Without a doubt, technology is changing the way we live and work. This notion is nothing new or groundbreaking. For example, the energy industry has been utilizing drone technology since 2013, and processes are becoming increasingly automated universally across industries.
According to a 2017 report from the McKinsey Global Institute, automation could eliminate 500 million jobs by 2030, with 73 million of those located across the U.S. This means employees who do remain will be multi-skilled, will require upskilling and will need a reduced learning curve to keep up with the increasing pace.
At the same time, a new generation of workers is emerging as the experienced workforce reaches retirement or leaves the industry due to the economic downturn. This causes a widening in the experience gap, which means that industries such as oil and gas are seeing significant gaps in the competency of the workforce.
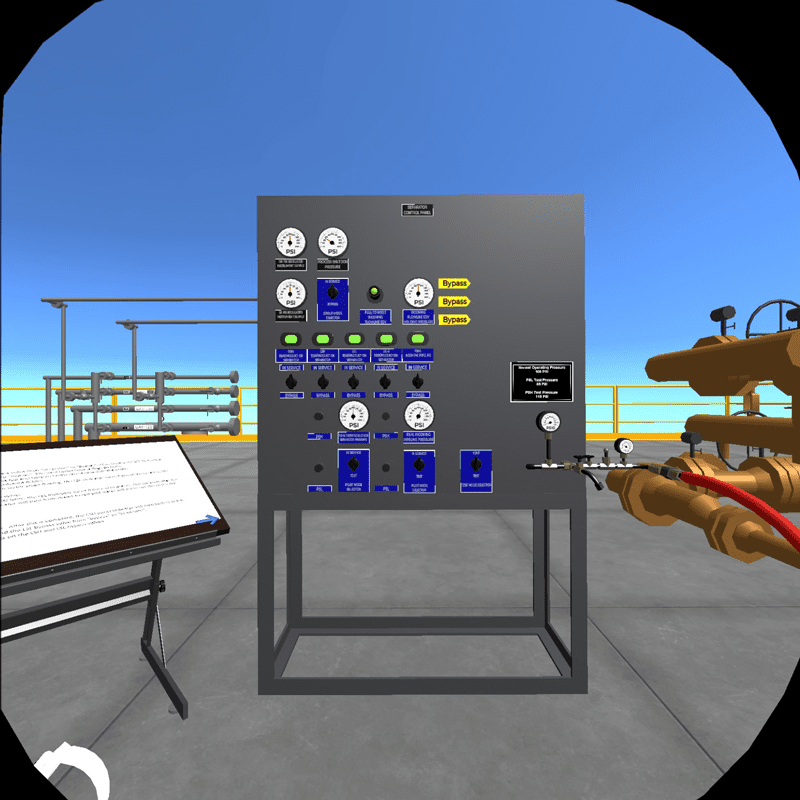
Organizations are investing billions of dollars in new technologies like virtual reality (VR), augmented reality (AR), and electronic tracking and management systems in hopes that it is effective in training workers. But companies are up against the time and risk involved to get workers up to speed.
As the digital revolution seeks to connect users through technology such as AR, VR and the Internet of Things (IoT), companies also face large room for error with the actual end user. This creates a wide variability in the one area where organizations have very little data – their people.
Service company Danos, with operations in the Gulf of Mexico, Permian and Delaware basins, Eagle Ford and Marcellus Shale plays, believes that it is eliminating this variability through a competency management system (CMS). Danos says that the web-based application allows it to manage the individual learning and development needs of its workforce in a way that is consistent with the expectation of its global customer base.
One technology enterprise Danos is partnering with is the newly established iCAN Technologies LLC. iCAN is Danos’ sole provider for competency solutions.
“Through partnership with iCAN, our CMS is designed to track and measure the competency profile of each field employee throughout his or her career with Danos,” says Competency Assurance and Training Manager Mark Theriot. “We can measure each individual’s unique training and competency level and track the employee’s career progression.”
According to Theriot, the platform can identify competencies for each skill set and provide the user with an unambiguous, competency-based roadmap to reach a desired role.
