“If you want the good stuff (performance), then you have to use the bad stuff.” This has been a long-standing slogan in the oilfield production chemicals business, referring to the use of synthetic chemistries. The meaning of it? Chemicals that performed the best were also some of the most toxic and environmentally harmful products to use—resulting in a difficult choice of selecting performance and cost over safety and sustainability.
For decades, chemical usage in the oilfield has been ubiquitous by operators to control and manage risk associated with a variety of flow assurance challenges, including wax deposition—one of the most common and challenging. While synthetic chemicals are relatively low in cost and offer variable results, their ongoing use can result in long-term formation damage, as seen in hot oiling applications for paraffin remediation.
Today’s paraffin remediation problems need more than conventional treatments. With ever-changing well characteristics, specific regional challenges and increasing formation damage from using hot oil or brine applications, customization and a new approach are crucial to stay profitable and extend the life of older wells. But is there an alternative? Enter biosurfactants.
Outperforming Chemicals with Green Solutions
Chemical suppliers have attempted to introduce green solutions for paraffin remediation into the oilfield, but with variable results and high costs. Standard production methods limited volume capacities and caused challenges in achieving biodegradability with reduced bioaccumulation, while retaining temperature stability, persistence in application, and stability for transportation and storage.
The most promising green solution for paraffin remediation is a unique class of surfactants knows as biosurfactants. Biosurfactants are highly biodegradable, low in toxicity, offer a smaller carbon footprint and have endless application possibilities. Most importantly, biosurfactants have an unmatched ability to enhance traditional remediation methodology and offer added production benefits through their enhanced oil recovery capabilities.
Historically, biosurfactants have been too expensive for oilfield applications, until recent advancements in fermentation technology enabled the cost-effective production of high-quality, pure solutions with consistent, proven results—in volumes large enough for oilfield use. These new customized biosurfactant solutions are outperforming synthetic chemicals and allowing the multiple benefits of green chemicals to be realized in the oilfield for the first time.
The result? A growing movement across the industry in replacing hot oiling and standard synthetic dispersing agents with biosurfactants.
The Hot Oiling Replacement Movement
Due to low cost, rapid results and simple application, hot oiling has been the most widely-used method for removing paraffin deposition. This conventional method utilizes thermal heat transfer from heated oil or brine to heat the paraffin above the wax appearance temperature and dissolve it. The paraffin is then typically kept dispersed using a dispersant. Although this appears to be a practical way to manage paraffin deposition, the reality is many producers suffer from hot oiling formation damage. This is when precipitation of high molecular weight waxes, asphaltenes, and inorganics occur. The sources of this can come from impurities in the oil or brine sources used for the thermal heat transfer, or procedural errors that push paraffin deposits from the rod and tubulars out into the formation. The complications and safety hazards associated with hot oiling have led some producers to explore alternative remediation methods, such as biosurfactants.
Case Study: Making the Change in the Permian
A producer in the Permian basin decided to travel down the unconventional path of using biosurfactants to remediate paraffin from the rod, pump, tubulars, and nearby wellbore. The difference in this producer’s scenario was that instead of applying live microbes downhole and relying on those microbes to metabolize organics insitu and excrete biosurfactants, this producer decided to pump a purified biosurfactant mixture, produced by Locus Bio-Energy Solutions, that contained no live microbes. Known as AssurEOR FLOW™, this biosurfactant solution was derived from a fermentation process in a local production plant in Midland, where the molecules are produced under tight tolerances. This was a game changer for the producer because this reduced variability and ensured that the high-quality biosurfactants could be reproduced in a consistent manner.
To ensure that the producer had an apple-to-apples comparison, a lease that contained nine producing vertical wells was used as the live experiment. These vertical producing wells were in Upton county and produced oil from the Wolf-camp and Leonard tight shale formations. This lease had been hot oiled for years with different degrees of success and failure—the ladder had become more frequent, which provided a solid foundation to evaluate the efficacy of the AssurEOR FLOW ™ treatment.
Treatment success was evaluated in three factors: a dispersion and dissolution kinetics test to determine if the biosurfactants could disperse paraffin into solution, fingerprinting the CCD (Carbon Chain Distribution) of oil from the wells before the biosurfactant treatment and after to see if an appreciable increase in carbon chains was detected, and a comparison of production trends from when the lease was hot oiled to after the biosurfactant treatment, adding a new dimension to the paraffin remediation program.
