For the oil industry, efficiently finding and developing hydrocarbon resources is essential. In the ongoing search for new energy reserves, seismic data acquisition has emerged as one of the petroleum industry’s most reliable and commonly used technologies for finding subsurface oil and gas deposits. And the need for accurate and cost-effective seismic data acquisition technology continues to grow.
GeoSpace Technologies, headquartered in Houston, Texas, has been developing innovative products for the petroleum industry since 1980, including geophones, printheads, and land-to-deep sea systems for seismic data acquisition. With GeoSpace’s seismic instruments and equipment, geoscientists use sound to search for oil and gas, collecting seismic data that can then create images of the earth’s subsurface, revealing potential or existing oil- and gas-bearing formations.
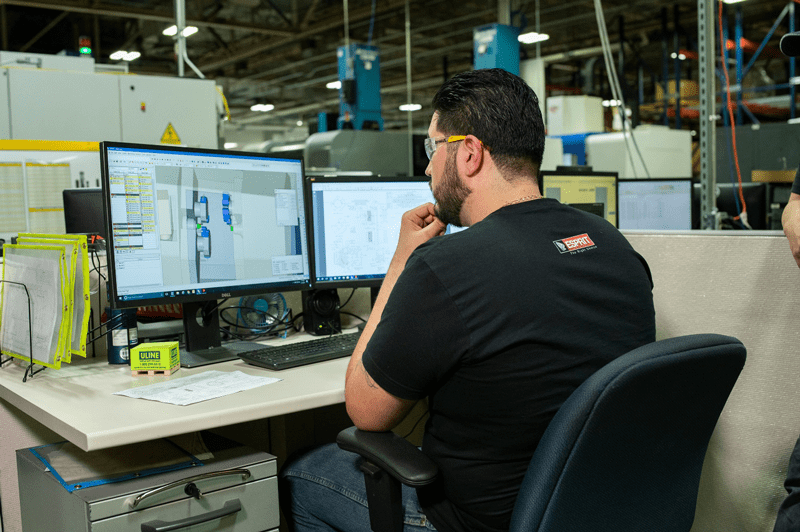
Geoscientists have come to rely on GeoSpace’s products to keep that valuable seismic data flowing – and to do so in newer and better ways. Efficiency and reliability are the twin keys to success, for both GeoSpace Technologies and the petroleum companies that rely on its products.
Keeping tight delivery schedules is another critical factor in this industry. The costs associated with a late delivery can be substantial. For example, it might cost a company up to $300 thousand a day to charter a large ship for a geological survey. Forcing that ship to sit at the dock waiting for equipment to be delivered is not acceptable.
Given these constraints, it can be risky to rely on external manufacturing suppliers—especially overseas suppliers—that have their own priorities and can’t always be relied on to meet delivery schedules. GeoSpace has overcome this challenge by manufacturing the majority of its products and their components in-house. The company has more than 200 manufacturing employees who make machined metal and plastic components, build molds, perform injection molding, build printed circuit boards, and perform other essential manufacturing operations.
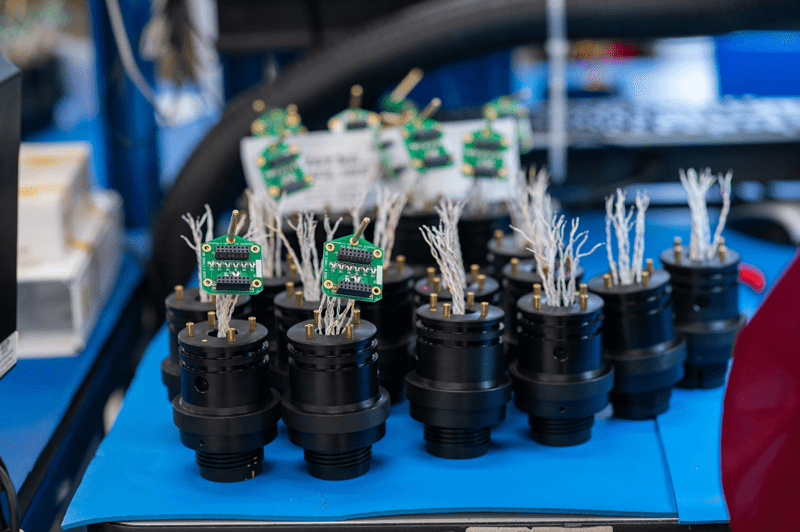
GeoSpace’s production equipment includes 33 CNC machine tools and a number of manual machines and auxiliary equipment. This has recently been augmented by newer, more advanced machinery, including a Citizen Miyano Machinery ABX-51TH3, which has an upper turret on the left side, another on the right side, and a lower turret capable of working on both sides.
Initially, the manufacturing engineers at GeoSpace Technologies programmed the machine with the CAM (Computer-aided Manufacturing) software they had been using for years. However, they ran into difficulties while trying to make full use of the machine’s capabilities. For example, achieving complete use of the machine’s three turrets was hindered by the fact that just moving an operation from one turret to another often required starting the program from scratch.
