to change. Our industry’s reliance on paper-based processes for the back-office is well past their expiration date. The most significant opportunity for the industry is to collaborate and digitize the entire ecosystem.
EE: What are the most essential concepts for management and operations teams to learn and promote while undergoing these changes?
RL: Transformation definitely must start at the top. Leadership sets the vision. Communication is key. Start by giving employees an overview of how the digitized company will run and how it will affect success. Assure them that it will make everyone’s job more manageable and show them how. If they can replace rummaging through a file cabinet looking for one piece of paper with a simple Google-like search for the same document, they will appreciate that. Employees will feel encouraged to rally around this effort to make the organization more efficient by saving time, resources and money. This makes the learning curve worth it.
Depending upon their size, companies may house tens or hundreds of thousands of documents with complex workflows. They will get overwhelmed if they try to digitize everything at once. We recommend a “point forward” process, meaning the company sets a date to go digital and stop the influx of paper as it moves its procedures online. Then companies can determine what the next priority is and continue their journey from there.
Additionally, companies need to evaluate how their current software infrastructures are best supporting them. It’s not enough to just cut costs. Companies have to change how they operate in order to thrive today. Ensuring that all of your company’s software meets your best-fit requirements is tantamount to success. We advise companies not to fall into the “sunk cost” fallacy and continue to invest in systems that aren’t agile enough to maneuver in today’s climate.
EE: What kind of automation are you seeing the most in your experience?
RL: The current pandemic has shed a harsh light on the old-fashioned financial processes hindering oil and gas operators and production. The production side has always been quick to implement the latest technologies. Still, investments for the back office have not kept pace, so accounting teams, among others, have had to rely primarily on paper-based systems and spreadsheets.
Huge file rooms of documents and paper-based information are quickly becoming a thing of the past with more and more people having to work from home. WolfePak’s Document Management solution helps our customers with digital transformation by automating workflows to the back office. Since people aren’t going into the office to pull a file or approve an invoice, digitizing documents is crucial for maintaining business continuity.
With WolfePak’s document management, employees working remotely can log in from any computer with an Internet connection and gain instant access to the information they need to do their jobs. For accounting pros, if you haven’t made your workflows electronic, something as simple as asking many people to sign off or approve invoices is difficult and inefficient. With the integration of DocVue into WolfePak, customers can automate this entire process.
When they do return to the office, [employees] will be more efficient in this environment, reducing their reliance on huge file rooms of documents and paper-based information. It’s a win-win situation.
EE: Why WolfePak? What sets you apart from the competition?
RL: WolfePak’s customers are active in our strategic roadmap planning and are the lifeblood of our organization. Every company is unique, and it is our entire team’s mission to collaborate with them to learn how best to provide support today and in the future.
WolfePak Software has been providing software for independent oil and gas companies for the past 30 years. Our mission is to put technology, once reserved for the biggest oil and gas companies, into the hands of independents to enable automation. Automation will be the key to optimizing costs and getting the visibility companies need to make better decisions.
Our goal is to automate as much of the work as possible, providing solutions for oil and gas accounting, oilfield data collection, document management and inter-company business transactions. Our customers trust us because we provide information that helps them make better business decisions to deal with today’s volatile market conditions.
Today, virtually any company can automate its operations. Doing it correctly requires forethought and planning. It’s not just about data collection and transfer. It’s about data insights and letting the data tell you what to do next. In short, the only way that companies can survive in what is now a depressed market is to automate and streamline everything they can.
EE: While we have seen ups and downs in the past, it appears the COVID-19 pandemic will have lasting effects on how we live our lives and do business. Some of these effects, such as working from home, will have major impacts on cities and transportation. Given that transportation demand will shrink, and electric vehicles are on the rise, which market do you see oil and gas consumption shifting to?
RL: COVID-19 has indeed changed the way we live and work, perhaps forever. What happens next is still up for debate. But it doesn’t mean the end of the office as we know it. Don’t forget that essential workers, of which there are so many within oil and gas, never left the office. That said, companies need to do everything they can to make data access, transfer and integration as easy as possible to manage for their teams, whether they are remote or not.
Many work processes will never come back. No one wants to push paper or drive to the office to get a file when they can access it online from wherever they are. But not all manual work disappears; the approach just changes.
And while the electric movement is exciting, it doesn’t signal the end of oil and gas as an industry. We forget that there are so many other things that rely on oil and gas to run – trucks, boats, barges, even irrigation systems on farms.
EE: Under the Biden administration, how do you see oil and gas faring? Do you believe there will be a lot more regulations set forth?
RL: We work in a highly regulated industry already. Our job at WolfePak is to help our customers maneuver through any market or political climate with ease. Oil prices going negative is something no one thought would ever be possible. This year is a perfect example of our industry’s resiliency and adaptability – we’ll get through this together.
Our primary focus is on taking care of our customers. We’re doing everything we can to help them adjust to the “new normal” of business, whether that’s getting online remotely, implementing new cloud and mobile technologies, or creating new business rules in our software to account for so many of this year’s industry firsts.
We work with our clients to navigate their specific market requirements, understand what insights they can glean, and what new reporting needs they may have. And we aim to provide our customers with access to the right information when they need it, in as few steps as possible.
EE: Technology and the oil and gas industry have come a long way. What are your predictions for the next step in this relationship?
RL: Technology is an enabler to a more profitable path. As I mentioned before, we will continue to work with our customers and partners to ensure we deliver solutions that efficiently help them reach their business goals.
Cloud adoption has rapidly increased in the wake of COVID-19. Customers understand the benefits of cloud economics and want the ability to scale as needed.
In addition to more cloud and mobile deployments with the back office, we’ll see more data analytics and business intelligence (BI). Companies are sitting on mountains of data, but need help in gaining actionable insights from the information.
Eissler, former editor-in- chief of Oil & Gas Engineering magazine, previously worked as an editor for Dubai-based The Oil & Gas Year Magazine.
Oil and gas operations are commonly found in remote locations far from company headquarters. Now, it's possible to monitor pump operations, collate and analyze seismic data, and track employees around the world from almost anywhere. Whether employees are in the office or in the field, the internet and related applications enable a greater multidirectional flow of information – and control – than ever before.