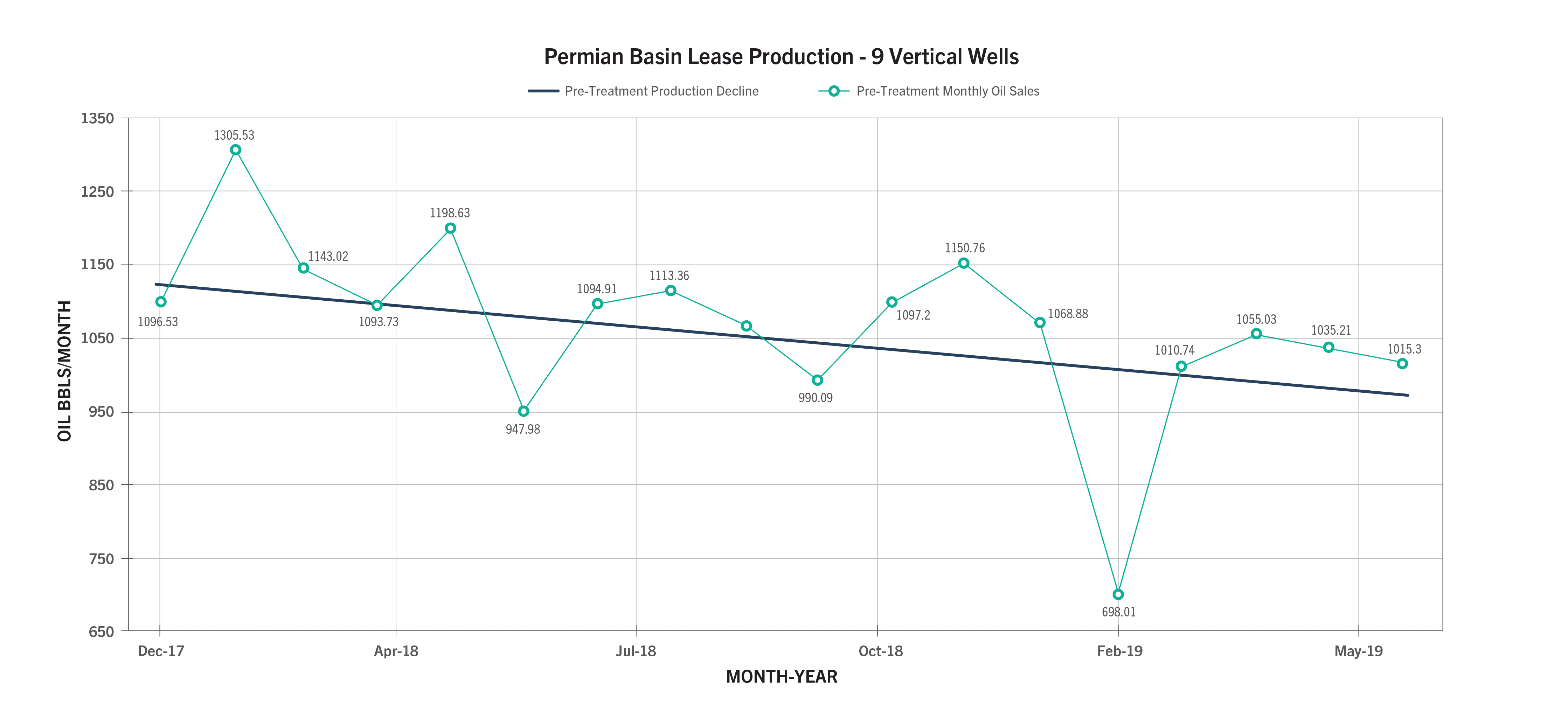
Factor One: Dissolution and Dispersion Kinetics
The oil production of the wells drilled in a tight reservoir were continuously decreasing over the previous months (Figure 1), and wax deposition was also observed (Figure 2 – Left Side). The precipitation and deposition of waxes are related to permeability reduction and formation damage around wellbore, changes in rheological behavior, increasing of viscosity, excessive pumping cost, oil production reduction, interior diameter reduction of pipelines and in severe cases the blockage of wells and equipment. In order to evaluate if a biosurfactant-based product would be able to disperse the wax deposit, a Dynamic Wax Remediation Test (DWRT) was performed. The DWRT results were obtained by observing the dispersibility of 2 grams of wax deposit in a tube with 30 mL of AssurEOR FLOW™ at 95° F and rotating at low speed (5 RPM). The results showed that after only 2 hours, the wax deposit was completely dispersed with high flowability (Figure 2 – Right Side).
