Oil and gas producers may not have control over the direction of their commodity prices, but lifting cost is a lever that can be applied to lower breakeven and improve profitability. One area that may not immediately come to mind to reduce lifting cost is the expense associated with safely disposing of produced water. Permian operators face increasing water production in the Midland Basin – as much as seven barrels per barrel of oil produced – and 10 barrels in the Delaware Basin. Produced water transportation is arguably a bigger business in many basins than moving crude oil. The hauling costs come back to an operator’s balance sheet adding something north of $3 to a barrel of oil’s lifting cost in the Midland Basin. Boom or bust, oil producers are sure to take a five percent or more boost to their cash flow any day. New technology is enabling a step change in how efficiently produced water is moved, which in turn is lowering the cost of doing business for haulers, translating to lower lifting cost, and enabling producers to get out of the transportation management business.
A 30 cent per barrel reduction in water disposal, is a $3.00 per barrel lifting cost savings on a 10 to one cut. The dollar cost savings are significant, but the ESG impact can be even greater. Technology brings better data, and better data leads to better, more efficient planning and field operations. That’s good for haulers and good for the environment.
The energy industry has always pulled more out of the ground than oil, gas and natural gas liquids. There are often other commodities that can be sold or must be disposed of, including sulfur, CO2, and even lithium, that are now being extracted from a well’s petroleum brine. This puts energy companies in the business of tracking multiple streams of molecules produced at the wellhead. Those who do it well can dramatically reduce costs while gaining a deeper view into where, when and how commodities are flowing through the energy value chain.
Following the Physical and Accounting Movement of Commodities
Energy companies assume responsibility for every molecule they produce and moving each commodity along the value chain is a risk they carefully manage. In some parts of the Midland Basin, that means seven to 10 water trucks are needed for every oil hauler (if you’re 100 percent efficient). That’s a lot of traffic on West Texas roads and even where there is access to water pipelines, chances are trucks are moving it to the terminal. The ability to monitor driver and carrier safety is critical to managing risk.
For many producers, water management is its own department with a head count that includes dispatchers, back-office and technology costs for field operations. A lot of paper tickets are generated as a result, requiring the necessary accounting staff to process thousands or even tens of thousands of invoices per month from haulers. Field operations and accounts payable also have to manage relationships with dozens or more haulers, requiring bandwidth and patience.
Everyone has a stake in the game. Cost effectively moving a barrel of water and knowing where it is at all times enables producers to optimize production expenses and gain transparency into its disposition while enabling haulers to be more proactive, avoid deadhead runs and demurrage, and compete on price. Technology also enables carriers to run more efficiently while being more environmentally responsible.
Adding complexity, how produced water ends up at a disposal well or treatment facility often requires more than trucks. Across the country, a single molecule of oil, gas, NGLs or water is increasingly transported in multiple modes or intermodality. As such, once a molecule leaves the wellhead, stakeholders in the value chain must follow it across a mix of trucks, pipelines, railcars, ships, barges and vessels. Tracking even a single molecule through intermodal transportation is complex enough, so just imagine what it takes to see where the production stream is at any given moment, and effectively reduce or eliminate demurrage. Transportation management is critical in the digital oil field.
Just ten years ago, managing the physical and accounting movement of water and other commodities was almost entirely paper-based – paper run tickets left in Mason jars, grease sheets for pumpers, physical invoices sent by haulers. Producers and carriers have mostly gone digital, even if they still exchange physical run tickets in the field. Supporting hauling operations these days requires a raft of software and back-office capabilities, including inventory management, scheduling, invoicing, accounts payable, payroll and compliance. The persistent problem for most companies is that all of this – paper field tickets, back-office software and the G&A to manage it all – is expensive, resource intensive and, at the end of the day, only provides a static view of where a commodity is in the supply chain.
Three major waves of innovation have intersected to enable a paradigm shift in how stakeholders up and down the value chain move and track commodities. The first is the Cloud. With on-demand access from anywhere and automatic provisioning of storage and compute power, the Cloud created a Cambrian explosion of innovation and new opportunities to build software as a service (SaaS), avoiding the limitations and costs of traditional on-premise software.
Secondly, mobile devices have brought real-time data access and acquisition into the oil field. The smart phones that field staff now carry in their pockets, and the tablets sitting in the truck, introduced exciting new opportunities to support lease assessments, the hauling process and tracking the molecule. This includes collection of key metadata for every molecule such as volume, gravity, BS&W draw and tank strapping. But these devices also carry real-time GPS, accelerometers, thermometers and cameras. The upshot is that a producer can now accept its run tickets digitally, then follow a water haul in real time to the end of its journey with a photo to mark each milestone.
And finally, 5G brings data access to even the most remote of locations. It allows images to be transferred in real time and allows a large pipeline of data to be used for optimization of the whole supply chain.
