Corrosion can be defined as the deterioration that a metal suffers from being under exposure to electrochemical molecules that are in its environment, creating permanent damage to the surface and, in many cases, even worse.
In the article, “Corrosion – The Longest War” published by Schlumberger, it mentions that in 2015 the annual cost of the effects of corrosion was $500,000 in the United States alone. This budget was six times bigger than the one for natural disasters.
Corrosion is one of the most frequently recurring problems the oil industry faces today, just as it has in the past. The article written by Kermany in 1995 for the Society of Petroleum Engineers (SPE) mentions that out of the failures that occur in the operations of the gas and oil industry, the most important is corrosion, which was involved in 33 percent of the cases at that time.
This number has dropped over time due to the use of new alloys, but challenges related to reservoirs with more contaminating fluids also increased, as did both hydraulic and matrix stimulations. All these factors cause metals to come into contact with fluids for which they are not normally prepared, accelerating the corrosion process and, in some cases, even creating corrosion immediately, compromising the structures and lives of the wells over time.
In view of the different problems, there are different tools and technologies that are designed to detect corrosion early on and others designed to mitigate such processes.
Technologies to Detect Corrosion
Corrosion not only affects the operational sector of the oil and gas industry, it also affects the tasks performed in a refining complex. This is why Imperial College London-Permanense developed the use of Radio Frequency Identification (RDIF) sensors upon request from bp, to be installed in its 11 refineries worldwide.
RDIFs are sensors widely used for different activities. For corrosion detection in pipes, they focus on the use of radio waves that travel the metal surface where multiple emitters are distributed throughout the pipe.
The emitting sensors are also information receivers and together they are able to provide an overall picture of the pipe’s integrity. Using sounds, they go off when corrosion occurs, which can be noticed at different levels, thus facilitating early detection and being able to choose which type of repair methodology to use.
In 2017, the company Draper took notice that in the U.S. alone, gas and oil pipelines travel over 2.5 million miles of mountains, forests and urban wetlands, whose characteristics create the perfect conditions for corrosion to occur. Overhead pipelines were not prepared and losses related to pipe problems and repairs increased.
For this reason, Draper decided to focus its efforts on creating an economical and reliable technology to detect corrosion in pipes around the country. Draper’s team of engineers developed WiSense, an identification network, which centers on the detection of the pipe’s magnetism, corrosion being one of the fierce enemies of this characteristic in metals. WiSense is placed directly on the pipe, emitting a conductive signal on the metal and, when it detects a drop in its magnetism, it emits a signal to the checkpoint, thus detecting the growth of corrosive agents immediately.
Draper is dedicated to the transportation of hydrocarbon, knowing that in order for this technology to succeed both low costs and minimal human operation are needed. They used the Internet of Things (IoT) to create a conductive loop, where each of the responses from the magnetic sensors located throughout the pipe is monitored by its hydrocarbon distribution system, making it a single data network where, in addition to being able to read the pressure, temperature and volume values of the fluids, workers can also check the integrity of the metal equipment.
The lifespan of Draper’s patented sensors is 10 to 20 years, during which time no battery change or human interference is required to ensure their operation.
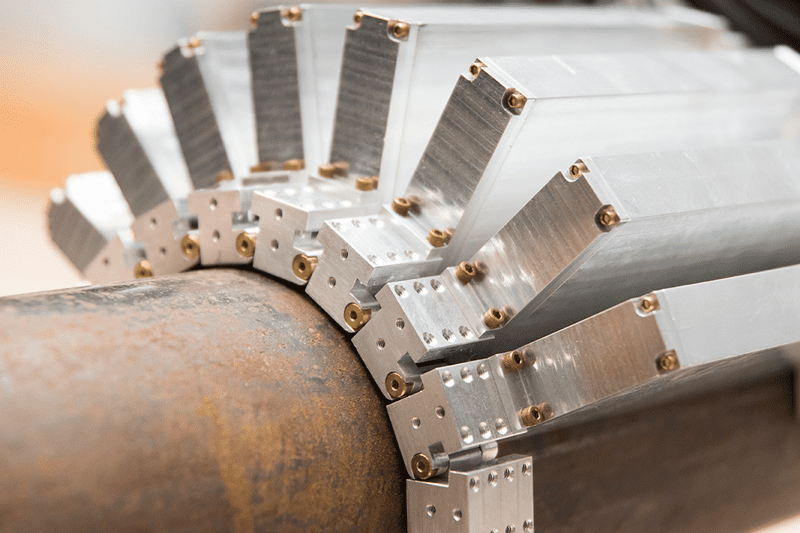
The inclusion of fiber optics is in the race to find out which is the best corrosion detector in pipes. The article, “External and Internal Corrosion Detection Sensors for Oil and Gas Pipelines Using Fiber Optics,” written by Dr. Nader Vahdati and company in 2018, presents a detailed study on the technology provided by Fiber Bragg Grating, which is based on the use of a permanent magnet.