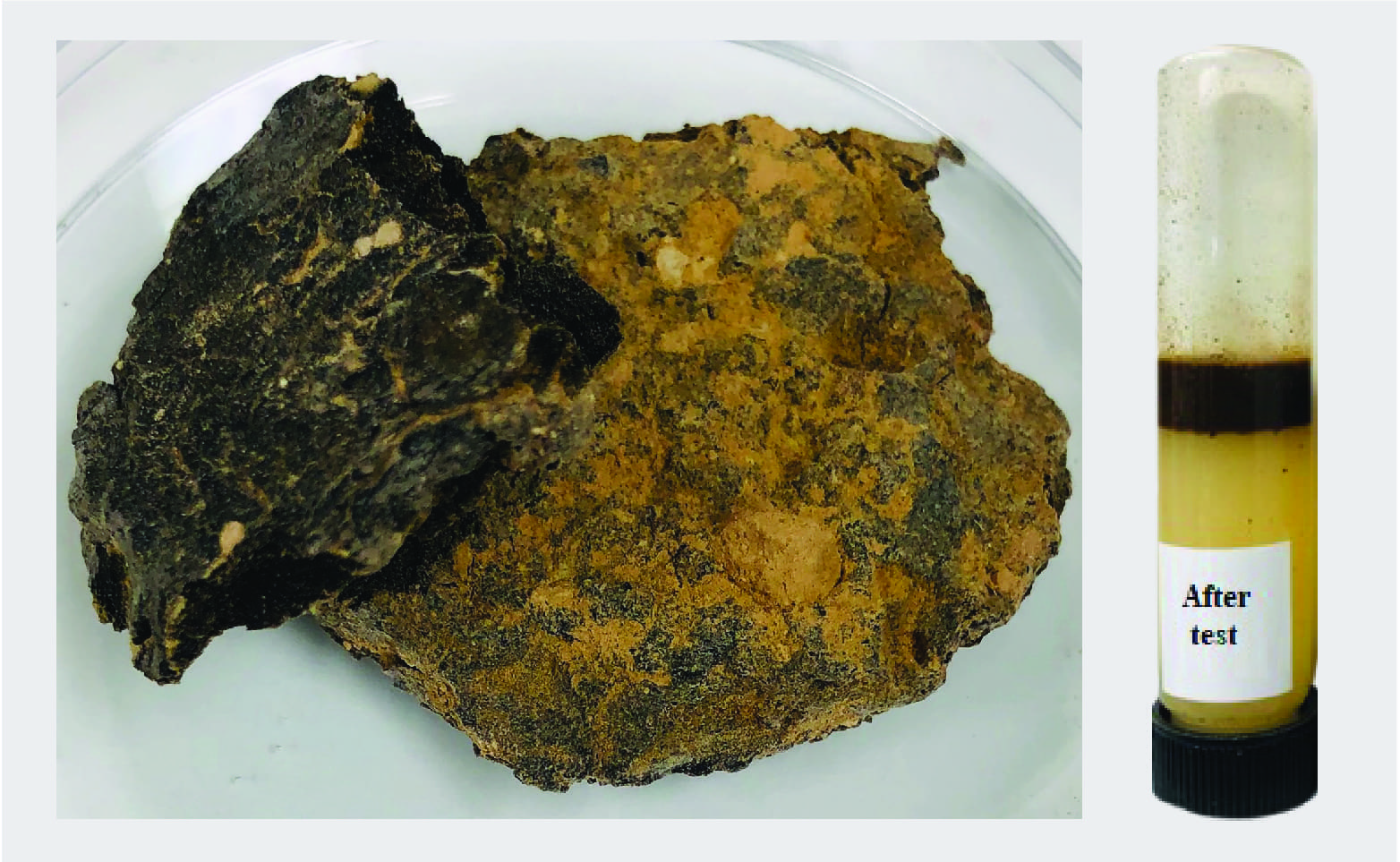
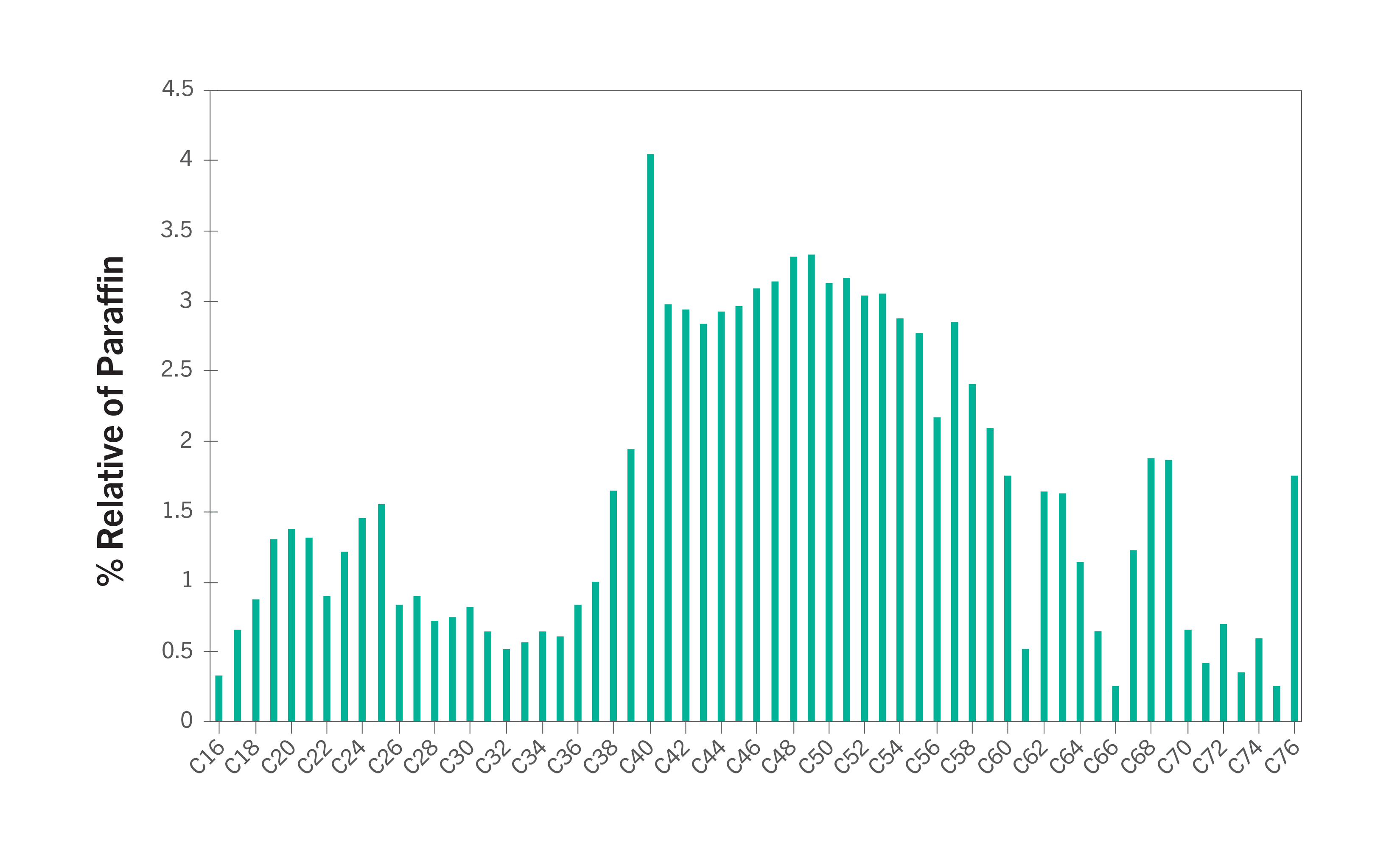
Factor Two: Carbon Chain Profiles
A study based on CCD showed that the wax deposit contained macro and microcrystalline waxes with long paraffin and carbon chains up to 76 carbons (Figure 3). Considering that deposits with long carbon chain normally present high Wax Disappearance Temperature (> 113° F), AssurEOR FLOW™ proved to be efficient even under hard conditions on DWRT, performed at 95° F.