Justin Henry, manufacturing manager for GeoSpace Technologies, was assigned the task of improving the efficiency of its manufacturing options. Upgrading the company’s CAM software was his top priority and increasing efficiency with multitasking machinings, like mill-turn and Swiss-type turning, was essential. Henry evaluated a number of CAM companies and systems and selected ESPRIT from DP Technology “because it provides the best support I have seen for advanced machines.”
ESPRIT reseller, Victor Davila of Shape Design in Houston, was brought in to assist and showed GeoSpace what it could achieve with the CAM software, which offers factory-certified post processors delivering machine-optimized, edit-free G-code. “I told them they could write code and take it to the machine and run good parts the first time,” says Davila.
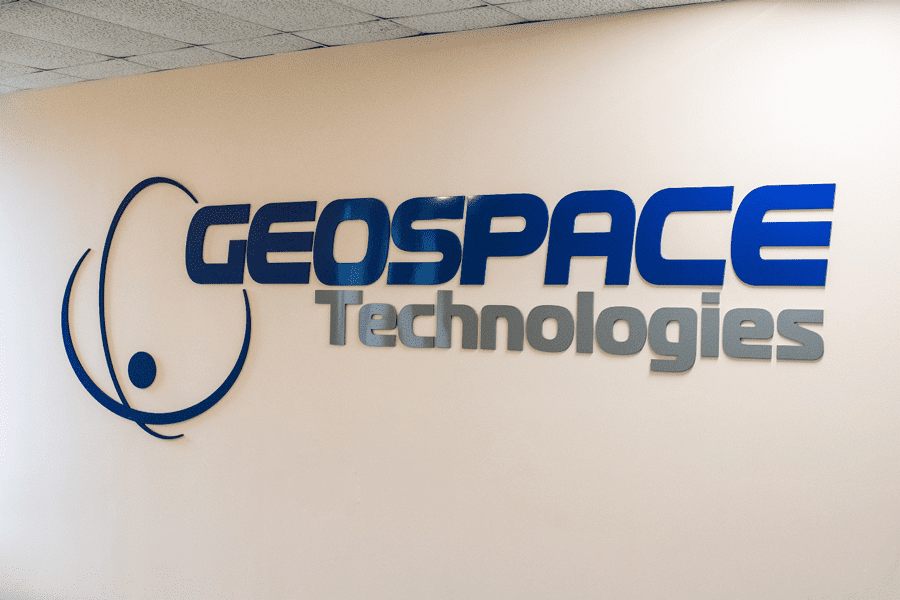
After training on the new software, Henry concentrated on improving the program to produce an “end bell,” a part for the company’s OBX product. During seismic mapping, this part protects electronic components from the intense deep-water pressure on the ocean floor with the use of six O-ring seals. GeoSpace produces nearly 50,000 end bells every year, machining them from plastic as they are too complex to be injection molded.
The GeoSpace Technologies’ programmer began by opening the Solidworks solid model of the part in the CAM software and used the software’s automatic feature recognition component to identify the machining operations necessary to produce it.
“We decided to flip the part around front to back in the machine because it is easier to deploy two spindles on the front side of the part, which also has most machining operations,” says Henry. The programmer then assigned machining operations in order to maximize turret utilization. For example, originally, two radial drilled and tapped holes were produced one after another by a single turret. Using the new software system, they are now machined simultaneously on the front side of the machine by two synched turrets.
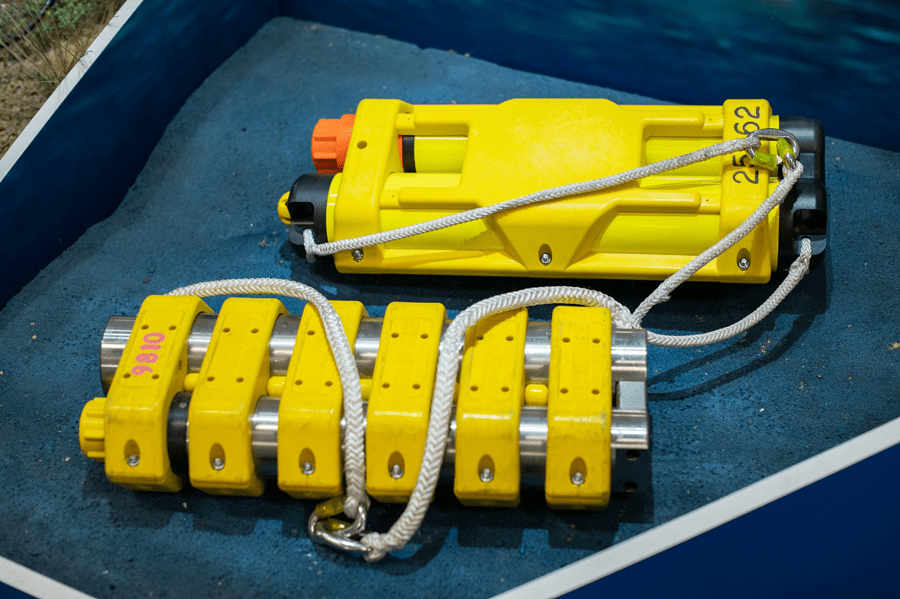
Previously, an axial through-hole with several steps was drilled and bored using four different tools. The programmer changed this. Now, after the hole is drilled, a single carbide insert tool is held in the positions to bore all the steps while the part rotates. This new method shortens the cycle time considerably by reducing the number of tool changes.