Following the same line as Draper, FBG’s engineers designed a prototype in which they took advantage of how economic fiber optics are to use them as a data bus, and use the FBG sensor as a detector, based on the reading of internal pipe material loss normally caused by corrosion. In this first prototype, the FBG sensor is capable of issuing an alert when the pipe drops below a 3mm thickness.
A small sensor placed on a thin metal sheet that is then bolted to the pipe works as a thickness reader. By early 2021, FBG hopes to patent this innovative tool, as well as its big brother, which is capable of working with greater thicknesses.
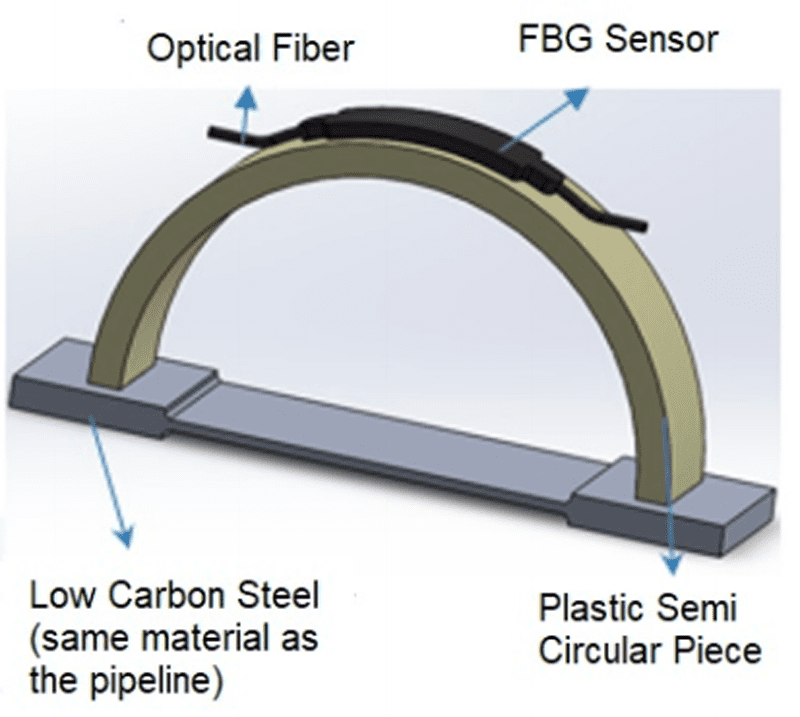
Techniques and Technologies to Avoid Corrosion
It is better to have an ounce of prevention to a pound of cure. In his article, “Use of Polyurethane Coating to Prevent Corrosion in Oil and Gas Pipelines Transfer,” written for the University of Mahshahr, Iran, in 2012, engineer Amir Samimi proposes a plan to use a triple layer of coating to improve the external corrosion resistance in the pipe over time.
With the use of a first layer of polyolefin, this material acts as insulation against the oxidizing ions in the metal by limiting movement and its spread. As an intermediate layer, copolymer is used, which is responsible for improving the adhesion of the polyolefin and further restricts the occurrence of electrolysis; finally, it is covered with an epoxy coating, which acts as a sealant agent which provides greater resistance to shock and high temperatures to which the pipe is exposed. The disadvantage to this type of method is how difficult it is to install in old, settled and working pipes, and in turn it represents added costs for new installations.
There is a great battle in the development of corrosion inhibitors. One of the competitors is Baker Hughes with its CRONOX ™ corrosion control solutions. This element can be used in drilling or production areas as well as in transport and refining areas. It has a great duality thanks to its HP/HT characteristics. It is also able to resist attacks of oxidizing agents such as CO2 and oxygen.
CRONOX was tested by Dr. Mihalea Alexandra, which she writes about in her article, “Corrosion Inhibition Process of Carbon Steel in Hydrochloric Acid by CRONOX,” written for Politehnica Timişoara University in 2017. In this study, she tested CRONOX in two cases: weight loss and linear polarization by the Tafel polarization method.
