The drilling industry’s push for increased digitalization has been driven by new data formats, innovative software applications as well as an ever-increasing abundance of real-time data. Oil rigs have turned into massive sources of data that help engineers, some of whom work at ROCs (remote operations centers) aid operators in gaining greater yields and less downtime. Oil companies also utilize many sensors that are installed on/in wells and equipment to provide continuous data-collecting and real-time monitoring. Innovations in drilling systems have also been generating large amounts of data during drilling operations. For example, tools such as LWD (logging while drilling) and MWD (measurement while drilling) are able to transmit various data to the surface in real time. ROCs have been a driving force in these trends, as they are places where this massive amount of data is captured, processed, analyzed, actioned and stored. ROCs have many different software technologies and hardware solutions that integrate information to support work processes that teams conduct. Drilling engineers have been able to gain valuable analytical insights from the data that gets analyzed at ROCs. This has enabled them to help operators optimize operations and reduce non-productive time.
There is no denying that both operators and oilfield service providers have evolved to be data-centric enterprises that rely on analytics to make key decisions. Leveraging analytics involves recognizing meaningful patterns in data. Effective decisions and actions come from valuable insights gained from a combination of mathematics, statistics and other techniques.
Where Does Data Come From?
Most oilfield data (which is structured) comes from SCADA (supervisory control and data acquisition) systems, drilling information, production monitoring, surface and subsurface facilities. SCADA is a configurable set of industrial software applications that can be used to support management of many different types of process production. In the upstream sector, SCADA’s role is typically in support of remote data gathering and transmission. SCADA is able to collect data at remote oil and gas sites, thus it reduces personnel visits. Asset, risk and project management reports also offer structured data. Unstructured data, on the other hand, comes from well logs and daily reports. Modeling and simulation provides semi-structured data.
Drilling data/information comes from downhole sensors that are placed near the bit, bottom hole assembly or drill string with the sensors recording data in memory mode or transmitting the data real-time through various forms of telemetry. The information that is collected at a rig is typically sent to an ROC where it is stored in a database. Analysts or drilling engineers have to deal with this massive amount of data and need to extract meaning from the patterns and relationships in order to take appropriate actions or recommendations.
Combining this new data with old records that have been converted into digitized coherent data sets have proven to be valuable for fully understanding an operating asset.
What Does Data Analytics Achieve?
There’s a lot that goes into analytics. Engineers at ROCs conduct geophysical modeling and simulation where 2D and 3D tools and technologies generate visual data reports. ROCs also provide analysis for a wide range of data types including: MWD, LWD, image logs, seismic data, geological models, trajectory projections and real-time drilling performance data. Once an analyst has access to data from logging, MWD and other methods, they utilize various applications to extract meaning or knowledge from it. Drilling parameters from offset wells are analyzed to create an offset model that is later correlated to a drilling plan for other wells or the well currently in operation.
Additionally, data from continuous, real-time monitoring of assets helps identify conditions or anomalies that may impact operations. ROCs actually provide analysis and monitoring of wells during the drilling process, after drilling and during completions and production operations. During all of these phases, ROCs provide analysis for the behavior of the well. This aids in an improved understanding of well characteristics. It also helps to minimize HSE (health, safety and environment) risks and overhead costs.
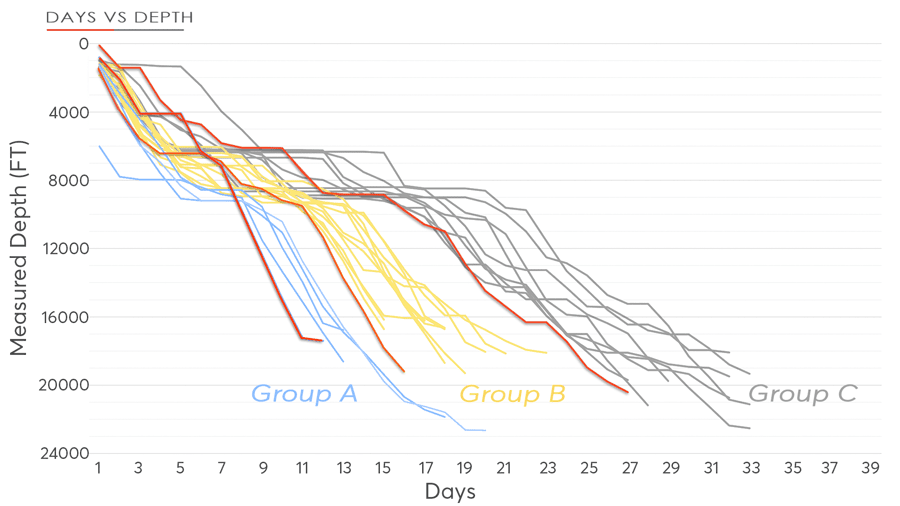
Models and Simulations
Analytics also build on the assessment of drilling models. These models are based on existing well data. They are incorporated with geological measurements into drilling processes. Models get updated based on incoming sensor data from rigs. This helps to optimize drilling parameters. BHA (bottom hole assembly) modeling also enables the performance of nodal analysis to identify the operating parameters. BHA models are useful for determining the ideal well parameters. Engineers are able to apply the modeling to troubleshoot and optimize wells. Torque and drag modeling in particular allows operators to evaluate actual automated real-time data points instead of modeling so they can improve downhole efficiencies. Additionally, analytical models are able to serve as an early-warning system, which helps operators avoid significant nonproductive time events during drilling operations.