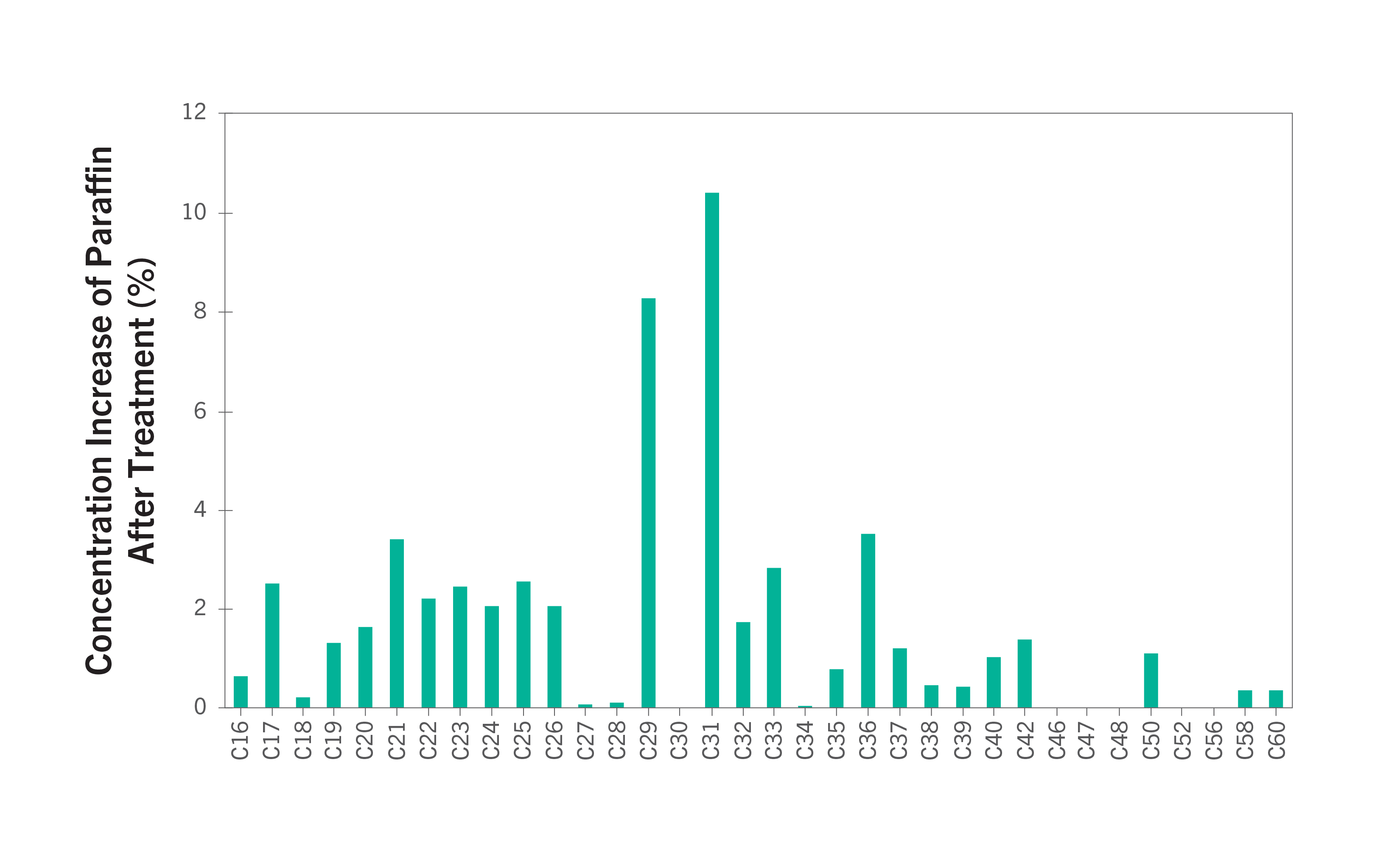
The CCD study also showed an increase of paraffin amount in crude oil after treatment (Figure 4), the largest increases in paraffin concentration were observed for paraffin with 29 and 31 carbons (8 percent and 10 percent, respectively), but the concentration of shorter and longer carbon chains were also increased. This data combined with the observations of the operator that claims not observe wax deposition after treatment confirmed the assumptions based on DWRT, that AssurEOR FLOW™ is able to disperse the wax deposit in the reservoir and in the pipeline, leading to an increase in the amount of paraffin in the oil.