In the experiment, a cylindrical disc cut from a carbon sample was used; hydrogen chloride or hydrochloric acid or in its hydrated form (HCI), which is a highly corrosive agent and is present in most oxidation processes to which pipes are exposed in the oil and gas fields, was used as an oxidizing agent. Subsequently, for the gathering of results, she used electrochemical studies to detect corrosion.
For the Tafel polarization method, the disc was exposed to temperatures of 298°k to 338°k, with a concentration of one M CHI and 0.1 percent of CRONOX for 240 hours, and another experiment was conducted without CRONOX during the same time. The application of CRONOX yielded positive results in improving the resistance to oxidation. The results are shown in Figure 1 & 2.

In Figure 1 you will notice how the oxidation accompanies the piece throughout the whole process, corrosion being the lines that are in the lower plane.
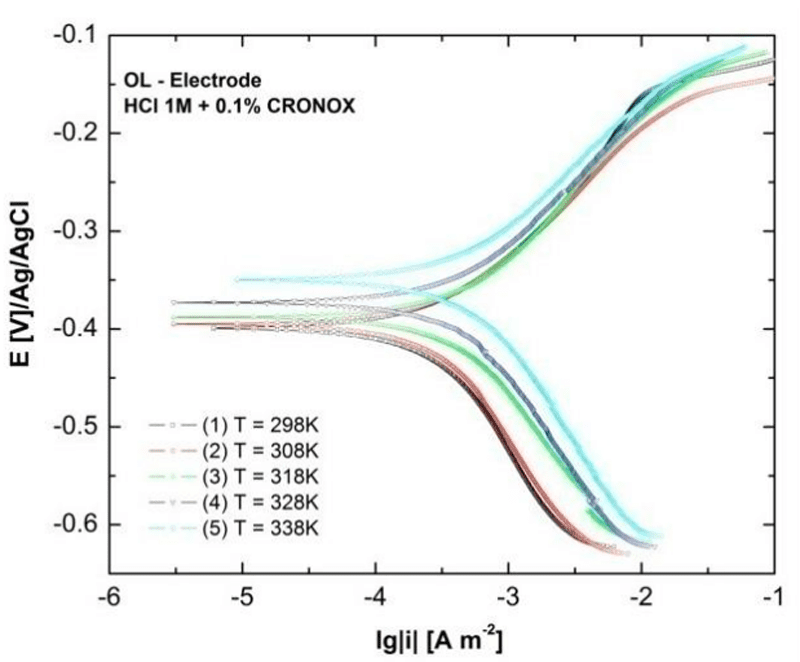
In Figure 2 you can see how CRONOX inhibits the corrosion process by stopping its occurrence during the experiment.
Subsequently, a study was carried out on the tested plates based on the mass loss they experienced when CRONOX was and was not present in the process. The results gave a green light to the use of this compound as an inhibitor.
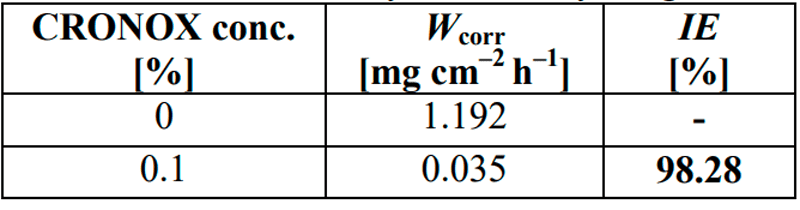
The best way to work with corrosion is to avoid any existence of it. Also, it is known that some structures are already very long-lived and were not properly prepared before this derivation. However, there will always be detection methods to address the problem in time.
Headline photo – Pipe corrosion. Source: PV Productions – www.freepik.com
Raul Palencia is an engineer and researcher with more than 10 years of experience as a geologist. He graduated from the prestigious University of Andes (ULA), later he received a master’s degree in reservoir engineering at the Venezuela Hydrocarbons University. During his career development, he worked for oil companies in positions such as: field geologist, reservoir engineer and reservoir simulation. He has worked in Argentina, Ecuador, Mexico and Venezuela. He currently resides in Texas.
Oil and gas operations are commonly found in remote locations far from company headquarters. Now, it's possible to monitor pump operations, collate and analyze seismic data, and track employees around the world from almost anywhere. Whether employees are in the office or in the field, the internet and related applications enable a greater multidirectional flow of information – and control – than ever before.