With drilling simulation, a real drilling operation is replicated into drilling software. Simulation modeling involves optimizing the drilling of the well. Experts use sophisticated computer modeling software to simulate down-hole conditions. Well logs specifically provide knowledge into the formation and geology of a subsurface area. They are able to characterize a wellbore, fluids and formation. Analysis of well logs provides engineers with data regarding porosity, permeability, resistivity, lithology and fluid type. Such analysis can also determine an estimation of reserves of hydrocarbon and detect fractures. Engineers use well logs to conduct qualitative and quantitative assessments of reservoirs. Based on this data and assessments, experts also develop an integrated drilling plan and drilling system with the goal of achieving maximum performance and optimal recovery. Well plans typically allow experts to create effective strategies that lead to the accurate placement of wells without collisions.
Key Performance Indicators
Key performance indicators (KPI) are another important aspect of data analytics. Experts utilize statistical forecasting techniques to build future trends for KPIs. Features include: a description of rock property, the orientation of well trajectory, water volume, chemical composition as well as the density of wells. Experts also use a composite similarity matrix to identify wells that have similar behaviors across an area. KPIs and drilling data help experts understand how to improve drilling. They also help identify risks and opportunities. By utilizing offset well benchmarks, experts develop a drilling plan. Once this plan is in place, they continue to gather and visualize information from the surface and downhole environments. This allows them to make recommendations that help to minimize risks and improve performance.
Why are Analytics Beneficial?
Data and analytics help operators gain a better understanding of their operations so they can address a wide range of factors, such as design decisions, ways to improve operational efficiency, ways to develop new strategies, well mechanics as well as planning and performance.
Due to large volumes of data analytics (which is also referred to as big data), operators and oilfield service companies have the ability to focus more on real-time and agile processes instead of regular monitoring processes. This allows them to produce key insights that help to improve the performance of their operations substantially, while also enabling them to avoid a wide range of problems. Analytics specifically help improve drilling accuracy because they identify issues that could have a negative impact on operations. Additionally, analytics also help experts predict when drilling maintenance is going to be needed or when there’s going to be downtime. Engineers are able to predict further performance based on historical results. It’s critical for operators and oilfield service providers to have an understanding of when maintenance intervals are going to be impacted by flow rate, pressure, temperature, vibration and shock. Having a solid understanding of these factors helps them to prevent failures as well as associated downtime. Predicting equipment failures also has the benefit of allowing teams to more effectively schedule maintenance. Because analytics identify anomalies and issues, they help prevent nonproductive time, which can increase operational costs by 30 percent.
Analytics are also ideal for drilling operations because they facilitate real-time decision making. Engineers make decisions in real time based off of formation geology and drilling parameters, which is used for predictive modeling.
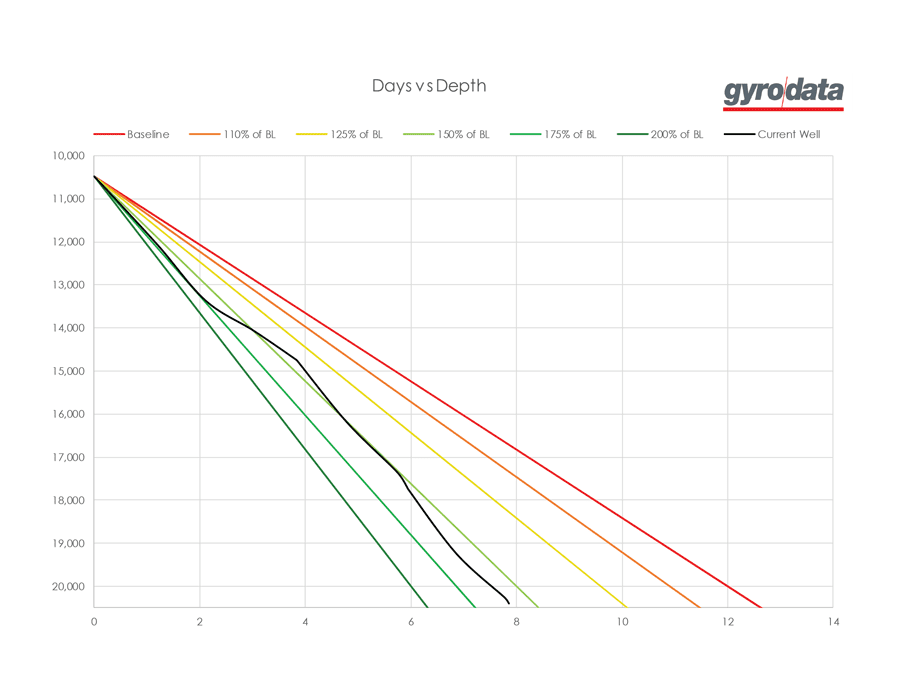
How Gyrodata Utilizes Analytics to Improve Drilling Operations
At Gyrodata’s ROC, the Guide Center, drilling engineers deliver 24/7 real-time monitoring services and support where they analyze a vast amount of data so operators can make vital decisions regarding their drilling operations. Our Guide Center’s well planning, well engineering and real-time optimization services allow operators to optimize well performance. Experts at the Guide Center specifically examine the following:
- Is a gyro required in a surface hole due to the proximity of wells?