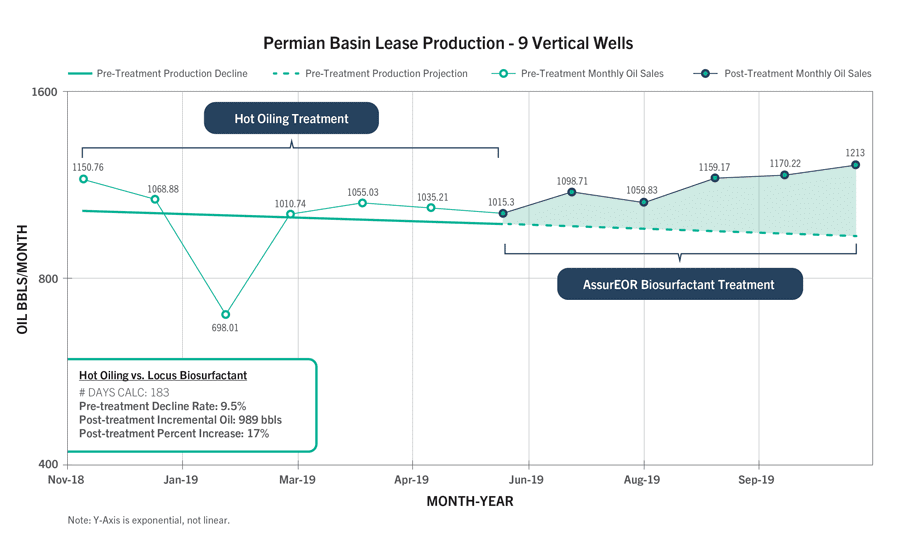
Factor Three: Production Trends
A production decline rate of 9.5 percent was calculated as the baseline projected decline for the lease that was treated with hot oiling. To the surprise and fascination of the producer, production rates began to steadily increase over the 6-month period following the AssurEOR FLOW™ paraffin remediation treatments. The biosurfactant treatments were deployed on a monthly basis and provided a 17 percent increase in production over that time period. Figure 5 depicts the monthly production trends during hot oiling and the biosurfactant treatment program.
Conclusion
The depletion of conventional oil reserves and the large oil production increase from unconventional and tight reservoirs since the mid-2000s have made wax deposition an ongoing challenge. Its impact on lowering the ability of wells to reach predicted maximum recovery, slow cleanup and production decreases, along with growing safety and environmental concerns within the industry, creates a crucial need for highly-effective, green solutions. Results prove that biosurfactant-based solutions are not only a greener, biodegradable, low toxicity option, but also a highly efficient product able to eliminate wax deposition problems and increase oil production. This approach opens up a world of possibilities in deploying biosurfactants in unconventional ways to achieve unmatched benefits. Goodbye hot oiling; hello biosurfactants.
Jason Thompson, Business Development Director, Locus Bio-Energy Solutions. Jason is responsible for developing and managing Locus Bio-Energy’s award-winning AssurEOR treatment program business in the US. For the past 16 years he has been working in all aspects of oil field production chemicals, previously as the District Manager of USA West (California and Alaska) for Clariant Oil Services. Jason holds an MBA and is qualified as a Six Sigma Black Belt.
Dr. Janaina I. S. Aguiar, Application Scientist, Locus Bio-Energy Solutions. Dr. Aguiar is a chemical engineer with Master’s degree and PhD in Science and Technology of Polymers. She has more than 10 years of experience in oil R&D. Dr. Aguiar has experience studying the mechanisms of actions for oilfield solutions and finding innovative solutions for flow assurance problems related to asphaltenes and wax deposition, emulsions stability and compatibility of surfactants and polymers.