Cutting speeds and feeds were also adjusted to take full advantage of the tooling’s capabilities. After testing the new speeds and feeds on the machine, and tweaking where necessary, the final parameters were transferred into the final CNC program.
The new program greatly reduced the cycle time—from 22 minutes to 6.5 minutes—for producing the part on the ABX machine, saving the company significant time and money. The programmers then followed up on this success by using the CAM software to reprogram a variety of additional parts for the ABX machine, achieving still greater savings.
The time savings also came from the ability to do time studies within the software. Knowing that a tool actually takes, say, two minutes to run instead of 10 allows for more accurate job planning and cost reporting. With the previous software, it wasn’t possible to get an accurate idea of run times until the part was test run on the machine. That has changed; now the new software provides GeoSpace with a report that shows how long the tool will be in the cut.

The software’s ability to simulate machining operations also allows GeoSpace engineers to accurately visualize how a program will run when creating or modifying a new tool. Being able to check the machining—virtually—before actual production begins helps ensure optimal programming and avoid machine-tool crashes. With the new software, avoiding collisions and syncing between turrets can all be simulated in real time with a click of a button. This is in contrast to other systems, where the syncs don’t always match what you see in the machine and time and materials must be wasted proving out the program on the machine tool.
According to Henry, the new software made it possible to move operations from turret to turret or set sync points with a few clicks of the mouse. Now, with more accurate syncs possible, even greater efficiencies could be found.
When you’re programming and process planning, control is everything. Among the reasons that GeoSpace selected the new software for its machinery is the power and control that it provides. With the new system, programmers have control over the tool to do whatever they want to do. The software is completely customizable to meet the unique and changing needs of the manufacturers and machine tool builders who use it.
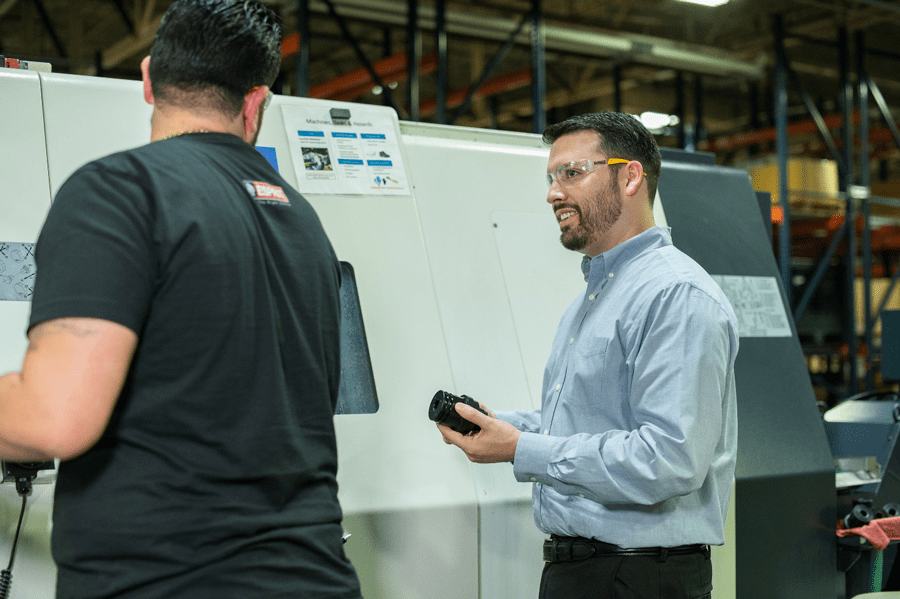
Implementing the new full-spectrum CAM system for CNC programming, optimization, and simulation, one that supports the entire manufacturing process from CAD file to machined part, has helped increase production efficiency at GeoSpace Technologies. Cycle times have been reduced, production rates have risen, and the company is able to rapidly adapt and improve its CNC programs for multitasking machines.
“We have achieved substantial savings by combining processes into a leaner approach, dividing operations to more efficiently utilize all machine spindles and turrets, reduce the number of tool changes required, and make many other improvements,” concludes Henry.
With its CAM software and world-class technical support in place, GeoSpace Technologies is set to continue to develop value-driven, innovative and effective seismic data acquisition products and services for its clients.
A video interview with Justin Henry discussing GeoSpace Technologies’ products, machining operations, and new CAM software:
Jerry Fireman is a technology writer who specializes in writing about computer-aided design and computer-aided manufacturing (CAD/CAM), 3D printing, the Internet of Things (IoT), and a variety of other topics. To date, he has written more than 10,000 articles that have been published in over 3,000 trade journals, technical journals and mass media around the world.