It is well known that in the oil industry the production of hydrocarbons in many cases leads to the production of unwanted fluids, generally water. It is also known that the barrels of water production by oil production are too high worldwide. So it is important to know at what time this water production is presented, under which schemes, what are the control mechanisms that have been raised in general, and the recommendation of having a structural geological model as the best control element for the future decision-making in the management of water production control.
The production of water in producing wells constitutes a limiting factor that controls its productive life. This excessive production of water causes various problems both at the well level (corrosion in casing, grooved pipe or prepackaged grids), and at surface level (formation of scales, hydrates and emulsions in flow lines and tank yards), which reduces the profitability and productivity of wells, since costs per barrel of oil are increased for maintenance and chemical treatments; therefore, the analysis of all the characteristic aspects of the well and the reservoir is always required, in order to improve their profitability and productivity.
The water control management consists of having knowledge of the structural geological model of the reservoirs, petrophysical properties, pressure levels, production behaviors and records, types of mechanical completion and intervals completed, particular conditions of each producing well or injector. Establish diagnoses that allow determining areas invaded by water and thus optimize the production of active wells, recommending useful water control techniques when carrying out future rehabilitation works and new well locations.
Water control technology is an activity that consists of improving the injection or production profiles of a well, minimizing the effects of coning and/or channeling of fluids to improve recovery efficiency. In order to reduce water cut and increase the useful life of the well, various techniques and alternatives are used, among which include Production Log (PLT), Cementation Logs (CBL, VDL, GR), Water Flow Log, and diagnostic curves (Chang Charts).
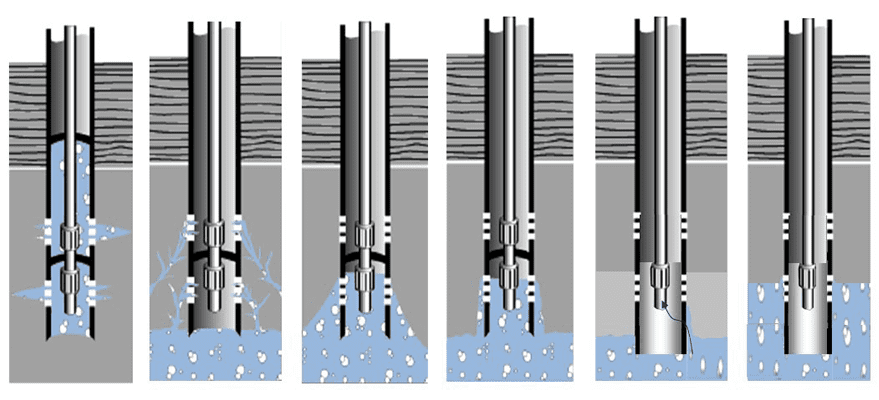
Types and Solutions of Problems for Water Control
Some specific types of problems associated with water are shown by degree of complexity. High water cut can be the result of one or more problems. The following are the most common types of problems in a well:
- Leak in production line, casing line or packer. Production records, such as temperature and injection records, may be sufficient to diagnose these problems. Solutions typically include forced injection of isolation fluids and mechanical isolation.
- Flow behind the casing, failure of primary cementing, or the creation of interstitial space due to sand production can cause water to flow behind the casing in the annular space. Isolation fluids can provide a solution.
- Upwardly displaced water/oil contact (WOC). This phenomenon is usually associated with the presence of limited vertical permeability, generally less than one MD. With higher vertical permeabilities, the coning phenomenon is more likely. In vertical wells, the problem can be solved by mechanically insulating the bottom of the well.
- High permeability layer without cross flow. The presence of a shale barrier above and below the producing layer is usually the cause of this condition. The absence of cross flow facilitates the resolution of this problem by applying rigid insulation fluids or mechanical insulation either in the injector well or in the producer well.
- Cracks between the injector well and the producing well. In naturally fissured formations, water can quickly enter production wells. Applying an insulating fluid to the water injector well can be effective without adversely affecting cracks that contribute to oil production.
- Fissures or fractures and an underlying water layer (2D coning). Water is produced from an underlying water area through natural fissures. The application of isolation fluids can be effective for this problem.
- Conical or cusp formation. The production carries water upwards toward the well. A gel coat placed above the cone can be effective in slowing down the coning process. A new side well can also be drilled near the top of the formation, increasing the distance from oil/water contact and reducing pressure drop, both of which reduce the coning effect.
- Poor areal sweep. This problem is usually associated with heterogeneity of poor areal permeability or anisotropy. It is particularly severe in environments with sand channels. One solution is to divert the injected water out of the already swept pore space or access the unswept oil by adding lateral drainage sections to existing wells or by drilling fill holes.
- Gravity segregated layer. In powerful prospective layers, with good vertical permeability, the water, coming from an aquifer or from a water injection project, is segregated by gravity and sweeps only the lower part of the formation. Isolation of bottom shots in injection or production wells often only has marginal effects; ultimately, gravity segregation predominates. Drilling additional side drainage wells may be effective in accessing the unswept oil. Energized viscous flood fluids, gas injection, or alternate use of both techniques can also improve vertical sweep efficiency.
- High permeability layer with cross flow. Unlike the case without cross flow (4), the presence of cross flow prevents the implementation of solutions that modify the production or injection profiles only in the area near the well. The use of deep penetration gel can provide a partial solution.