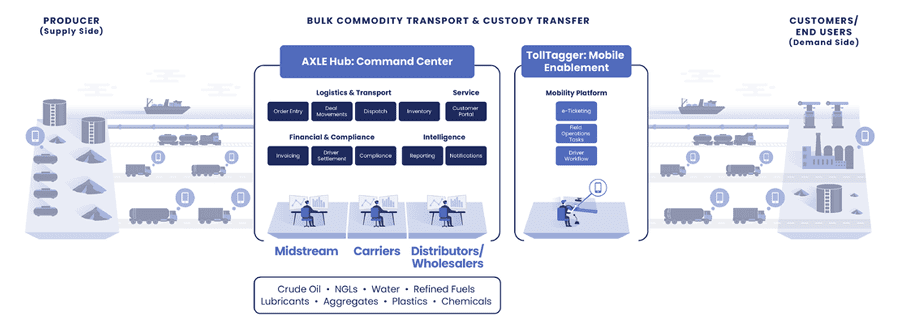
Transportation management has advanced further with innovators like Chorus Logistics, a W Energy Software company, that is executing on a roadmap to provide upstream and midstream companies with complete visibility into every molecule of production passing through the energy value chain. Its transportation management solution consists of a SaaS product called AXLE Hub, which provides back-office management tools for inventory management, intermodal scheduling, invoicing, payroll and regulatory reporting.
Connecting the field to the back-office application is TollTagger, a mobile app designed for Apple and Android devices, that continuously synchronizes driver location, speed and status with the Cloud. It leverages artificial intelligence algorithms to enable adaptive routing similar to logistics systems used by UPS and FedEx. As a result, commodities are automatically routed along the most efficient path from wellsite to the final destination and points in between. Importantly, AXLE Hub and TollTagger combine to create a two-way network that automatically links producers with their carriers to optimize logistics in real time and simplify transactions.
The Opportunity for Upstream and Midstream
AXLE Hub and TollTagger lower the barrier for new water haulers to get into the business. The transportation management solution effectively delivers a complete back-office for new and existing haulers, enabling the former to immediately start moving water and the latter to dramatically reduce G&A and technology costs.
Moving produced water, or any oilfield produced commodity, must be a well-choreographed dance to ensure trucks are constantly moving, not waiting in line with engines idling, and not burning deadhead miles (driving long distances with empty tanks). TollTagger choreographs this dance for the hauler, rerouting them if trucks are waiting in line at one location and providing turn-by-turn guidance that ensures they are always taking the most cost-effective routes.
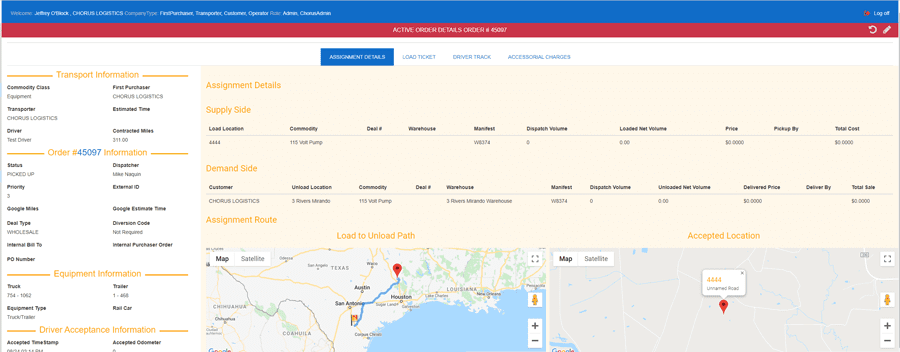
Haulers face many other challenges where automation can streamline business efficiency. Consider the International Fuel Tax Agreement, or IFTA, which requires haulers to regularly disclose their fuel usage when they operate in multiple states, such as crossing the Texas/Oklahoma state line with a load or moving between U.S. states and Canadian provinces. Given the record keeping involved and complexity of IFTA reporting, staying up-to-date and compliant requires significant time and resources each month. With the TollTagger app, however, IFTA reporting is completely automated because the system records fuel usage, calculates mileage and prepares requisite forms without any intervention from the carrier.
The technology is also helping haulers get paid more and faster. Because many producers can take months to pay invoices, haulers resort to invoice factoring or selling their accounts receivables to a third party for less than they’re worth (typically around 80 percent), trading revenue for immediate cash flow. With carriers and producers doing business through AXLE Hub, hauling invoices are automatically aggregated across all carriers, profoundly simplifying the invoicing process for the producers involved and enabling haulers to get paid on the same day in some cases.
Lean, well-orchestrated hauling operations can trim 30 cents or more for every barrel of water trucked. For haulers it’s a competitive advantage and, for many producers, the reduction in lifting cost can be the difference between making or losing money.
Instead of receiving thousands of invoices per month, AXLE Hub provides one consolidated invoice for producers, enabling them to shrink costs further by reducing the G&A and technology costs of managing oil field transportation in-house.