- Are there any lost circulation zones that will require lost circulation material?
- Will an agitator interfere with the MWD signal?
- Can the MWD handle the planned flow rates without washing out the tools?
One way that experts at Gyrodata’s Guide Center utilize analytics is by benchmarking wells. This data set helps determine how to drill future wells. Experts also examine large volumes of data to try to differentiate the wells to group them based on, for example, different formations or different hole sizes. They also determine if wells that are within a reasonable proximity of each other illustrate similar drilling behaviors. Analytics allow experts to determine similarities between wells. By analyzing data, they also expand on the successes of the pacesetter and focus on the limitations of the slower drilling of more challenging wells.
As an oil and gas service provider, Gyrodata is frequently compared or measured against the pacesetter wells in an area regardless of the well, casing profile, target formation or hole size that the company is planning to drill. It’s vital to utilize historical data more effectively and efficiently. This can be achieved when experts know the data that they are evaluating. The data should be organized and objectives should be clearly identified. Without a clear picture of what the objectives are, an oilfield service provider may not be capturing the correct data to store in their database. Gyrodata also chooses a criteria range for success. Experts do not just pick the fastest well and duplicate it because the one record-breaking well may have been an exception. Instead, they examine data from ten, 20 or even more wells in an area to identify what made them successful as a whole.
Experts also analyze data that shows the performance of the slowest offset wells in a group to try to figure out why these wells drilled slower. Previous knowledge and data is crucial because it allows service providers to create an effective road map for operators. It’s in service providers’ best interest to implement well engineering, data analytics and offset well data evaluation to determine what parameters should be selected for the best overall outcome.
At the Guide Center, a drilling services team constantly updates the latest historical data while they also monitor the live feeds from each rig so they can seek optimal drilling and validate analytical models. The team looks for the best combination of drilling parameters that will deliver the fastest rate of penetration (ROP) with minimal direction control while also staying within the operating ranges of the downhole tools. The experts utilize this knowledge to create efficient road maps and optimization reports that field personnel use as a drilling guide.
Processes and procedures are in place to minimize tool failures and provide real-time adjustments to parameters, which keeps tools in the hole longer. By utilizing these methods, Gyrodata has optimized and enhanced its drilling practices to achieve superior results.
In one case study, an optimized bottom hole assembly was selected to drill a Wolf Camp A well in the Permian Basin. Based on Gyrodata’s historical data of conventionally drilled wells in this formation, experts were able to apply the knowledge to select the proper configuration for motor assist, rotary steerable system (RSS), and MWD. Drilling with road maps and following parameter recommendations for the entire well were applied. Gyrodata drilled a 9,015-foot lateral in one run with the WellGuide RSS in 43.84 drilling hours. There was an average ROP of 205.8 feet/hour. The operator saved about nine days of rig time and almost half a million in drilling costs.
Overall, Gyrodata’s Guide Center has helped many operators save millions by improving drilling times for peak performance and reducing non-productive time. The center has a circular process of obtaining and reviewing data and utilizing it to support effective decision making so operators can run operations in a profitable and efficient manner.
Conclusion
In summary, the ability to access and draw valuable insights from large data sets has made the drilling industry more profitable and efficient. Experts are able to make forecast, and this allows them to keep costs down. Data analytics has the ability to improve the way operators and service companies manage their entire drilling process. Analytics has improved their ability to characterize sites, spot trends and create repeatable solutions with predictable outcomes. Data from wells, pipeline and other equipment helps drilling engineers to improve well productivity and prevent costly equipment failures as well as HSE risks. Overall, analysis from data analytics in real time has become a necessity for oil companies mainly because it helps to boost drilling performance, improve decision making and lower cost structures. Data analytics is arguably a key driver for drilling a high-quality well on time and under budget.
John Evans has over 30 years of experience in the oil and gas industry. He is the Gyrodata Product Line Manager for rotary steerable system (RSS) and measurement-while-drilling (MWD) services. John manages the technology portfolio and operations technical support (OTS) plus the remote operations Guide Center that provides well planning, well engineering and drilling optimization. John’s primary areas of expertise include RSS, drill bits and drilling technologies, MWD, logging-while-drilling, as well as drilling engineering and optimization.
Oil and gas operations are commonly found in remote locations far from company headquarters. Now, it's possible to monitor pump operations, collate and analyze seismic data, and track employees around the world from almost anywhere. Whether employees are in the office or in the field, the internet and related applications enable a greater multidirectional flow of information – and control – than ever before.