Diagnostic Techniques for Water Control
In general, when a sudden inrush of water is observed in the producing wells, it is most likely due to the presence of fractures or well-level problems such as leaks or channels behind the casing.
To discern if the problem is generated in the vicinity of the well, the most commonly used tools are the cementing logs (CBL / VDL). These records identify the areas where the cement has had poor adhesion with the formation and the casing and can be accompanied with records of fluid movements along the well (spectral or water flow log) or ultrasound records to inspect the integrity of the casing.
When these problems are ruled out, the presence of fractures should be considered, which can be confirmed by reviewing the history of the stimulations carried out on the well, the geomechanics of the reservoir, pressure tests, temperature records or the use of tracers.
When there is a late irruption of water or gas, the most common reason is due to highly permeable matrix channels or conification problems due to the presence of aquifers. In this case, it is important to have production and injection records that allow identifying where the fluid comes from. Additionally, Chang’s diagnostic curves can be used to discern between both problems.
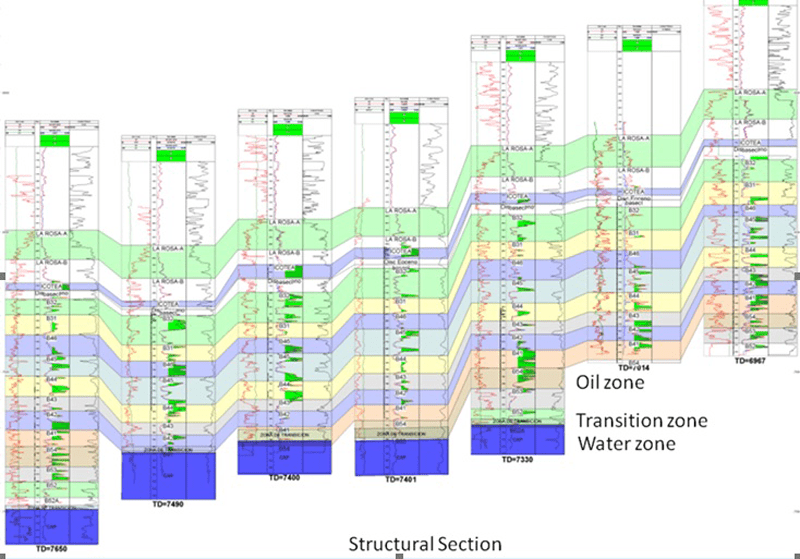
Importance of the Structural Geological Context in the Management of Water Production Control
In this order of ideas according to Bailey, B (2000), in the past, it was considered that the control of water was nothing more than the simple placement of a plug accompanied by a cementing operation, or a gel treatment in a well. The reason the oil industry could not achieve an adequate method to control water has been its lack of knowledge of the different problems and the consequent application of inappropriate solutions. The key factor is the diagnosis; that is, being able to identify the specific problem that arises.
Well diagnostics are used in three ways:
- To select wells that may need a water control system.
- To determine the water problem so that a suitable control method can be selected.
- To locate the point of entry of the water in the well in such a way that the treatment can be placed in the correct location.
Knowledge of the structural geological context in which the deposits are developed is of vital importance when selecting the different control mechanisms, both mechanical and chemical. In many cases, only with the establishment of a good structural geological model and knowing the distribution of the fluids, they already represent a solution by establishing the best production methods, avoiding the stimulation of production in the transition areas and areas below water/oil contact.
Mechanical methods represent the best alternative when it comes to evading fractures or communications through the casing, as well as chemical methods, which will represent the option when it comes to inhibiting areas of high permeability or trying to keep the water-oil ratio in balance. In any case, truly knowing the framework in which water production takes place is the best alternative in water control management.
Sources:
Craf, B.C y Hawkins, M.F. “Applied Engineering of Oilfields.” Editorial tenos. Madrid, 1977.
Sánchez, E. Geological model to determine early inrush of water Campo URD 01, Universidad de los Andes, Mérida, Venezuela, 2006.
Shulumberger “Wec. Well Evaluation.” Schlumberger Surenco. Caracas, Venezuela, 1997.
Vargas,J and col. Early water eruption in the wells of Block I, URD 01 field. Universidad del Zulia, Maracaibo, Venezuela, 2006.
Ender Sánchez has almost 12 years of experience in the oil and gas industry which include reservoir management, well productivity, petroleum geology, geomechanics characterization, stratigraphical characterization, integrated studies, new well location strategies, geomodeling. He holds a bachelor’s degree in Geology Engineering and a specialization degree in Petroleum Geology. His areas of expertise include technical support in borehole-stability problems during drilling and production to different completion schemes, pore pressure prediction, rock mass, and rock stress estimation, estimate mud safe window and the best direction to drill horizontal wells. In addition to this, he has been in charge of reservoir and production well surveillance that include generation of recommendations to drill new wells, geological models to oil reserves characterization. He has conducted numerous short courses in Geomechanics for Universities and the Oil & Gas Industry. Over the last few years, he has applied his expertise to the real-time wellbore stability monitoring and mechanical earth model estimation for Petroleos de Venezuela Company.
Oil and gas operations are commonly found in remote locations far from company headquarters. Now, it's possible to monitor pump operations, collate and analyze seismic data, and track employees around the world from almost anywhere. Whether employees are in the office or in the field, the internet and related applications enable a greater multidirectional flow of information – and control – than ever before.