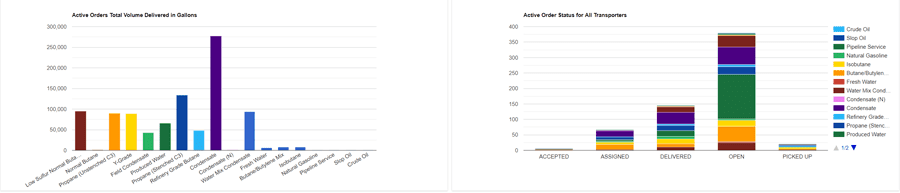
AXLE Hub and TollTagger create new opportunities for pipeline operators too. Pipelines are only a partial solution to the country’s produced water challenge. AXLE Hub enables anyone to get into the virtual trucking business and offer their customers a complete water management solution. This enables a water pipeline operator to become an intermodal transportation provider by effectively creating a virtual trucking fleet through AXLE Hub, which puts it in control of how and where customer water is moved. For pipeline infrastructure and disposal wells that can cost billions to build, this puts more power in the hands of midstream service providers to extract more value from their assets while extending their reach with a network of intermodal capabilities, including rail and marine.
Building the Best End-to-End Energy Supply Chain
Water management is just one facet of the complex logistical needs of today’s energy market. A dynamic industry requires more than a static snapshot into where a given commodity is. It requires a dynamic and real-time view into the flow of every molecule in order to optimize costs and supply chains. Crude, natural gas, NGLs, water and refined products are increasingly moving along the value chain in a constantly evolving mix of pipeline, truck, rail, barge, ship, and vessel, underscoring the need for new ways to manage intermodal and cross-commodity transportation.
Chorus Logistics (a W Energy Software company) is responding to the needs of the industry by offering each stakeholder in the value chain deep insight into where commodities are at every stage and at every moment. Equipped with its AXLE Hub and TollTagger technologies, upstream, midstream and downstream gain new agility, business performance and cost efficiencies. Benefits for companies along the value chain include:
- Producers – Simplifies invoicing, eliminates the transportation management cost center, and provides a granular view into how, where and when commodities are moving.
- Carriers – Increases operational efficiencies, reduces G&A and technology costs, and enables savings to be passed back to producers.
- Pipelines – Provides customers with a complete intermodal transportation solution and enables the operator to control the destiny of the commodity it is moving.
- Purchasers – Enables crude purchasers to source and streamline delivery of specific commodity grades and composition and respond to evolving market conditions.
- Processors – Reduces transportation costs and risks, improves marketing operations, and keeps producers and customers up-to-date.
- Refineries – Provides a deep view into long supply chains and enables visibility into the movement of clean fuels.
More than ever before, energy companies need a holistic picture of the flow of commodities across basins and modes of transportation, viewed from the right lens in ways that support their business drivers in the energy value chain. Chorus Logistics complements W Energy Software’s overall vision of delivering the only fully unified oil and gas SaaS ERP, spanning upstream and midstream workflows, including financials, upstream accounting, land management, production operations, gathering, pipeline, plant accounting, marketing, trading and risk management.
Bolstered with technology, energy companies are gaining new flexibility to adapt and reduce transportation costs armed with actionable insights into commodity movement. Increasingly, the physical and accounting movement of hydrocarbons, water and refined products is being seamlessly managed through W Energy Software.
Jeff O’Block has an extensive background in energy accounting and transportation. He is the founder of Chorus Logistics, the leading provider of cloud-based and mobile transportation management solutions (a W Energy Software company). O’Block co-founded Confirmation Corporation, (acquired by the New York Mercantile Exchange in 2002), a developer of software that provides confirmation services to subscribed trading companies. He is co-founder of Texas Cedar Clearing, which has become a premiere oil services company in Texas specializing in seismic line clearing, road building, transportation, site preparation and cleanup, pipeline construction and right-of-way work. O’Block was also the co-founder of PSC Energy, the original developer of GMS, one of the most successful energy trading platforms that became a very popular trade capture, scheduling, and accounting system (acquired by Altra Energy in 2000 and now supported by Sungard). He has assisted pipeline companies in authoring tariffs and is an expert in pipeline operations. O’Block is also a pilot with more than 3,000 hours of flight time.
Headline photo courtesy of Shutterstock/Pavel Chagochkin
Jeff O’Block has an extensive background in energy accounting and transportation. He is the founder of Chorus Logistics, the leading provider of cloud-based and mobile transportation management solutions (a W Energy Software company). O’Block co-founded Confirmation Corporation, (acquired by the New York Mercantile Exchange in 2002), a developer of software that provides confirmation services to subscribed trading companies. He is co-founder of Texas Cedar Clearing, which has become a premiere oil services company in Texas specializing in seismic line clearing, road building, transportation, site preparation and cleanup, pipeline construction and right-of-way work. O’Block was also the co-founder of PSC Energy, the original developer of GMS, one of the most successful energy trading platforms that became a very popular trade capture, scheduling, and accounting system (acquired by Altra Energy in 2000 and now supported by Sungard). He has assisted pipeline companies in authoring tariffs and is an expert in pipeline operations. O’Block is also a pilot with more than 3,000 hours of flight time.
Oil and gas operations are commonly found in remote locations far from company headquarters. Now, it's possible to monitor pump operations, collate and analyze seismic data, and track employees around the world from almost anywhere. Whether employees are in the office or in the field, the internet and related applications enable a greater multidirectional flow of information – and control – than ever before.