To continue to reduce costs, frac sand companies and oil companies have started to build their own frac sand mines in the Permian Basin, located mostly in the western part of Texas and in the southeastern part of New Mexico. While the quality of these in-basin frac sand mines is slightly lower than Wisconsin White Sand, operators cut millions from their capital budgets by supplying their own frac sand closer to their production sites in West Texas.
This trend marks a significant shift in the sand mines industry, as in-basin frac sand now accounts for a majority of the market, which has started rail shipments out of the Permian Basin and dissipated frac sand shortages.
However, access to power grids remains limited. It can take a utility company anywhere from 12 to 24 months to set up the infrastructure required to power a frac sand mine; however, after investing $100 million in a new mine, suppliers cannot afford to hold production until power becomes available from the utility company.
Modular natural gas generators bridge the power gap, enabling mines to start production and enter the market before the installation of permanent utilities. Rental power companies and owners and contractors’ electrical engineers work closely to develop a sophisticated, cost-effective and environment-conscious power plan for each mine that delivers the following benefits:
Low-cost Natural Gas
Mine operators seeking alternatives to diesel find natural gas to be an attractive option. Natural gas cost 40 to 45 percent less than diesel and since they need to supply their sand dryers with natural gas the use of natural gas generators is a no brainer.
However, the costs associated with natural gas generation, installation and operations, as well as the required maintenance of these complex installations, prove far less than the cost to hold production until permanent power is available, which can take years. In fact, multiple Permian sand mine developers are already using 83 megawatts of natural gas power in a market previously dominated by diesel.
Reduce Environmental Footprint
Over the years, many local governments and authorities have raised concerns about the long-term continuous use of diesel generation because of NOx pollutants. Tighter regulation means sand mine developers are expected to explore alternative options to minimize energy waste, reduce greenhouse gas emissions and improve air quality.
Mine operators find natural gas to be a good option for environmental reasons because natural gas emits roughly 30 percent less carbon dioxide than diesel fuel according to U.S. Energy Information Administration. With the emergence of lean-burn engine technology, natural gas power generators also meet the U.S. Environmental Protection Agency’s emissions regulations.
One Size Does Not Fit All
Projects vary greatly and so must power configurations to achieve each unique site’s needs and required redundancy levels. Thanks to a well-engineered power solution, the sand mine’s power capacity can ramp up or down, or the diesel can be swapped out for natural gas should it become available later.
Also, gas-powered generation can install a redundancy of N+1 to achieve 100 percent uptime should a generator fail or to allow a generator to be serviced every 30 days for maintenance, as required. A sand mine operator certainly doesn’t want to shut down or reduce production due to routine maintenance on a generator.
Grounding
Inadequate grounding and ground testing leaves personnel and equipment at risk and doesn’t meet Mine Safety and Health Administration requirements. The process of accurately measuring ground resistance is essential to verify proper grounding and ensure the protection of people and equipment. Proper grounding in highly resistive soil such as sand is much more difficult than in other materials like dirt or clay. Certification of correct grounding in large power grids such as these usually calls for a different method of testing.
Remote Monitoring
Given the off-grid locations of most mines, it is essential to have a remote monitoring system in place to monitor and verify the operation of the power system. Remote monitoring alerts engineers immediately of an issue and allows for swift and focused decision-making before a costly problem or worse, downtime can occur. Such an incident can cost a mine up to $15,000 an hour. The 24/7 monitoring of the installation, operations and required maintenance of these complex power systems enable operators to devote a larger share of capital to other mine projects.
Natural gas provides cost-effective, sustainable, flexible and dependable power for frac sand mines waiting on permanent power. Mines can start up to almost a year ahead of schedule thanks to modular natural gas power, potentially generating $100 million of revenue in 11 months for the operator.
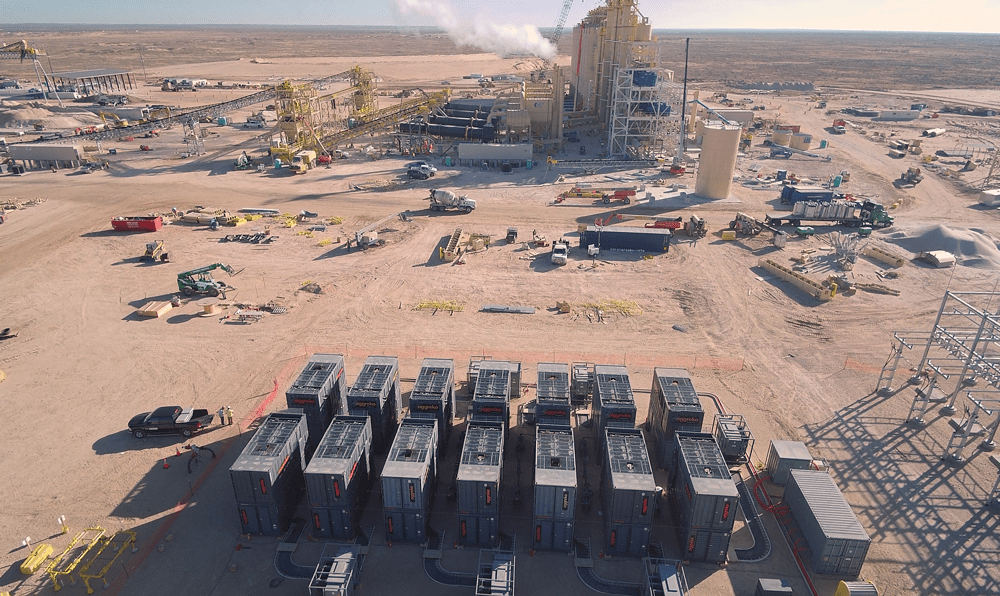
Mike Mayers is a business development manager specializing in the frac sand industry for Aggreko, based in Houston, Texas. Call Aggreko at 1-800-AGGREKO (1-800-244-7356) or visit www.aggreko.com whenever you need help.
Josh Haugan is a business development manager based in Houston. Call Aggreko at 1-800-AGGREKO (1-800-244-7356) or visit www.aggreko.com whenever you need help.
Oil and gas operations are commonly found in remote locations far from company headquarters. Now, it's possible to monitor pump operations, collate and analyze seismic data, and track employees around the world from almost anywhere. Whether employees are in the office or in the field, the internet and related applications enable a greater multidirectional flow of information – and control – than ever before.