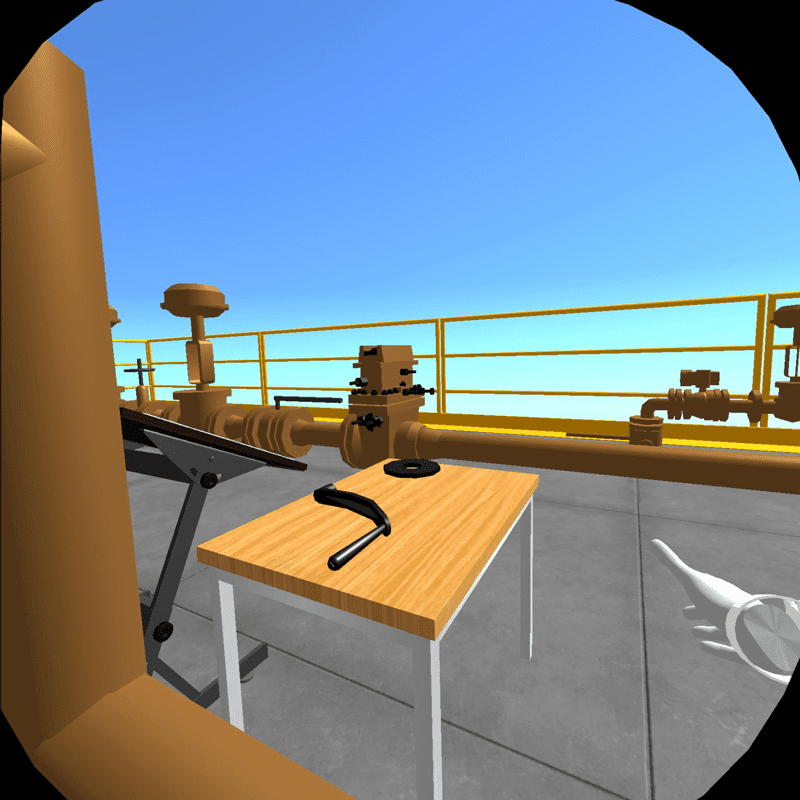
To enhance these competencies, Danos is using iCAN’s solutions to expedite learning and development through its computer-based training (CBT). Danos has invested in course development software to provide quality, CBT modules that were created by in-house subject matter experts. The CBTs encompass all typical skillsets the company employs in upstream, midstream and downstream. Developed using 3D-modeling technology, the courses feature interactive games, characters and voice narration, making training “fun, interesting and a step above your average instructor-led course,” says Theriot.
VR is also an important part of Danos’ program. Through collaborative efforts with technology partners, Theriot says the company has developed a complete virtual offshore platform. It features the major pieces of equipment found on an actual oil and gas producing facility and creates a safe environment in which the user can experience hands-on learning.
“This interactive platform allows our employees to be completely immersed in an offshore environment, identify equipment, perform tasks and explain processes to a qualified assessor,” says Theriot. “Employees can demonstrate their knowledge and skills in the same manner they would on real equipment, but in VR they can do this without consequences.”
“The competency, learning and training systems through iCAN are all intertwined, which allows us to perform regression analytics on all variables. In turn, this enables us to select best-in-class employees, develop them and measure performance to improve their work.”
When it comes to the skills and competency gap, iCAN believes the answer to the problem is fundamentally deeper than just presenting learning material in new ways.
“We see it in organizations in the oil and gas industry and beyond,” says David Decuir, partner at iCAN, “when an organization uses technology to satisfy training gaps, but misses out on determining the effectiveness of the training. They often fail to capture and analyze data, replace inefficient techniques or even invest more capital in the learning tools that are effective.”
iCAN looks at what it calls the “Human Internet of Things,” utilizing the same statistical, predictive algorithms that are applied to equipment through artificial intelligence and machine learning. However, the company takes those algorithms and applies them to the employee or end user’s technical aptitude.
“This allows organizations to determine not only who is competent but also what it takes for the next workers to become competent and ready in expedited form.”
iCAN says it is saving customers a minimum of 20 percent on training costs and in some cases as much as 40 percent. This is mainly because its scalable platform allows companies to analyze employee competency and the effectiveness of the training. Processes that at one time took trainers years to determine can now be done faster.
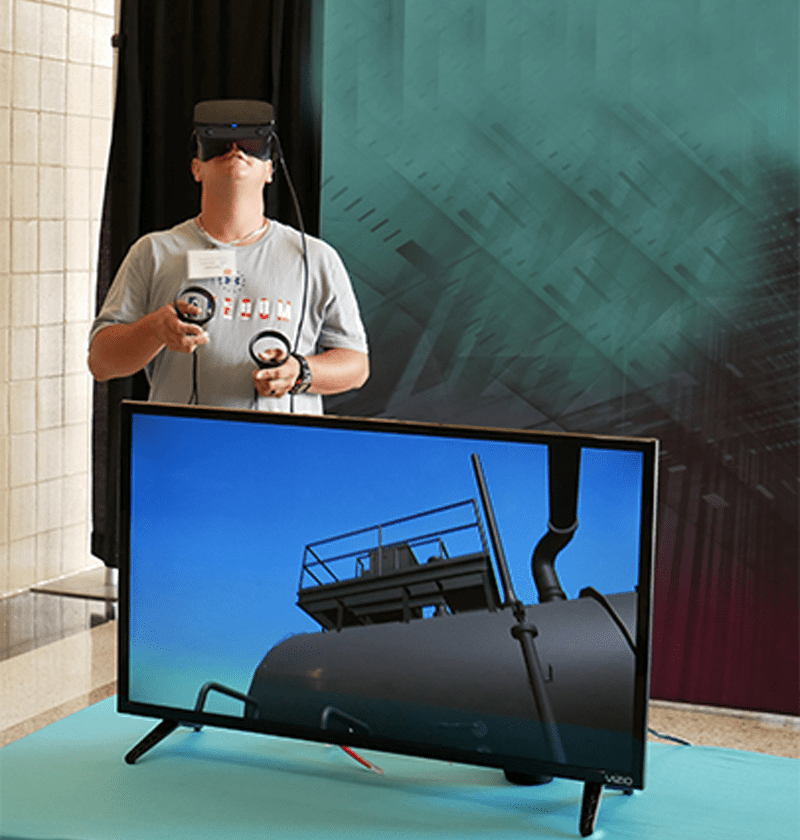
At the same time, Decuir says it eliminates the need for in-person assessments or group training sessions, both of which can incur significant costs in terms of time and money.
“By developing unit-based competency profiles for workers, organizations can identify holistically which training is working, what the largest gaps are and how to close those gaps,” says Decuir.
According to Decuir, iCAN has received positive feedback from its customers’ employees using the program, particularly regarding the VR and AR features of training.
“They love the idea of impactful training that breaks down the mechanics of the equipment and processes. Our technology gives people the ability to see what is happening internally on equipment, which is a game changer since humans are visual learners.”
Danos’ Theriot says that working with iCAN and other technology partners has introduced improvements to its training program.
“iCAN Technologies has given Danos the ability to pinpoint weaknesses in the workforce,” he says. “Rather than training or re-training employees with skills already mastered, we can look at the data, pinpoint areas of concern and train employees specifically in areas where they lack competency. This saves time and money but, most importantly, it improves competency and safety.”
iCAN has received positive feedback from customers regarding the available data analytics as well.
“The analytics allow customers to objectively view their workforce and empower employees. They can truly diversify their workforce based on data driven results, as opposed to an evaluator’s opinion,” Decuir says. “Obviously, they also appreciate the savings they see with our approach.”
Headline photo: iCAN and Danos are utilizing technology that gives users the ability to see the internal mechanics on platform equipment, like this heater treater vessel. This technology helps to expedite the learning curve during training as users can better understand equipment processes.
Samantha Magee joined Danos in 2018 as media relations coordinator. She has ten years of marketing and communication experience in oil and gas, education and non-profits. Magee holds a Bachelor of Arts in Mass Communication from Louisiana State University and an MBA from the University of Houston.
Oil and gas operations are commonly found in remote locations far from company headquarters. Now, it's possible to monitor pump operations, collate and analyze seismic data, and track employees around the world from almost anywhere. Whether employees are in the office or in the field, the internet and related applications enable a greater multidirectional flow of information – and control – than ever before.